Какое свойство материала характеризует модуль сдвига
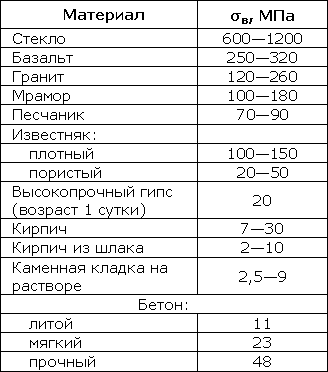
46.Основные
механические свойства. Модуль сдвига
Механические
свойства материалов,
совокупность
показателей, характеризующих сопротивление
материала воз действующей на него
нагрузке, его способность деформироваться
при этом, а также особенности его
поведения в процессе разрушения. В
соответствии с этим М. с. м. измеряют
напряжениями (обычно
в кгс/мм2 или Мн/м2), деформациями
(в %), удельной работой деформации и
разрушения (обычно
в кгс×м/см2 или Мдж/м2), скоростью
развития процесса разрушения при
статической или повторной нагрузке
(чаще всего в мм за
1 сек или
за 1000 циклов повторений нагрузки, мм/кцикл). М.
с. м. определяются при механических
испытаниях образцов различной формы.
В
общем случае материалы в конструкциях
могут подвергаться самым различным по
характеру нагрузкам (рис.
1):
работать нарастяжение,
сжатие, изгиб, кручение,
срез и т. д. или подвергаться совместному
действию нескольких видов нагрузки,
например растяжению и изгибу. Также
разнообразны условия эксплуатации
материалов и по температуре, окружающей
среде, скорости приложения нагрузки и
закону её изменения во времени. В
соответствии с этим имеется много
показателей М. с. м. и много методов
механических испытаний. Для металлов
и конструкционных пластмасс наиболее
распространены испытания на
растяжение, твёрдость,
ударный изгиб; хрупкие конструкционные
материалы (например, керамику,
металлокерамику) часто испытывают на
сжатие и статический изгиб; механические
свойства композиционных материалов
важно оценивать, кроме того, при
испытаниях на сдвиг.
Диаграмма
деформации. Приложенная
к образцу нагрузка вызывает его деформацию.
Соотношения между нагрузкой и деформацией
описываются т. н. диаграммой деформации
(рис.
2).
Вначале деформация образца (при
растяжении — приращение длины Dl )
пропорциональна возрастающей нагрузке Р,
затем в точке n эта
пропорциональность нарушается, однако
для увеличения деформации необходимо
дальнейшее повышение нагрузки Р;
при Dl >
Dlв деформация
развивается без приложения усилия
извне, при постепенно падающей нагрузке.
Вид диаграммы деформации не меняется,
если по оси ординат откладывать
напряжение
а
по оси абсцисс — относительное удлинение
(F и l —
соответственно начальная площадь
поперечного сечения и расчётная длина
образца).
Сопротивление
материалов измеряется напряжениями,
характеризующими нагрузку, приходящуюся
на единицу площади поперечного сечения
образца
в кгс/мм2. Напряжение
при
котором нарушается пропорциональный
нагрузке рост деформации, называется
пределом пропорциональности. При
нагрузкеР < Рn разгрузка
образца приводит к исчезновению
деформации, возникшей в нём под действием
приложенного усилия; такая деформация
называется упругой. Небольшое превышение
нагрузки относительно Рn может
не изменить характера деформации —
она по-прежнему сохранит упругий
характер. Наибольшая нагрузка, которую
выдерживает образец без появления
остаточной пластической деформации
при разгрузке, определяет предел
упругости материала:
У
конструкционных неметаллический
материалов (пластмассы, резины)
приложенная нагрузка может вызвать
упругую, высокоэластическую и остаточную
деформации. В отличие от упругой,
высокоэластическая деформация исчезает
не сразу после разгрузки, а с течением
времени. Высокопрочные армированные
полимеры (стеклопластики, углепластики
и др.) разрушаются при удлинении 1—3%.
На последних стадиях нагружения у
некоторых армированных полимеров
появляется высокоэластическая
деформация. Высокоэластический модуль
ниже модуля упругости, поэтому диаграмма
деформации в этом случае имеет тенденцию
отклоняться к оси абсцисс.
Упругие
свойства. В
упругой области напряжение и деформация
связаны коэффициентом пропорциональности.
При растяжении s = Еd, где Е —
т. н. модуль нормальной упругости,
численно равный тангенсу угла наклона
прямолинейного участка кривой s = s(d) к
оси деформации (рис.
2).
При испытании на растяжение цилиндрического
или плоского образца одноосному (s1>0;
(s2 =
s3 =
0) напряжённому состоянию соответствует
трёхосное деформированное состояние
(приращение длины в направлении действия
приложенных сил и уменьшение линейных
размеров в двух других взаимно
перпендикулярных направлениях): d1>0;
d2 =
d3 <
0. Соотношение между поперечной и
продольной деформацией (коэффициент
Пуассона)
в
пределах упругости для основных
конструкционных материалов колеблется
в довольно узких пределах (0,27—0,3 для
сталей, 0,3—0,33 для алюминиевых сплавов).
Коэффициент Пуассона является одной
из основных расчётных характеристик.
Зная m и Е,
можно расчётным путём определить и
модуль сдвига
и
модуль объёмной упругости
Для
определения Е,
G,
и m пользуются тензометрами.
Сопротивление
пластической деформации. При
нагрузках Р > Рв наряду
со всё возрастающей упругой деформацией
появляется заметная необратимая, не
исчезающая при разгрузке пластическая
деформация. Напряжение, при котором
остаточная относительная деформация
(при растяжении — удлинение) достигает
заданной величины (по ГОСТ — 0,2 %),
называется условным пределом текучести
и обозначается
Практически
точность современных методов испытания
такова, что sп и
sе определяют
с заданными допусками соответственно
на отклонение от закона пропорциональности
[увеличение ctg(90 — a) на 25—50 %] и на величину
остаточной деформации (0,003—0,05 %) и
говорят об условных пределах
пропорциональности и упругости. Кривая
растяжения конструкционных металлов
может иметь максимум (точка в на рис.
2)
или обрываться при достижении наибольшей
нагрузки Рв’.
Отношение
характеризует
временное сопротивление (предел
прочности) материала. При наличии
максимума на кривой растяжения в области
нагрузок, лежащих на кривой левее в,
образец деформируется равномерно по
всей расчётной длине l0,
постепенно уменьшаясь в диаметре, но
сохраняя начальную цилиндрическую или
призматическую форму. При пластической
деформации металлы упрочняются, поэтому,
несмотря на уменьшение сечения образца,
для дальнейшей деформации требуется
прикладывать всё возрастающую нагрузку.
sв,
как и условные s0,2,
sn и
sе,
характеризует сопротивление металлов
пластической деформации. На участке
диаграммы деформации правее в форма
растягиваемого образца изменяется:
наступает период сосредоточенной
деформации, выражающейся в появлении
“шейки”. Уменьшение сечения в шейке
“обгоняет” упрочнение металлов,
что и обусловливает падение внешней
нагрузки на участке Рв —
Pk.
У
многих конструкционных материалов
сопротивление пластической деформации
в упруго-пластической области при
растяжении и сжатии практически
одинаково. Для некоторых металлов и
сплавов (например, магниевые сплавы,
высокопрочные стали) характерны заметные
различия по этой характеристике при
растяжении и сжатии. Сопротивление
пластической деформации особенно часто
(при контроле качества продукции,
стандартности режимов термической
обработки и в др. случаях) оценивается
по результатам испытаний на твёрдость
путём вдавливания твёрдого наконечника
в форме шарика (твёрдость по Бринеллю
или Роквеллу), конуса (твёрдость по
Роквеллу) или пирамиды (твёрдость по
Виккерсу). Испытания на твёрдость не
требуют нарушения целостности детали
и потому являются самым массовым
средством контроля механических
свойств. Твёрдость по Бринеллю (HB) при
вдавливании шарика диаметром D под
нагрузкой Р характеризует
среднее сжимающее напряжение, условно
вычисляемое на единицу поверхности
шарового отпечатка диаметром d:
Характеристики
пластичности. Пластичность
при растяжении конструкционных
материалов оценивается удлинением
или
сужением
при
сжатии — укорочением
(где h и hk —
начальная и конечная высота образца),
при кручении — предельным углом
закручивания рабочей части образца
Q,рад или
относительным сдвигом g = Qr (где r —
радиус образца). Конечная ордината
диаграммы деформации (точка k на рис.
2)
характеризует сопротивление разрушению
металла Sk,
которое определяется
(Fk —
фактическая площадь в месте разрыва).
Модуль
сдвига-величина,
характеризующая деформацию сдвига.
Модуль
сдвига равен отношению касательного
напряжения к величине угла сдвига.
В начальной
части диаграмма сдвига (на рисунке)
линейная, т.е. угол сдвига пропорционален
касательному напряжению .
Закон пропорциональности, называемый
законом Гука при сдвиге, может быть
записан:
где
коэффициент пропорциональности G называется
модулем сдвига сдвига или модулем
упругости 2-го рода. Он характеризует
сопротивление материала упругим
деформациям и является его упругой
постоянной.
Источник
Диаграммы напряжений
На сегодняшний день существует несколько методик испытания образцов материалов. При этом одним из самых простых и показательных являются испытания на растяжение (на разрыв), позволяющие определить предел пропорциональности, предел текучести, модуль упругости и другие важные характеристики материала. Так как важнейшей характеристикой напряженного состояния материала является деформация, то определение значения деформации при известных размерах образца и действующих на образец нагрузок позволяет установить вышеуказанные характеристики материала.
Тут может возникнуть вопрос: почему нельзя просто определить сопротивление материала? Дело в том, что абсолютно упругие материалы, разрушающиеся только после преодоления некоторого предела – сопротивления, существуют только в теории. В реальности большинство материалов обладают как упругими так и пластическими свойствами, что это за свойства, рассмотрим ниже на примере металлов.
Испытания металлов на растяжение проводятся согласно ГОСТ 1497-84. Для этого используются стандартные образцы. Методика испытаний выглядит приблизительно так: к образцу прикладывается статическая нагрузка, определяется абсолютное удлинение образца Δl, затем нагрузка увеличивается на некоторое шаговое значение и снова определяется абсолютное удлинение образца и так далее. На основании полученных данных строится график зависимости удлинений от нагрузки. Этот график называется диаграммой напряжений.
Рисунок 318.1. Диаграмма напряжений для стального образца.
На данной диаграмме мы видим 5 характерных точек:
1. Предел пропорциональности Рп (точка А)
Нормальные напряжения в поперечном сечении образца при достижении предела пропорциональности будут равны:
σп = Рп/Fo (318.2.1)
Предел пропорциональности ограничивает участок упругих деформаций на диаграмме. На этом участке деформации прямо пропорциональны напряжениям, что выражается законом Гука:
Рп = kΔl (318.2.2)
где k – коэффициент жесткости:
k = EF/l (318.2.3)
где l – длина образца, F – площадь сечения, Е – модуль Юнга.
Модули упругости
Главными характеристиками упругих свойств материалов являются модуль Юнга Е (модуль упругости первого рода, модуль упругости при растяжении), модуль упругости второго рода G (модуль упругости при сдвиге) и коэффициент Пуассона μ (коэффициент поперечной деформации).
Модуль Юнга Е показывает отношение нормальных напряжений к относительным деформациям в пределах пропорциональности
Модуль Юнга также определяется опытным путем при испытании стандартных образцов на растяжение. Так как нормальные напряжения в материале равны силе, деленной на начальную площадь сечения:
σ = Р/Fо (318.3.1), (317.2)
а относительное удлинение ε – отношению абсолютной деформации к начальной длине
εпр = Δl/lo (318.3.2)
то модуль Юнга согласно закону Гука можно выразить так
Е = σ/εпр = Plo/FoΔl = tgα (318.3.3)
Рисунок 318.2. Диаграммы напряжений некоторых сплавов металлов
Коэффициент Пуассона μ показывает отношение поперечных деформаций к продольным
Под воздействием нагрузок не только увеличивается длина образца, но и уменьшается площадь рассматриваемого поперечного сечения (если предположить, что объем материала в области упругих деформаций остается постоянным, то значит увеличение длины образца приводит к уменьшению площади сечения). Для образца, имеющего круглое сечение, изменение площади сечения можно выразить так:
εпоп = Δd/do (318.3.4)
Тогда коэффициент Пуассона можно выразить следующим уравнением:
μ = εпоп/εпр (318.3.5)
Модуль сдвига G показывает отношение касательных напряжений т к углу сдвига
Модуль сдвига G может быть определен опытным путем при испытании образцов на кручение.
При угловых деформациях рассматриваемое сечение перемещается не линейно, а под некоторым углом – углом сдвига γ к начальному сечению. Так как касательные напряжения равны силе, деленной на площадь в плоскости которой действует сила:
т = Р/F (318.3.6)
а тангенс угла наклона можно выразить отношением абсолютной деформации Δl к расстоянию h от места фиксации абсолютной деформации до точки, относительно которой осуществлялся поворот:
tgγ = Δl/h (318.3.7)
то при малых значениях угла сдвига модуль сдвига можно выразить следующим уравнением:
G = т/γ = Ph/FΔl (318.3.8)
Модуль Юнга, модуль сдвига и коэффициент Пуассона связаны между собой следующим отношением:
Е = 2(1 + μ)G (318.3.9)
Значения постоянных Е, G и µ приводятся в таблице 318.1
Таблица 318.1. Ориентировочные значения упругих характеристик некоторых материалов
Примечание: Модули упругости являются постоянными величинами, однако технологии изготовления различных строительных материалов меняются и более точные значения модулей упругости следует уточнять по действующим в настоящий момент нормативным документам. Модули упругости бетона зависят от класса бетона и потому здесь не приводятся.
Упругие характеристики определяются для различных материалов в пределах упругих деформаций, ограниченных на диаграмме напряжений точкой А. Между тем на диаграмме напряжений можно выделить еще несколько точек:
2. Предел упругости Ру
Нормальные напряжения в поперечном сечении образца при достижении предела упругости будут равны:
σу = Ру/Fo (318.2.4)
Предел упругости ограничивает участок на котором появляющиеся пластические деформации находятся в пределах некоторой малой величины, нормированной техническими условиями (например 0,001%; 0,01% и т. д.). Иногда предел упругости обозначается соответственно допуску σ0.001, σ0.01 и т.д.
3. Предел текучести Рт
σт = Рт/Fo (318.2.5)
Ограничивает участок диаграммы на котором деформация увеличивается без значительного увеличения нагрузки (состояние текучести). При этом по всему объему образца происходит частичный разрыв внутренних связей, что и проводит к значительным пластическим деформациям. Материал образца полностью не разрушается, но его начальные геометрические размеры претерпевают необратимые изменения. На отшлифованной поверхности образцов наблюдаются фигуры текучести – линии сдвигов (открытые профессором В. Д. Черновым). Для различных металлов углы наклона этих линий различны, но находятся в пределах 40-50о. При этом часть накопленной потенциальной энергии необратимо расходуется на частичный разрыв внутренних связей. При испытании на растяжение принято различать верхний и нижний пределы текучести – соответственно наибольшее и наименьшее из напряжений, при которых возрастает пластическая (остаточная) деформация при почти постоянной величине действующей нагрузки.
На диаграммах напряжений отмечен нижний предел текучести. Именно этот предел для большинства материалов принимается за нормативное сопротивление материала.
Некоторые материалы не имеют выраженной площадки текучести. Для них за условный предел текучести σ0.2 принимается напряжение, при котором остаточное удлинение образца достигает значения ε ≈0,2%.
4. Предел прочности Рмакс (временное сопротивление)
Нормальные напряжения в поперечном сечении образца при достижении предела прочности будут равны:
σв = Рмакс/Fo (318.2.6)
После преодоления верхнего предела текучести (на диаграммах напряжения не показан) материал снова начинает сопротивляться нагрузкам. При максимальном усилии Рмакс начинается полное разрушение внутренних связей материала. При этом пластические деформации концентрируются в одном месте, образуя в образце так называемую шейку.
Напряжение при максимальной нагрузке называется пределом прочности или временным сопротивлением материала.
В таблицах 318.2 – 318.5 приведены ориентировочные величины пределов прочности для некоторых материалов:
Таблица 318.2 Ориентировочные пределы прочности на сжатие (временные сопротивления) некоторых строительных материалов.
Примечание: Для металлов и сплавов значение пределов прочности следует определять согласно нормативных документов. Значение временных сопротивлений для некоторых марок стали можно посмотреть здесь.
Таблица 318.3. Ориентировочные пределы прочности (временные сопротивления) для некоторых пластмасс
Таблица 318.4. Ориентировочные пределы прочности для некоторых волокон
Таблица 318.5. Ориентировочные пределы прочности для некоторых древесных пород
5. Разрушение материала Рр
Если посмотреть на диаграмму напряжений, то создается впечатление, что разрушение материала наступает при уменьшении нагрузки. Такое впечатление создается потому, что в результате образования “шейки” значительно изменяется площадь сечения образца в районе “шейки”. Если построить диаграмму напряжений для образца из малоуглеродистой стали в зависимости от изменяющейся площади сечения, то будет видно, что напряжения в рассматриваемом сечении увеличиваются до некоторого предела:
Рисунок 318.3. Диаграмма напряжений: 2 – по отношению к начальной площади поперечного сечения, 1 – по отношению к изменяющейся площади сечения в районе шейки.
Тем не менее более правильным является рассмотрение прочностных характеристик материала по отношению к площади первоначального сечения, так как расчетами на прочность изменение первоначальной геометрической формы редко предусматривается.
Одной из механических характеристик металлов является относительное изменение ψ площади поперечного сечения в районе шейки, выражаемое в процентах:
ψ = 100(Fo – F)/Fo (318.2.7)
где Fo – начальная площадь поперечного сечения образца (площадь поперечного сечения до деформации), F – площадь поперечного сечения в районе “шейки”. Чем больше значение ψ, тем более ярко выражены пластические свойства материала. Чем меньше значение ψ, тем больше хрупкость материала.
Если сложить разорванные части образца и измерить его удлинение, то выяснится, что оно меньше удлинения на диаграмме (на длину отрезка NL), так как после разрыва упругие деформации исчезают и остаются только пластические. Величина пластической деформации (удлинения) также является важной характеристикой механических свойств материала.
За пределами упругости, вплоть до разрушения, полная деформация состоит из упругой и пластической составляющих. Если довести материал до напряжений, превышающих предел текучести (на рис. 318.1 некоторая точка между пределом текучести и пределом прочности), и затем разгрузить его, то в образце останутся пластические деформации, но при повторном загружении через некоторое время предел упругости станет выше, так как в данном случае изменение геометрической формы образца в результате пластических деформаций становится как бы результатом действия внутренних связей, а изменившаяся геометрическая форма, становится начальной. Этот процесс загрузки и разгрузки материала можно повторять несколько раз, при этом прочностные свойства материала будут увеличиваться:
Рисунок 318.4. Диаграмма напряжений при наклепе (наклонные прямые соответствуют разгрузкам и повторным загружениям)
Такое изменение прочностных свойств материала, получаемое путем повторяющихся статических загружений, называется наклепом. Тем не менее при повышении прочности металла путем наклепа уменьшаются его пластические свойства, а хрупкость увеличивается, поэтому полезным как правило считается относительно небольшой наклеп.
Работа деформации
Прочность материала тем выше, чем больше внутренние силы взаимодействия частиц материала. Поэтому величина сопротивления удлинению, отнесенная к единице объема материала, может служить характеристикой его прочности. В этом случае предел прочности не является исчерпывающей характеристикой прочностных свойств данного материала, так как он характеризует только поперечные сечения. При разрыве разрушаются взаимосвязи по всей площади сечения, а при сдвигах, которые происходят при всякой пластической деформации, разрушаются только местные взаимосвязи. На разрушение этих связей затрачивается определенная работа внутренних сил взаимодействия, которая равна работе внешних сил, затрачиваемой на перемещения:
А = РΔl/2 (318.4.1)
где 1/2 – результат статического действия нагрузки, возрастающей от 0 до Р в момент ее приложения (среднее значение (0 + Р)/2)
При упругой деформации работа сил определяется площадью треугольника ОАВ (см. рис. 318.1). Полная работа, затраченная на деформацию образца и его разрушение:
А = ηРмаксΔlмакс (318.4.2)
где η – коэффициент полноты диаграммы, равный отношению площади всей диаграммы, ограниченной кривой АМ и прямыми ОА, MN и ON, к площади прямоугольника со сторонами 0Рмакс (по оси Р) и Δlмакс (пунктир на рис. 318.1). При этом надо вычесть работу, определяемую площадью треугольника MNL (относящуюся к упругим деформациям).
Работа, затрачиваемая на пластические деформации и разрушение образца, является одной из важных характеристик материала, определяющих степень его хрупкости.
Деформация сжатия
Деформации сжатия подобны деформациям растяжения: сначала происходят упругие деформации, к которым за пределом упругости добавляются пластические. Характер деформации и разрушения при сжатии показан на рис. 318.5:
Рисунок 318.5
а – для пластических материалов; б – для хрупких материалов ; в – для дерева вдоль волокон, г – для дерева поперек волокон.
Испытания на сжатие менее удобны для определения механических свойств пластических материалов из-за трудности фиксирования момента разрушения. Методы механических испытаний металлов регламентируются ГОСТ 25.503-97. При испытании на сжатие формы образца и его размеры могут быть различными. Ориентировочные значения пределов прочности для различных материалов приведены в таблицах 318.2 – 318.5.
Если материал находится под нагрузкой при постоянном напряжении, то к практически мгновенной упругой деформации постепенно прибавляется добавочная упругая деформация. При полном снятии нагрузки упругая деформация уменьшается пропорционально уменьшающимся напряжениям, а добавочная упругая деформация исчезает медленнее.
Образовавшаяся добавочная упругая деформация при постоянном напряжении, которая исчезает не сразу после разгрузки, называется упругим последействием.
Влияние температуры на изменение механических свойств материалов
Твердое состояние – не единственное агрегатное состояние вещества. Твердые тела существуют только в определенном интервале температур и давлений. Повышение температуры приводит к фазовому переходу из твердого состояния в жидкое, а сам процесс перехода называется плавлением. Температуры плавления, как и другие физические характеристики материалов, зависят от множества факторов и также определяются опытным путем.
Таблица 318.6. Температуры плавления некоторых веществ
Примечание: В таблице приведены температуры плавления при атмосферном давлении (кроме гелия).
Упругие и прочностные характеристики материалов, приведенные в таблицах 318.1-318.5, определяются как правило при температуре +20оС. ГОСТом 25.503-97 допускается проводить испытания металлических образцов в диапазоне температур от +10 до +35оС.
При изменении температуры изменяется потенциальная энергия тела, а значит, изменяется и значение внутренних сил взаимодействия. Поэтому механические свойства материалов зависят не только от абсолютной величины температуры, но и от продолжительности ее действия. Для большинства материалов при нагреве прочностные характеристики (σп, σт и σв) уменьшаются, при этом пластичность материала увеличивается. При снижении температуры прочностные характеристики увеличиваются, но при этом повышается хрупкость. При нагреве уменьшается модуль Юнга Е, а коэффициент Пуассона увеличивается. При снижении температуры происходит обратный процесс.
Рисунок 318.6. Влияние температуры на механические характеристики углеродистой стали.
При нагревании цветных металлов и сплавов из них прочность их сразу падает и при температуре, близкой к 600° С, практически теряется. Исключение составляет алюмотермический хром, предел прочности которого с увеличением температуры увеличивается и при температуре равной 1100° С достигает максимума σв1100 = 2σв20.
Характеристики пластичности меди, медных сплавов и магния с ростом температуры уменьшаются, а алюминия – увеличиваются. При нагреве пластмасс и резины их предел прочности резко снижается, а при охлаждении эти материалы становятся очень хрупкими.
Влияние радиоактивного облучения на изменение механических свойств
Радиоактивное облучение по-разному влияет на различные материалы. Облучение материалов неорганического происхождения по своему влиянию на механические характеристики и характеристики пластичности подобно понижению температуры: с увеличением дозы радиоактивного облучения увеличивается предел прочности и особенно предел текучести, а характеристики пластичности снижаются.
Облучение пластмасс также приводит к увеличению хрупкости, причем на предел прочности этих материалов облучение оказывает различное влияние: на некоторых пластмассах оно почти не сказывается (полиэтилен), у других вызывает значительное понижение предела прочности (катамен), а в третьих – повышение предела прочности (селектрон).
Источник