Какой конечный продукт металлургии
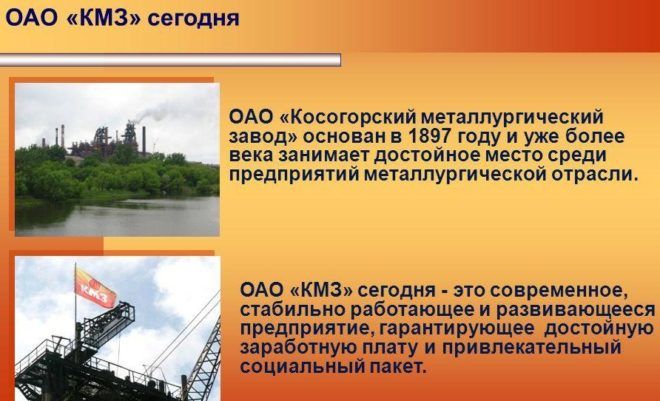
Массовые производства металлов долгие годы являлись мерилом промышленной развитости стран (их экономическом и военном могуществе).
Металлургия это фундамент для производства всевозможных машин. Часть сырья идет в строительство на разнообразные инфраструктурные объекты.
Несмотря на переход на так называемую стадию постиндустриализма (информационнного общества) металлы остаются нужны для всевозможных сборок ЭВМ, гаджетов, умной бытовой техники и другой электроники, в будущем для массовой робототехники.
Не куда не делась и классическая инфраструктура из металлов, она просто стала более электрофицируемой и взаимосвязанной с интернетом.
Все это в конечном итоге определяет хозяйственный облик страны в целом.
Постоянные спутники металургической промышленности – – теплоэнергетика и машиностроительный комплекс (в первую очередь крупногабаритные изделия требующие много конкретного металла)
Металлургический комплекс России
В составе металлургической сферы находится:
- Черная металлургия (железо и производные от него металлы, чугун, сталь, прокат и др.)
- Цветная металлургия (свыше 70 металлов – аллюминий, титан, магний, медь, свинец, никель, цинк, олово и др.)
Среди предприятий черной металлургии выделяют:
- Комбинаты полного цикла (чугун, сталь, прокат). Таких предприятий в РФ большинство.
- Заводы неполного цикла (что то одно или 2 из 3 основных металлов)
- Малая металлургия (переплавленние отходов с машиностроительных заводов)
Цветная металлургия определяет свою структуру в соответствии с разнообразием добываемых металлов. Цветные металлы требуются для авиационной, космической, электротехнической промышленности.
Географически у России сейчас созданы и работают 3 металлургических базы:
- Уральская металлургическая база (Урал остается крупнейшей металлургической базой России)
- Центральная металлургическая база (Великороссия)
- Сибирская металлургическая база (самая молодая с возможностью расширения)
Дальний Восток несмотря на то что имеет на это все возможности пока к сожалению индустриально не освоен в плане металлургии.
Заводы-гиганты VS мобильные заводы
Челябинский металлургический комбинат делает город одним из самых суровых городов России, но в то же время серьезно влиет на здоровья горожан и экологию в целом.
Как правило чем крупнее предприятие тем оно более мощно по своим промышленнным возможностям и тем дешевле в итоге может производить продукцию.
С другой стороны концентрация в одном месте повышает затраты на перевозки, повышает концентрированное загрязнение окружающей среды ( металлургия это одна из самых “грязных” отраслей народного хозяйства). В быстро меняющемся современном мире с его постоянными инновациями гигантам труднее идти в ногу со временем, а также приспосабливаться к заказчикам – то есть быстро модернизироваться.
Поэтому отметим что все же с учетом развития технологий и повышения их отдачи (когда даже малый завод может выпускать столько же что и комбайн-диназавр XX века) – заводы-динозавры проигрывают мобильным заводам, за ними следует признать будущее и направлять действия в соответствии с этой веткой развития.
В частности есть замечательная книга к данной сфере “К.Кристиансени и М.Рейнор “Решение проблемы инноваций в бизнесе” рассмматривающая пример электрометаллургических мини-заводов превосходящие старые комбинанты-гиганты по всем параметрам.
Также отметим нанотехнологическое завтро которое будет способно создавать любые металы и любые изделия из них буквально из песка и глины просто манипулируя атомами (подробнее здесь).
Всё это свидетельствует о наступлении революции в металлургической промышленности, а в любой революции главное быть в тренде и успеть стать первыми закрыв старую эпоху через начало новой.
Резюме
В современной национальной экономики все сферы взаимосвязанны друг с другом.
В РФ сегодня 3 металлургические базы, которые должны пополниться ещё одной Дальневосточной (Рутенской) через новую мобильную индустрилизацию данного макрорегиона.
Приоритет в в будущем развитии направлен на технологии переворачивающие мир и делающие не нужным сразу целые отрасли промышленности. Мы созданим доселе неизвестные продукты которые сразу оборвут прежние линии научно-технического прогресса и начнем свою новую историю породив эти новые Миры в которых сразу станем лидерами.
Источник
Цветная металлургия является комплексной отраслью промышленного производства. Ассортимент товарной продукции предприятий цветной металлургии достаточно широк и разнообразен. Это:
· цветные металлы и сплавы в виде слитков, катодов, проката и т.д.
· химическая продукция: серная кислота, элементарная сера, медный и никелевый купорос, кальцинированная сода, поташ, различные химические реактивы (соли, оксиды, гидроксиды и т.д.);
· минеральные удобрения: суперфосфат, амофос и др.;
· строительные материалы: цемент, минераловатные и асбошиферные изделия, щебень, гранулированный шлак, шлаковая брусчатка и т.д.;
· тепловая и электрическая энергия;
· кислород и аргон.
Кроме товарной продукции на предприятиях цветной металлургии получают многочисленные отходы и полупродукты металлургического производства, свойства и качества которых весьма важны для технологических процессов цветной металлургии. К ним относятся шлаки, штейны, пыли, газы, агломераты и спеки, кеки, шламы, растворы и т.д. Рассмотрим общие характеристики некоторых основных продуктов и важнейших полупродуктов металлургической технологии, получающихся при переработке большинства сырьевых материалов.
Металлы
Металлы являются основным видом товарной продукции металлургического производства. В цветной металлургии в зависимости от применяемой технологии и состава получающихся металлов различают черновые и рафинированные металлы. Товарной продукцией, поступающей к потребителю для дальнейшего использования по прямому назначению, как правило, являются рафинированные металлы.
Черновыми металлами называются металлы, загрязненные примесями.
В число примесей входят вредные и ценные элементы – спутники основного металла. Вредные примеси ухудшают характерные для данного металла свойства (электропроводность, пластичность, коррозионную стойкость и т.п.) и делают их непригодными для непосредственного использования. Ценные спутники – благородные металлы, селен, галий, индий, рений и многие другие необходимо попутно извлекать из-за их достаточно высокой цены.
После очистки (рафинирования) черновых металлов от примесей получают рафинированные металлы. В зависимости от качества очистки и конечного содержания в рафинированном металле примесей устанавливают марку металла. Чем чище металл, тем выше его стоимость (за счет высоких затрат на его очистку). В небольших количествах некоторые предприятия цветной металлургии выпускают металлы повышенной (особой) чистоты. Получение таких металлов связано с большими дополнительными затратами труда, времени и средств, поэтому выпуск их ограничен.
Штейны
Штейном называется сплав сульфидов тяжелых цветных металлов (меди, никеля, свинца, цинка и др.) с сульфидом железа, в котором растворены примеси.
Штейны являются промежуточным металлсодержащим продуктом, получение которых характерно для пирометаллургии меди6 никеля и частично свинца.
В практике цветной металлургии получают медные, медно-никелевые и полиметаллические штейны.
Примерный состав заводских штейнов
Штейн | Cu | Ni | Pb | Zn | Fe | S |
Медный | 10-60 | до 0.5 | до 1 | 1-6 | 30-50 | 23-26 |
Медно-никелевый | 5-10 | 5-13 | 40-60 | 24-27 | ||
Никелевый | 0.1-0.3 | 12-60 | 55-10 | 15-22 | ||
Полиметал. | 10-30 | 10-20 | 5-10 | 20-40 | 13-22 |
Они образуются в жидком состоянии и практически не смешиваются с жидкими шлаками, что позволяет отделять их друг от друга путем отстаивания. Для успешного разделения штейнов и шлаков необходимо, чтобы разность их плотностей была не менее 1 (г/см3). Чем она больше, тем при прочих равных условиях (вязкость шлака, крупность штейновых капель) быстрее идет отстаивание.
Основными компонентами медных штейнов являются сульфиды меди и железа – Cu2S и FeS. В медно-никелевых штейнах преобладают Ni3S2, Cu2S и FeS. Характерными особенностями медных и медно-никелевых штейнов являются примерно постоянное содержание в них серы и присутствие некоторого количества кислорода (до 3-6 % в бедных штейнах) в форме оксидов железа – FeO и Fe3O4.
Медные и медно-никелевые штейны являются хорошими растворителями (коллекторами) всех благородных металлов. Кроме того, в зависимости от состава исходного сырья они могут содержать небольшие количества селена, теллура, мышьяка, сурьмы, висмута, кадмия и других примесей.
В отличие от медных и медно-никелевых штейнов содержание серы в никелевых штейнах колеблется более существенно. Это связано с тем, что никелевые штейны, как правило металлизированы, т.е. помимо сульфидов в них содержатся в растворенном виде и чистые металлы (Ni, Fe). Чем выше металлизация штейна, тем меньше в нем содержание серы. Кислорода в металлизированных никелевых штейна практически нет.
Металлургические шлаки.
Шлаки являются вторым жидким (в редком случае твердым) продуктом большинства металлургических плавок.
Шлаки – это сплав оксидов, образующийся, главным образом, из компонентов пустой породы и флюсов и продуктов окислительных реакций.
Кроме шлакообразующих компонентов, реальные заводские шлаки содержат и некоторое количество извлекаемых металлов. При плавке на штейн в шлаках также присутствует небольшое количество сульфидов.
При относительно низком содержании ценных компонентов в большинстве рудных плавок шлаки являются отвальным продуктом, т.е. отходами металлургического производства. Однако в будущем, с развитием металлургической техники они могут вновь стать ценным сырьем для получения ряда цветных металлов, а также железа и других ценных составляющих.
Основными компонентами шлаков цветной металлургии являются SiO2, FeO и CaO. Суммарное содержание этих трех оксидов обычно составляет от 70 до 90 -95 %. Концентрация CaO редко превышает 6-8 %. В большинстве случаев, таким образом, шлаки цветной металлургии в основе своей являются железосиликатными (FeO-SiO2).
В ряде процессов цветной металлургии в зависимости от состава перерабатываемого сырья и применяемой технологии в металлургических шлаках может содержаться Al2O3, MgO, Fe3O4, ZnO и некоторые другие оксиды.
К числу важнейших физико-химических свойств шлаковых расплавов, влияющих на показатели плавки, относятся плавкость, вязкость, плотность, поверхностные свойства и растворимость в шлаках металлсодержащего продукта (основные свойства физико-химические свойства металлургических расплавов будут рассмотрены далее в настоящем курсе). Физико-химические свойства шлака оказывают значительное влияние на показатели металлургического процесса. В свою очередь, на свойства шлака значительное влияние оказывают его состав и температура.
Сильное влияние состава шлака и температуры на его свойства приводят к необходимости в каждом металлургическом процессе подбирать оптимальный состав шлаков, который должен удовлетворять определенным технологическим и экономическим требованиям. Далеко не всегда плавка исходного сырья обеспечивает получение оптимальных шлаков. В большинстве случаев состав шлака приходится корректировать введением в исходную шихту соответствующих флюсов – минеральных добавок (кварцевые материалы, известняк и др.).
Не нашли то, что искали? Воспользуйтесь поиском гугл на сайте:
Источник
Металлургический комплекс занимает третью позицию в структуре промышленного производства и относится к базовым отраслям индустрии. Черная металлургия играет важную роль в развитии экономики любой страны.
Ее отраслевой состав включает организационные и технологические мероприятия по производству стали, чугуна и проката. Кроме того, она включает в себя:
- добычу, обогащение руд;
- получение нерудного и вспомогательного сырья для этой отрасли;
- вторичный передел;
- изготовление огнеупоров;
- металлоизделий производственного назначения;
- коксование угля.
Продукция черной металлургии нашла применение в большинстве сфер экономики. Главные ее потребители – машиностроительная, металлообрабатывающая индустрия, строительство, железнодорожный транспорт. Она взаимосвязана также с легкой и химической промышленностью.
Черная металлургия, динамично развивающаяся отрасль. Но это сложная производственная сфера и у России довольно сильные конкуренты в лице Японии, Украины, Бразилии. Ей удается сохранять одну из лидирующих позиций, при этом выгодно выделяться низкой себестоимостью. В сфере добычи железной руды, а также выплавки чугуна и коксового производства ей удалось добиться наибольших успехов. Этому способствует постоянное совершенствование технологических процессов, разработка стратегических планов и совершенствование антикризисного управления.
Типы и особенности предприятий
Природная основа черной металлургии – топливо и металлическое сырье.
Россия богата на ископаемые и сырье для развития этой отрасли, но их территориальное размещение неравномерно. Поэтому строительство комбинатов имеет привязку к определенным районам. Выделяют три типа черной металлургии, от них непосредственно зависит географическое положение производственных комплексов:
- металлургия полного цикла, подразумевающая присутствие всех производственных этапов, которые осуществляются на территории одного предприятия;
- металлургия неполного цикла отличается тем, что один из процессов выделен в отдельное производство;
- малая металлургия, которая характеризуется отдельными металлургическими цехами в составе машиностроительных комплексов.
Полный цикл производства включает в себя как основное производство чугуна, стали, проката, так и подготовительный этап к плавке железных руд – ее обогащение для повышения содержания в ней железа. Для этого удаляется пустая порода и обжиг для устранения фосфора, углекислоты, серы.
Для обеспечения качества конечного продукта необходимо применение следующих компонентов:
- технологического топлива;
- воды;
- легирующих металлов;
- флюсов;
- огнеупорных материалов.
В качестве топлива в основном выступает кокс из высококалорийного, малозольного, малосернистого и высокопрочного угля, а также газ. Металлургические предприятия полного цикла в большинстве своем размещаются поблизости к топливным, сырьевым и водным ресурсам, а также к вспомогательным материалам.
При производстве 90% затрат идут на топливо и сырье. На кокс из них приходится – около 50%, на железную руду – 40%. Предприятия полного цикла располагаются близко к сырьевым источникам – в Центре и на Урале, топливным базам – комплексы на Кузбассе, а также заводы между пунктами – в Череповце.
Полный цикл
В металлургии неполного цикла акцент делается на одном виде продукции – чугун, сталь или прокат. Передельные предприятия – отдельная группа, специализирующаяся на изготовлении стали без выплавки чугуна, в нее входят также трубопрокатные заводы.
Расположение таких производств зависит от близости к источникам вторсырья и потребителям готовой продукции. В случае с машиностроительными заводами – это одно лицо, поскольку они и потребители, и источники металлолома.
Для малой металлургии, являющейся частью предприятий машиностроения, как понятно из расположения, основной ориентир – потребители.
Изготовление ферросплавов и электростали также входит в состав черной металлургии.
Первые – сплавы с легирующими металлами такими, как ферросилиций, феррохром. Их производят на передельных предприятиях (чугун-сталь, чугун) либо заводах полного цикла.
Они важны для развития качественной металлургии. Получение их происходит электрометаллургическим путем на специализированных заводах, но при этом расходуется большое количество электроэнергии – на 1 тонну нужно до 9 тыс. кВт-ч. Изготовление электросталей наиболее развито в областях необходимого скопления металлолома и источников энергии.
В современном машиностроении, которое нуждается в металле разных марок, высокого качества, ограниченных партиях особым спросом пользуется продукция мини-заводов. Они не требуют больших мощностей, способны в оперативном порядке осуществить выплавку конкретного металла в небольшом количестве.
Их преимущество – быстрая реакция на изменения конъюнктуры рынка, максимальное удовлетворение потребительских запросов и высокое качество получаемой стали, особенность плавки прогрессивным электродуговым методом.
Получение и применение чугуна и стали
Металлургические базы: характеристики и размещение
Металлургические предприятия, пользующиеся общими ресурсами – топливом и рудой, обеспечивающие страну нужным объемом металла называются металлургическими базами. Старейшая из них расположена на Урале. Она еще с XVIII века выплавляет наибольший объем чугуна, стали в России и по сей день остается лидером.
Следующие позиции занимают Центральный и Северный район, а также Сибирь и Дальний Восток. Кроме того, за пределами основных, расположены другие центры черной металлургии – «Северсталь» (Череповец) комбинат полного цикла, а также передельного типа – в Поволжье, на Северном Кавказе.
Уральская черная металлургия использует привозное топливо – кузнецкий, карагандинский уголь, а ископаемые, добываемые в Кизеловском бассейне, могут применяться лишь в смеси.
Поставки сырья осуществляются из Казахстана, а также с Курской магнитной аномалии. Собственная сырьевая база представлена, перспективно развивающимися, Качканарским и Бакальским месторождением.
На Урале много железной руды, которая содержит легирующие компоненты, а также в месторождении «Полуночное» имеются залежи марганцевых руд.
Ведущая роль в этом районе у предприятий полного цикла, при этом сохранились и развиваются мелкие заводы.
Предприятия неполного цикла преимущественно расположены на западных склонах. Особенность региона в том, что только там производят выплавку природно-легированных металлов и чугуна на древесном угле.
Центральная металлургическая база пользуется привозным топливом. Добыча руды преимущественно осуществляется в Курской, Белгородской области. Большая часть стали, чугуна выплавляется Новолипецким комбинатом – в одном из самых крупных и технологически развитых в России.
Особый интерес представляет завод, расположенный в Старом Осколе, на котором железо и электросталь изготовляют из железорудного концентрата посредством химического восстановления, при этом минуя этап выплавки чугуна.
Особенности метода
Этот прогрессивный метод не требует использования кокса, большого водопотребления, что важно для района с дефицитом пресных вод и собственных топливных ресурсов. К крупным чугунолитейным, сталелитейным и сталепрокатным металлургическим заводам относятся:
- Новотульский;
- «Электросталь»;
- предприятие в Орле;
- Косогорский.
Менее мощные сталелитейные заводы в Волго-Вятском районе: Выксунский, Кулебакский, Омутнинский. Центральный район славится малой металлургией и имеет огромный плюс – расположение рядом с железорудным бассейном, а также соседство с центрами машиностроения и другими потребителями.
Сибирская и Дальневосточная металлургические базы работают на кузбасском угле, а также железных рудах Горного Алтая, Приангарья.
Там расположены заводы, комбинаты полного цикла – Кузнецкий и Западно-Сибирский.
Передельные заводы работают в следующих городах:
- Красноярк;
- Комсомольск-на-Амуре;
- Забайкальск;
- Новосибирск.
Занимающийся выпуском строительных и машиностроительных профилей металлопроката «Западно-Сибирский металлургический комбинат» производит 44% общего объема арматуры и 45% – проволоки, а также отправляет продукцию на экспорт в 30 стран мира.
Выплавка ферросплава – ферросилиция происходит на крупнейшем в России Кузнецком заводе ферросплавов.
Процесс производства черной металлургии
Состояние рынка и тенденции развития отрасли
В России объем экспорта в черной металлургии превосходит внутреннее потребление. На долю производства непосредственно влияет возможность экспорта, а также уровень конкуренции и торговой политики импортеров.
Если снижается экспорт, происходит и сокращение инвестиционной активности, а соответственно активное развитие этой сферы. При таких обстоятельствах отрасль больше зависит от внутреннего спроса – производств, нуждающихся в этой продукции.
Основной тенденцией перспектив отрасли становится переход к более качественной и чистой черной металлургии.
Приходит время экономно-легированных сталей, отличающихся большим пределом прочности.
Изготовляемые конструкции получаются металлоемкими и имеют длительный срок эксплуатации.
В развитии сферы черной металлургии актуальными становятся следующие направления:
- Модернизация, использование новейших технологий, переориентация предприятий, чья продукция неконкурентоспособна. Основными производителями останутся Череповецкий, Магнитогорский, Нижнетагильский, Кузнецкий, Новолипецкий, Челябинский и другие крупные трубные заводы.
- Рост доли передельных металлургических производств, поскольку такой металл дешевле. Перспективно создание мини-заводов, максимально ориентированных на нужды потребителей. Они способны обеспечить высококачественными металлами, быть узкоспециализированными и выполнять небольшие заказы.
- Ориентация на потребителей, что связано с развитием научно-технического прогресса, усовершенствованием методов обогащения руд, большим скоплением вторсырья в старопромышленных районах.
- Строительство заводов вдали от густонаселенных районов, так как большее значение уделяется мероприятиям по охране природы и экологической безопасности.
- Закрытие заводов, где на «нижних» этажах до сих пор используется устаревшее оборудование.
- Усиление специализации заводов для улучшения качества сталей, сложных видов проката. Начнется активность производств металла для транспортной, строительной, автомобильной и электронной отраслей.
Технологии и безопасность производства
Темпы технологического перевооружения российской черной металлургии превышают другие промышленные отрасли.
Проведенная в последние годы модернизация базовых переделов позволила снизить издержки производства, что и является основным конкурентным преимуществом.
А также повысилась энергоэффективность, потребность в ресурсах, что привело к снижению энергозатрат на экологически вредной мартеновской выплавке стали, которая теперь производится на конверторных, а также электросталеплавильных мощностях.
Одна из насущных проблем на этой стадии развития металлургии – это рациональное природопользование и обеспечение безопасности окружающей среды. При работе оборудования, применяемого при производстве черных металлов, осуществляются вредные выбросы в атмосферу, что негативно влияет как на окружающую природу, так и на здоровье людей.
По объему выбросов в воздух эта отрасль стоит на третьем месте, перед ней только энергетическая область и цветная металлургия.
Среди основных источников загрязнения вредными веществами являются дробильно-размольная техника, машины – агломерационные, а также обжига окатышей. Опасными также являются места, где происходят погрузочно-разгрузочные работы, пересыпка материалов.
В городах, где функционируют крупные комбинаты, которые занимаются переработкой, выплавкой и выпуском товаров этой отрасли, в воздухе наблюдается уровень загрязнения различными примесями с высоким классом опасности.
Особо высокую концентрацию примесей фиксируют в Магнитогорске, где этилбензол, диоксид азота имеют угрожающие показатели, а также аналогичная ситуация в Новокузнецке с диоксидом азота.
Рост производства провоцирует увеличение сбросов отходов, то есть происходит загрязнение вод. По результатам исследований, каждый девятый кубометр сточных вод, получающийся при работе российских промышленных предприятий, это отходы черной металлургии.
Хотя эта проблема стоит достаточно остро, в нынешней ситуации всевозрастающей конкуренции с производителями из СНГ маловероятны широкомасштабные работы, требующие серьезных финансовых вливаний, направленных на решение экологических проблем. Значение черной металлургии часто превышает важность экологии в стране. Предприятия, специализирующиеся на производстве стали, редко задумываются о чистоте окружающей среды. Поэтому и возникает фирма, которая специализируется на проверке работы предприятий черной.
Видео по теме: Черная металлургия
Источник