При какой температуре сталь теряет свойства
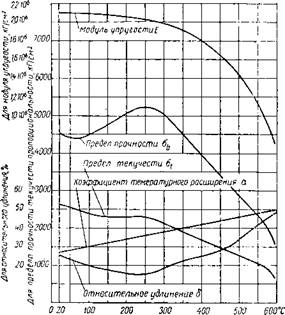
ВНУТРЕННИЕ УСИЛИЯ И ДЕФОРМАЦИИ ПРИ СВАРКЕ
Механические свойства металла изменяются в зависимости от его температурного состояния. В процессе сварки металл подвергается нагреву до высоких температур, изменение которых происходит в широких пределах и в сравнительно короткое время.
Механические характеристики металла при высоких температурах нельзя считать полностью исследованными. Более обстоятельно изучены механические свойства металла в области упругих изменений. На фиг. 9 представлено изменение механических характеристик стали в зависимости от температуры при нагреве до 500—600° С [2].
Модуль упругости стали Е при нагревании постепенно понижается, а коэффициент теплового расширения а возрастает. В области температур упругих изменений стали произведение аЕ можем принять постоянным и равным (хЕ = 12 • 10-6 • 2,1 • 106^ = 25 кГ/см2.
Предел прочности стали оь с повышением температуры до 100°С несколько снижается, затем при дальнейшем нагреве повышается и имеет наибольшее значение в области температур 200—300°С. При нагреве от 300 до 500°С предел прочности стали, кроме жароупорной, постепенно понижается. При температуре выше 500°С предел прочности стали резко снижается, принимая при 600°С весьма низкие значения по сравнению с прочностью при обычных температурах.
Пластические свойства стали, характеризуемые относительным удлинением и поперечным сужением при разрыве, неск(элько снижаются в области температур 150—300° С. С увеличением температуры выше 300°С пластические свойства стали возрастают. Такой характер изменения пластических свойств стали показывает, что при большой скорости остывания закрепленного стального элемента его разрыв при температурах 150—300°С весьма вероятен. Этим объясняется целесообразность предварительного подо-
21
грева стали при сварке до 150—200° С, чтобы замедлить остывание после сварки.
Предел текучести стали ст с повышением температуры до 500° С несколько понижается, а затем при дальнейшем повышении температуры (свыше 500°С) резко падает, доходя почти до нуля при температуре 600°С.
Фиг. 9. Зависимость механических свойств стали от температуры.
В действительности предел текучести стали несколько повышается в области температур 150—300°С, затем постепенно понижается при нагреве до 500° С, а после этого резко падает (фиг. 10, пунктирная кривая). Ввиду малых значений предела текучести стали при температуре 600°С и выше, примем допущение, что предел текучести сталей, кроме жароупорной, при температуре 600° С и выше имеет нулевое значение (фиг. 11). Другими словами, будем считать, что при температуре 600°С и выше сталь находится только в пластическом состоянии, теряя полностью свои упругие свойства.
При охлаждении стали ниже нуля предел прочности и предел текучести повышаются, причем предел текучести приближается к пределу прочности.
При весьма низкой температуре сталь теряет пластические свойства, переходит в хрупкое состояние и становится хладно-
Фиг. 10. Зависимость предела текучести аг стали
от температуры:
1 — схематизированная диаграмма; 2 — действительная диаграмма.
бгшКГ/СМ>
Фиг. 11. Условная зависимость предела текучести стали от температуры:
1 — схематизированная диаграмма; 2 — условная диаграмма.
ломкой. Для каждого металла существует своя критическая температура, выше которой металл способен пластически деформироваться, а при температурах ниже критических металл теряет способность к образованию пластических деформаций и разрушается в виде хрупкого излома. Для стали критическая температура, ниже которой происходит хрупкое разрушение, находится в области — 65—160° С.
Помимо низких температур, на хрупкое разрушение стали большое влияние оказывает концентрация напряжений, вызванная
Фиг. 12. Работа излома стали при разных температурах; а — ненадрезанные образцы; б — надрезанные образцы.
надрезами и неровностями. Хрупкое состояние стали может быть вызвано объемным напряженным состоянием, при котором весьма затруднено образование пластических деформаций.
На фиг. 12 приведены кривые ударной вязкости котельной стали в зависимости от температуры [3]. Кривые А соответствуют результатам испытаний стали, подвергавшейся предварительно нормализации для измельчения зерна, а кривые В соответствуют результатам испытаний крупно-зернистой стали.
Критическая температура ненадрезанных образцов для стали А— 160°С, а для стали В—90°С. При наличии надрезов критическая температура хрупкого разрушения значительно выше и для стали А равна +5° С, а для стали В +45° С (см. фиг. 12).
Для устранения деформаций после ‘сварки – применяется холодная и горячая правка сварных конструкций. Холодная правка основана на растяжении укороченных участков и мест сварной конструкции до проектных размеров – и форм. …
Образование остаточных напряжений и деформаций при сварке вызывается появлением внутренних усилий при местном нагреве металла. Оба эти явления находятся во взаимной связи, но проявляются при сварке конструкций в различной степени …
могут быть самые разнообразные и зависят от характера соединений и вида конструкции, применяемых методов сварки, режима нагрева, механических характеристик и химического состава свариваемых металлов. Как правило, для уменьшения пиков остаточных …
Источник
Как известно, не все металлы одинаковы, и температурное воздействие может менять их структуру по-разному. Но основная масса распространенных металлов приобретают пластичность при нагревании. Среди них: алюминий, железо, сталь, латунь и т.д. То есть, при воздействии температуры, они способны растягиваться, меняя свою структуру. В это время металл можно ковать, придавая ему любую форму по желанию мастера. Однако есть металлы, которые не обладают пластичностью при нагревании, и во время попытки их ковать, совершая удары, они могут просто трескаться и разрушаться. Среди них: цинк, серый чугун, сплав олова и бронзы, и др.
Поведение металлов при воздействии разных температур
Железо и сталь – самые популярные металлы, которые хорошо поддаются температурному воздействию и ковке. Однако, необходимо учитывать тот факт, что при воздействии разной температуры эти металлы и ведут себя по-разному. Например, если нагреть сталь до температуры чуть выше 900°С, то ковать ее будет 2,5 раза сложнее, нежели если нагреть металл до 1200 °С. Следовательно, чем меньше температура нагрева, тем сложнее ковать. Это логично. Но необходимо знать, что нагрев стали уже до 600 °С способствует изменению ее структуры и улучшается пластичность. Температуру регулируют в зависимости от вида работ, которые планируют проводить со сталью.
Интересный факт: при нагревании стали от комнатной температуры, например, от 15-20 градусов и до 600 °С процесс видоизменения металла происходит по-разному. На значении в 300 °С наступает первый предел прочности на растяжение, но в этот момент металл становится очень хрупким. И только после значения в 600 °С сталь можно начинать растягивать и ковать. Далее, чем выше поднимается температура, тем ниже падает прочность стали. При 1200°С-1300°С, в сравнении со сталью комнатной температуры, ее прочность падает в 30 раз.
Что касается цветных металлов и других сплавов, то температура плавления у них меньше, чем у стали, а значит и все значения уменьшатся. Например, алюминий становится в 30 раз менее прочным уже при нагревании до 600 °С. В таком состоянии их можно легко деформировать, не затрачивая при этом особых усилий.
Максимальная температура для снижения прочности металлолома
Если сталь нагревать сильнее, чем до 1300 °С, то начинается превращение металла в жидкую фазу. Для того, чтобы этого не случилось, на пунктах приема металлолома установлены специальные печи, с максимальной температурой 1400 °С. Если поднимать температуру выше этого значения, то сталь расплавится. Этого допустить нельзя, ведь при, так называемом, пережоге стали наблюдаются негативные реакции в следующей последовательности:
- Кристаллы и зерна металла начинают оплавляться;
- Проникновение кислорода в межкристаллическое пространство;
- Образование окиси железа на гранях зерен;
- Разрушение металла.
Все эти факторы приводят к порче материала и неисправному браку. Именно поэтому печь должна быть отрегулирована положенным образом, а металл должен находится в ней только определённое короткое время. Во избежание пережога.
Прием металлолома metprom-group.ru оснащен всей необходимой специализированной и современной техникой, как для транспортировки и погрузки лома, так и для его дальнейшей обработки. Также, компания предлагает услуги вывоза лома с территории заказчика и очень выгодные цены. Сдав ненужный лом, вы сможете не только подзаработать, но и дать металлу вторую жизнь, сэкономив, таким образом, ценные ресурсы.
Источник
Методы исследования термических поражений изделий из металлов и сплавов.
Деформация – один из самых низкотемпературных процессов, происходящих с металлическими изделиями на пожаре.
Нагрев стали свыше 300-350 оС приводит к повышению ее пластичности и сопровождается снижением прочности и появлением заметных деформаций. При 500-600 оС прочность углеродистой стали снижается вдвое, деформации нагруженных элементов стальных конструкций становятся значительными по величине и 15-20 минутный нагрев может привести к их обрушению. При 1000 оС прочность стали снижается в 10 раз.
Помимо стали несущие конструкции изготавливаются также и из алюминиевых сплавов. Температура потери несущей способности конструкций из алюминиевых сплавов составляет 250 оС.
Разумеется, при этом конструкция не разрушается полностью. Она просто перестает выполнять свою функцию выдерживать нагрузку других конструктивных элементов здания или сооружения. В первую очередь она гнется, деформируется. Эти деформации при осмотре места пожара необходимо оценивать количественно. Оценка величины и направленности деформаций дает важную информацию об относительной интенсивности и направленности теплового воздействия в различных зонах пожара.
По направлению деформации металлических элементов можно судить о направлении наибольшего теплового потока. Металлоконструкции и их отдельные элементы деформируются, как правило, в сторону наибольшего нагрева.
Величина деформации металлической конструкции пропорциональна температуре и длительности ее нагрева. Однако часто наибольшая деформация наблюдается не там, где имело место наибольшее тепловое воздействие. Она может быть связана с более высокой нагрузкой, испытываемой конструкцией. Например, чаще всего стальная балка перекрытия имеет наибольшую деформацию посередине пролета, что вовсе не означает, что именно в этой точке был наиболее интенсивный нагрев. В этом месте на балку действует наибольший изгибающий момент. Количественно сравнивать между собой можно лишь рассредоточенные по месту пожара однотипные и одинаково нагруженные конструкции. Такую сравнительную оценку необходимо рассматривать как важный признак направленности распространения горения.
Для количественной оценки степени деформации, рассчитывают так называемую величину относительной деформации, представляющую собой отношение величины абсолютной деформации к длине участка конструкции, на которой эта деформация наблюдается (b/l) (рисунок).
Если деформация наблюдается на нескольких однотипных конструкциях, то сравнительные данные об относительной деформации характеризуют распределение зон термических поражений на месте пожара и относятся к группе последовательно нарастающих (убывающих) термических поражений.
Ярко выраженные и значительные по величине локальные деформации металлоконструкций на отдельных участках, относящиеся к группе произвольно расположенных термических поражений возникают, как правило, на начальной стадии пожара, когда горения во всем объеме помещения еще нет, и конструкции нагреваются от очага пожара в ограниченной локальной зоне. Если указанное локальное термическое поражение не находит иного логического объяснения оно должно рассматриваться как признак очага пожара.
Окислы на поверхности стальных изделий.
На гладких отполированных поверхностях стальных изделий, нагретых до температуры 200-300 оС можно визуально различить так называемые цвета побежалости. Они представляют собой пленки окисла микронной толщины и окрашены за счет интерференции света в разные цвета в зависимости от толщины слоя окисла. Толщина слоя, в свою очередь, увеличивается с увеличением температуры нагрева. Примерная цветовая шкала цветов побежалости на сталях выглядит следующим образом (рис. 7).
Источник
При нагреве металла возрастает подвижность атомов, увеличивается амплитуда колебаний, ослабляются межатомные связи, облегчается обмен местами и переход атомов в новые положения. Все это существенным образом влияет на изменение физико-химических и механических свойств металлов и сплавов.
Вольфрам и молибден промышленной чистоты не пластичны при комнатной температуре. Переход вольфрама из хрупкого состояния в пластичное колеблется в интервале температур 150-450° С, причем разрушение носит главным образом межкристаллитный характер. Молибден в зависимости от чистоты переходит из хрупкого в пластичное состояние в интервале температур 20-300° С.
На температуру перехода наряду с другими факторами влияет размер зерна в металле: чем мельче зерно, тем ниже температура этого перехода. Ниобий и тантал обычной чистоты обладают хорошей пластичностью при температурах ниже комнатной.
При нагреве до высоких температур заметно изменяются физико-механические свойства тугоплавких металлов. Поскольку механические свойства тугоплавких металлов при высоких температурах зависят от среды испытаний, в данном разделе приводятся свойства, полученные испытанием в нейтральной среде или в вакууме.
Сравнение высокотемпературной прочности нелегированных вольфрама, молибдена, ниобия и тантала показывает, что вольфрам отличается наибольшей прочностью при всех температурах, в то время как тантал занимает среднее по прочности место между ниобием и молибденом.
Образцы были изготовлены из прокатанного и полностью рекристаллизованного материала. В зависимости от содержания примесей абсолютные значения могут несколько меняться, но характер кривых принципиально остается одинаковым.
Кривые показывают интенсивное увеличение предела текучести вольфрама при понижении температуры от 350 до 175° С, т. е. в интервале перехода из пластичного состояния в хрупкое. Примерно в этом же интервале температур резко увеличивается удлинение, а прочность снижается более равномерно. Снижение твердости происходит одинаково как для наклепанного, так и для отожженного металла. Твердость вольфрама и молибдена при нагреве до 327° С резко падает, однако при дальнейшем повышении температуры твердость изменяется с меньшей интенсивностью.
Представляет интерес изменение механических свойств полуфабрикатов тугоплавких металлов при высоких температурах после деформации. Например, прочность молибденовой проволоки диаметром 0,6 мм с повышением температуры падает, но даже при температуре 1400° С остается высокой и составляет 500 Мн/м2 (50 кГ/мм2). Прочность этой же проволоки при комнатной температуре после деформации ~90-95% составляет 1150 Мн/м2 (115 кГ/мм2).
С уменьшением содержания примесей предел прочности понижается почти в два раза при всех температурах, оставаясь все же значительным по величине 140 Мн/м2 (14 кГ/мм2) даже при 1500° С. Одновременно повышается пластичность, достигая при 1500° С 50,8%. Зависимость твердости ниобия от температуры приведена на рис. 45. С повышением температуры твердость ниобия резко снижается. При температуре 1173° С на кривой твердость — температура у литого ниобия наблюдается максимум, а у металлокерамического ниобия три максимума — при 777, 927 и 1127° С.
Дальнейшее повышение температуры вызывает понижение твердости, и при 1850° С твердость металлокерамического и литого ниобия совпадает и составляет небольшую величину: при 2027° С • 1 Мн/м2 (0,1 кГ/мм2), а при 2127° С всего 8,2 Мн/м2 (0,82 кГ/мм2).
Примечание. Тантал листовой толщиной 1,27 мм получен из штабика с содержанием примесей, % (по массе): 0,02 С; 0,013 N2; 0,056 02; 0,1 Nb; 0,01 W; 0,015 Fe.
Влияние температуры на изменение механических свойств тантала приведено. При температуре 400° С наблюдается «пик», вызванный процессом деформационного старения. — Твердость тантала при повышении температуры также снижается.
Важным показателем является удельная прочность тугоплавких металлов при высоких температурах. На рис. 46 показано изменение удельной прочности вольфрама, молибдена, ниобия и тантала в зависимости от температуры. До температуры 1320°С ниобий и молибден имеют значительное преимущество по удельной прочности по сравнению с вольфрамом и танталом, а выше этой температуры наибольшую удельную прочность имеет вольфрам.
Одной из характеристик тугоплавких металлов при высоких температурах является ползучесть или свой ство металла пластически деформироваться при высоких температурах под действием постоянных напряжений. Для оценки ползучести (жаропрочности) металла образцы испытывают при температуре под действием постоянных напряжений и определяют изменение длины в зависимости от времени. На основании исследования строят кривую текучести.
При этом определяют: а) предел текучести — напряжение, вызывающее при данной температуре определенную, допустимую для нормальной работы конструкции скорость или значение деформации. Например, 0,1% за 100 ч, 0,2% за 1000 ч и т. д.;
б) предел длительной прочности- напряжение, приводящее при данной температуре к разрушению за данный период времени — 100, 200, 20 000 чит.д.
Длительная прочность некоторых тугоплавких металлов при 1095°С показана на рис. 48. Как видно, ЮО-ч прочность рекри-сталлизованного молибдена дуговой плавки составляет 84 Мн/м2 (8,4 кГ/мм2), а прочность вольфрама при этих условиях почти в два раза превышает прочность молибдена и равняется 155 Мн/м2 (15,5 кГ/мм2).
Пластические, технологические и другие свойства тугоплавких металлов заметно изменяются под воздействием термической обработки. Основным видом термической обработки является отжиг, который подразделяют на три вида: гомогенизацию, возврат, полный рекристаллизационный отжиг.
Гомогенизация — это такой вид отжига, который применяется для дегазации и устранения химической и структурной неоднородности слитков, деформированных заготовок и полуфабрикатов. Гомогенизирующий отжиг часто применяют для слитков и прессованных изделий из вольфрама, молибдена и ниобия. Для этого слитки длительно нагревают перед обработкой при температурах, близких к началу оплавления. Вследствие высокой подвижности атомов (диффузии) при таком нагреве структура слитка становится более однородной.
Например, слитки ниобия, выплавленные в дуговых печах и содержащие значительное количество примесей, при неоднородной структуре подвергают отжигу при 1800-2000° С в вакууме 13,3-1,33 мн/м2 (10-*- 10~5 мм рт. ст.) и выдерживают до 10 ч. Такой отжиг приводит к уменьшению газосодержания в слитке. Одновременно с дегазацией происходит растворение избыточных фаз и структура становится более однородной. Однако следует учитывать, что длительный отжиг ниобия при высоких температурах приводит к росту зерна в слитках.
Гомогенизирующий отжиг прессованных и кованых заготовок из ниобия производят при температуре 1350- 1450° С, когда происходит заметное растворение карбидных и других фаз, и в то же время не наблюдается сильного роста зерна. Гомогенизация заготовки благоприятно сказывается на технологических свойствах при последующей обработке.
Возврат или неполный отжиг применяют для частичного снятия остаточных напряжений, искажений кристаллической решетки, возникающих в заготовках и изделиях при различных операциях обработки давлением. В результате такого процесса повышается пластичность металла. Микроструктура металла не изменяется.
Степень возврата зависит от температуры, скорости и степени предварительной деформации, продолжительности и температуры отжига. При возврате, по мнению многих исследователей, число дислокаций не изменяется, а изменяется преимущественно их распределение, которое становится более равномерным.
Рентгеноструктурные исследования деформированного ниобия показывают, что в металле имеются значительные остаточные напряжения и сильно выраженная текстура (наличие на рентгенограмме размытых линий). Это состояние сохраняется и после получасового отжига при 900° С. Отжиг при 1000° С в течение получаса приводит к значительному снятию напряжений в решетке (уменьшение толщины размытых линий на рентгенограмме).
Однако при указанном времени отжига повсеместного снятия напряжений еще не происходит (отдельные линии остаются размытыми), на кольцах рентгенограммы сохраняются текстурные уплотнения, характеризующие предпочтительную ориентировку зерен в металле. После двухчасовой выдержки при 1000° С возврат практически полностью заканчивается, все линии рентгенограммы становятся четкими с хорошо выявленным дублетным строением. Рефлексов от рекристаллизованных зерен не наблюдается. Таким образом, нагрев при 1000° С в течение 2 «является оптимальным режимом для отжига-возврата деформированного ниобия.
Ниобий, отожженный по указанному режиму, имеет следующие механические свойства:— ав = 560 Мн/м2 (56 кГ/мм2); ат = 480 Мн/м2 (48 кГ/мм2); 6 = 17%, тогда как в исходном деформированном состоянии ав = = 650 Мн/м2 (65 кГ/мм2); ат = 570 Мн/м2 (57 кГ/мм2); 8=7%.
Отжиг-возврат рекомендуется применять к изделиям и полуфабрикатам, предназначенным для работы при температурах ниже температуры рекристаллизации.
Рекристаллизационный отжиг применяют как промежуточный процесс между операциями холодной обработки (для снятия наклепа и устранения текстуры) или как окончательную операцию термообработки, (для придания полуфабрикатам или изделиям необходимых свойств).
Физическая природа рекристаллизации состоит в том, что при увеличении температуры деформируемого металла поднимается энергетический потенциал атомов так, что последние получают возможность перегруппировок и обмена местами. С. С. Горелик определяет рекристаллизацию как процесс повышения структурного совершенства и уменьшения свободной энергии металлов и сплавов в пределах данной фазы, совершающийся путем возникновения и движения (или только движения) границ с большими углами ориентировки. Это наиболее полное определение процесса, охватывающее все его стадии.
Источник