Какое свойство характеризует сопротивление материала хрупкому разрушению
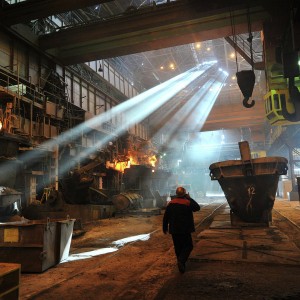
Требования к свойствам конструкционных материалов
Успех в создании конструкций – возможность их индустриального изготовления, надежность и долговечность в эксплуатации, технико-экономическая эффективность во многом зависит от правильного выбора материала. В последние десятилетия благодаря совместным усилиям металлургов, металловедов и специалистов-сварщиков улучшены существующие и разработаны новые эффективные марки стали и виды проката, значительно расширившие возможности проектирования. При этом были сформулированы определенные требования к стальному прокату (основному конструкционному материалу) для металлоконструкций.
Накопленный опыт проектирования и длительной эксплуатации эффективных по уровню воспринимаемых нагрузок и архитектурному оформлению конструкций позволяет выделить пять основных служебных свойств, которыми в той или иной мере должны обладать конструкционные материалы:
· прочность,
· свариваемость,
· сопротивление хрупкому разрушению,
· сопротивление вязкому разрушению,
· технико-экономическая эффективность.
Прочность
Эффективность повышения прочности стали проявляется в снижении массы металлической конструкции. Если за основу (нижний уровень прочности) принять наименее прочную углеродистую сталь обыкновенного качества с пределом текучести σт=230 МПа и временным сопротивлением σв=380 МПа, то анализируя опыт создания металлоконструкций с пределом текучести до 1000 МПа можно сделать вывод, что особенно интенсивное снижение массы конструкции наблюдается при относительном повышении прочности – до двух, – трехкратного уровня. При этом максимальное снижение массы достигается в сооружениях, в которых значительная часть несущей способности конструкции расходуется на поддержание собственного веса, например, в элементах тяжелого пролетного строения; хорошие результаты дает использование высокопрочной стали в элементах, испытывающих растяжение, несколько худшее в конструкциях, включающих сжато-изогнутые элементы. Не удается получить снижение массы при повышении прочности стали в элементах с малой жесткостью. Не достигается оно и в элементах сварных конструкций, испытывающих интенсивные переменные силовые воздействия с большим числом циклов нагружения и малой асимметрией циклов.
Из этого следует, что наиболее эффективными в части снижения массы (и стоимости) могут оказаться комбинированные конструкции, включающие элементы из сталей разных уровней прочности (бистальные), которые выбираются исходя из условий нагружения и конструктивных особенностей элементов.
На основании приведенных представлений для проката строительных сталей были выбраны семь основных унифицированных уровней прочности, которым соответствует:
σт – предел текучести не менее: 225, 285, 325, 390, 440, 590 и 735 МПа;
σв – временное сопротивление разрыву не менее: 375, 430, 450, 510, 590, 685 и 830 МПа.
Свариваемость
Традиционный способ повышения прочности стали состоит в увеличении содержания углерода и легирующих элементов. Установлено, однако, что при этом возрастает опасность появления в околошовной зоне закалочных микроструктур, хрупких холодных трещин и трещин задержанного хрупкого разрушения. Действие углерода в этом отношении особенно отрицательно. Влияние легирующих элементов и примеси выражают количественно сравнением с влиянием углерода. По формуле Международного института сварки:
Сэ = С + Mn/6 + (Cr + Mo + V)/5 + (Cu + Ni)/15.
По свариваемости стали делят на четыре группы:
хорошая: Сэ <= 0,25
Углеродистые стали: Ст1, Ст2, Ст3, Ст4, 08,10, 15, 20, 25;
Конструкционные низколегир.:15Г, 20Г, 15Х, 15ХА, 20Х, 15ХМ, 20ХГСА, 10ХСНД, 10ХГСНД, 15ХСНД
Эти стали при обычных способах сварки не дают трещин. Сварка таких сталей выполняется без предварительного и сопутствующего подогрева, без последующей термообработки.
удовлетворительная: Сэ = 0,25 – 0,35
Углеродистые стали: Ст5, 30, 35;
Конструкционные низколегир.: 12ХН2, 12ХН3А, 20ХН3А, 20ХН, 20ХГСА, 30Х, 30ХМ, 25ХГСА;
Такие стали допускают сварку без образования трещин только в нормальных производственных условиях, когда температура окружающей среды выше 0º С и отсутствует ветер или сквозняки.
ограниченная: Сэ = 0,35 – 0,45
Углеродистые стали: Ст6, 40, 45, 50;
Конструкционные низколегир. : 35Г, 40Г, 45Г, 40Г2, 35Х, 40Х, 45Х, 40ХМФА, 40ХН, 30ХГС, 30ХГСА, 35ХМ, 20Х2Н4А, 18Х2Н4МА, 4ХС:
Эти стали в обычных условиях сварки склонны к образованию трещин. Как правило, сварка таких сталей производится по специальной технологии, регламентирующей режимы предварительной термообработки, подогрева и тепловой обработки после сварки.
плохая: Сэ > 0,45
Углеродистые стали: 65, 70, 80, 85, У7, У8, У9, У10, У11, У12;
Конструкционные низколегир.: 50Г, 50Г2, 50Х, 50ХН, 45ХН3МФА, ХГС, 6ХС, 7Х3.
Эти стали склонны к образованию трещин. Сварка их выполняется с обязательной предварительной термообработкой подогревом в процессе сварки и с последующей термообработкой.
Кроме эквивалента углерода, образование закалочных микроструктур и связанных с ними трещин зависит от скорости охлаждения металла шва и околошовной зоны, на которую влияют тепловые параметры сварки (тепловложение, начальная температура) и конструктивные особенности соединения (форма, толщина). При сварке стали с одним и тем же углеродным эквивалентом с возрастанием скорости охлаждения вероятность образования закалочных микроструктур увеличивается, что находит отражение в монотонном росте максимальной твердости в околошовной зоне. Поэтому ограничение максимальной твердости некоторой критической величиной может служить хорошим критерием для выбора стали и условий ее применения. Так, в японских стандартах на сталь для сварных конструкций, помимо ограничений по эквиваленту углерода с 70-х годов введено ограничение по максимальной твердости в околошовной зоне: не свыше 350 HV.
Предложено много способов экспериментальной оценки свариваемости, включая механизированные способы испытаний в условиях имитированных термодеформационных циклов сварки. Однако их применение необходимо только при разработке новых сталей или при использовании существующей стали в той области, в которой она ранее не применялась. Для проката традиционных свариваемых сталей при их обычном использовании достаточной гарантией свариваемости является соответствие химического состава и механических свойств нормам технических условий и стандартов.
Склонность к образованию горячих трещин для класса хромоникелевых сталей может быть оценена по хромоникелевому эквиваленту (Crэкв/Ni экв):
Cr экв =Сr + 1,5 Si + Mo +0,8 V + 0,5 Nb + W + 3,5 Al + 4 Ti;
Ni экв = Ni + 0,5 Mn + 0,5 Cu + 30 C +30 N;
К = (Cr экв)/(Ni экв) =1,6 – 1,3 сваривается без ограничений;
К = (Cr экв)/(Ni экв) = 1,3 – 1,0 ограниченно свариваемая;
К = (Cr экв)/(Ni экв) <1 трудно свариваемая.
Сопротивление хрупкому разрушению
Существенным фактором, ограничивающим выбор стали для сварных конструкций и, в частности, препятствующим дальнейшему повышению ее прочности обычным легированием (например, кремнием), является требование хладостойкости. Для строительной стали с ним ассоциируется сопротивление хрупкому разрушению микросколом. При этом виде разрушения зерна металла раскалываются по определенным кристаллографическим плоскостям с образованием в изломе характерных «кристаллических» фасеток и «ручьевого узора».
Разрушения этого вида особенно опасны, так как происходят внезапно, распространяясь с высокой скоростью без заметной макропластической деформации, часто даже при весьма низких напряжениях от рабочей нагрузки. Сварные конструкции подвержены хрупкому разрушению микросколом более других. Этому способствует концентрация напряжений, структурная и механическая неоднородность, неразъемность и высокий уровень сварочных напряжений.
Хладостойкость элемента конструкции определяется температурой хрупкости, при которой возможен переход от вязкого разрушения к хрупкому разрушению микросколом. На изменение этой температуры влияют как физические свойства стали (предел текучести, микроструктура), так и «внешние» условия нагружения (напряжение, жесткость напряженно-деформированного состояния, величина и скорость деформации).
Велика роль особенностей внешнего нагружения. Так, переход от условий растяжения гладкого образца к растяжению элемента с острым концентратором напряжений повышает критическую температуру перехода в хрупкое состояние Tk для строительной стали на 170-200 ºС.
Также любой из факторов, упрочняющих сталь и вызывающих повышение предела текучести (наклеп, старение, радиационное упрочнение и др.), повышает Tk, т.е. охрупчивает материал, а измельчение зерна микроструктуры, напротив, снижает Tk, т.е. повышает хладостойкость. Следовательно, непременным условием сохранения хладостойкости при повышении прочности является измельчение микроструктуры.
На основании исследований особенностей хрупкого разрушения микросколом предложено много способов экспериментальной оценки хладостойкости сварных соединений. Почти все они предусматривают многократные (сериальные) испытания одинаковых (для данного способа) по размерам и форме образцов, но при разных температурах. Показателем качества металла служит температура, при которой контролируемый признак (поглощенная при разрушении образца работа, доля волокна в изломе образца, сужение под надрезом в разрушенном образце, разрушающее напряжение и т.п.) по мере проявления хрупкости с понижением температуры достигает некоторой нормируемой величины.
Приведем некоторые основные методы, получившие наибольшее распространение:
·испытание на динамический изгиб стандартных (призматических) образцов по ГОСТ 6996-66 на ударную вязкость с полукруглым (r=1 мм) или треугольным (r=0,25 мм) надрезами, а также с концентратором в виде трещины усталости;
·испытание на растяжение или изгиб крупных плоских (листовых) образцов натурной толщины с глубокими надрезами или трещинами усталости на кромках;
·определение температуры остановки инициированной трещины на крупных листовых образцах натурной толщины по Робертсону.
Наряду с концепцией переходной (критической) температуры, широко используемой в механике хрупкого разрушения, разработаны и получили значительное развитие аналитические методы, основанные на рассмотрении поля упругих напряжений в вершине трещины. При этом для оценки сопротивления сталей хрупкому разрушению применяются энергетические, силовые и деформационные критерии механики разрушения. С использованием указанных критериев представляется возможным установить связь между разрушающим (или допустимым) напряжением и размером трещины, которая гипотетически может присутствовать в конструкции.
Основным критерием механики разрушения служит коэффициент интенсивности напряжений К, предложенный Ирвином (США), как параметр, определяющий поле упругих напряжений перед фронтом трещины, и является функцией приложенного напряжения и формы трещины. При переходе в хрупкое состояние трещина развивается при средних напряжениях в нетто сечении ниже предела упругости. В упругой области напряжений для трещины в бесконечно широкой пластине, нагруженной нормальными напряжениями, направленными перпендикулярно трещине, выражение для коэффициента интенсивности напряжений К имеет вид:
К = σ √ (3,14∙L),
где σ – номинальное напряжение; L – половина длины центральной сквозной трещины.
При других формах тел и расположении трещин, а также при переходе к телам ограниченных размеров и изменении характера распределения номинальных напряжений в формулу вводится соответствующая поправочная функция:
К = f ∙ σ √ (3,14∙L).
При достижении напряжениями критических значений σкр (момент начала настабильного разрушения) коэффициент интенсивности напряжений также достигает критического для данного материала значения:
Кс = σкр √ (3,14∙L).
При наиболее жестком напряженном состоянии, известном как «плоская деформация», критическое значение коэффициента интенсивности напряжений обозначается К1с .
К1с являются, таким образом, характеристиками материала, которые определяются его способностью сопротивляться распространению трещины. Ниже представлены значения К1с МПа√м для некоторых марок сталей:
Ст3сп………………… 60 – 80 МПа√м
09Г2С…………………65 – 90
10Г2С1………………..75 – 90
10ХСНД…………..…100 – 120
16Г2АФ…………… 110 – 130
Зная значение К1с для выбранной марки стали, проектировщик может рассчитать значение напряжения, вызывающее нестабильное разрушение при наличии трещиноподобного дефекта определенного размера и формы при наиболее жестком напряженном состоянии.
Источник
Хрупкое разрушение элементов стальных конструкций обусловлено действием напряжений и рядом факторов охрупчивания, стесняющих развитие пластической деформации металла.
Все многообразие таких факторов на практике можно свести к основным пяти: динамический характер нагружения, отрицательная климатическая температура, увеличение сечения элементов конструкций, наличие концентраторов напряжений, а также неблагоприятная микроструктура стали (повышенные разнозернистость. структурная и химическая неоднородность, загрязненность неметаллическими включениями и др.). В случаях одновременного воздействия четырех и более из перечисленных факторов хрупкое разрушение конструкций становится весьма вероятным, что требует проведения соответствующих расчетов.
Мелкозернистая и однородная микроструктура стали обеспечивает ей повышенную вязкость и частично может компенсировать отрицательное воздействие основных охрупчивающих факторов. Поэтому, чем больше факторов детерминированно действует при эксплуатации стальных конструкций, тем более высокие требования следует предъявлять к уровню вязкости стали.
Общие закономерности изменения основных механических характеристик конструкционных строительных сталей и условия перехода разрушения от вязкого к хрупкому при понижении температуры обычно выделяют четыре области I…IV.
Области I и II соответствуют разрушению элементов конструкций после общего пластического течения в их сечении-нетто и деформационного упрочнения, т. е. при номинальных растягивающих напряжениях, намного превышающих предел текучести стали. При этом излом стали характеризуется наличием значительного количества волокнистой составляющей В, уменьшающегося по мере снижения температуры от 100…50% в области I и практически до нуля — левая граница области II. Другими словами, возникновению и распространению трещины сколом в элементах конструкций предшествует формирование обширной зоны пластической деформации, что фактически является энергетическим барьером, предотвращающим их хрупкое разрушение. Поскольку низкоуглеродистые и низколегированные стали характеризуются достаточно высокими показателями пластичности в температурном интервале области II, то хрупкое разрушение элементов конструкций из этих сталей в указанном интервале температур может произойти лишь при одновременном действии 4-х и более основных охрупчиваюших факторов, стесняющих развитие пластической деформации. Поэтому требования к материалу сварных конструкций, эксплуатирующихся при температурах ниже —40° С или в условиях динамического нагружения, или изготовленных из проката сечением более 20 мм обычно связывают с первой критической температурой хрупкости (T1кр).
При температурах области III разрушение элементов конструкций происходит сколом, т. е. В ≈ 0%, при минимальной пластической деформации и напряжениях σPH, близких к σТ. Такой вид разрушений следует классифицировать как квазихрупкое разрушение. Граничная температура между областями II и III называется температурой нулевой пластичности Тн.п, ниже которой в изломе практически не наблюдается волокнистой составляющей. Со стороны отрицательных температур область III ограничивается температурой, называемой в технической литературе второй критической температурой хрупкости Т2кр и соответствующей условиям разрушения элементов конструкций сколом при напряжениях сгн, равных или несколько меньших σТ.
Наиболее часто критические температуры хрупкости и условные пороги хладноломкости устанавливают по энергетическому критерию: работе разрушения А или ударной вязкости (KCU, KCV и др.), или по изменению их значения относительно максимальных значений этих параметров. Этот критериальный параметр в сильной степени зависит от размеров образца, типа надреза, прочности стали и ее структуры, особенно от фазового состава и размера ферритного зерна. Высокая чувствительность критических температур хрупкости к структурным параметрам, определяемым по энергетическим критериям при испытании стандартных образцов на ударный изгиб, обусловило их широкое использование при проведении научных исследований, а также в практике приемо-сдаточных испытаний.
Оценку сопротивления хрупкому разрушению элементов стальных конструкций часто производят при испытаниях крупных образцов толщиной, равной толщине проката, предложенных Кинцелем и Робертсоном. При этом за температуру Тн.п при испытаниях образцов Кинцеля принимается температура, при которой относительное сужение у дна F-образного надреза после разрушения не превышает 1 %. Температура, при которой номинальное разрушающее напряжение становится меньше предела текучести, принимается за критическую температуру Т2кр. При этих испытаниях за Т1кр принимают температуру, при которой останавливается быстро распространяющаяся трещина в случае нагружения образца Робертсона с заданным,градиентным температурным полем.
Сопротивление стального проката хрупкому разрушению как в исследовательских работах, так и в нормативно-справочной документации обычно оценивают по результатам испытаний на ударный изгиб небольших надрезанных образцов при отрицательных температурах. Чаще всего используются образцы типов I и II по ГОСТ 9454-78 с U-образным, типа Менаже, и острым F-образным, типа Шарпи, надрезами соответственно, вырезанные вдоль или поперек направления прокатки. При этом определяют энергетические характеристики разрушения стали: полная работа разрушения образца А, Дж и ударная вязкость KCU, KCV, Дж/см2. т.е. отношение полной работы разрушения надрезанного образца к его сечению-нетто. За критическую температуру перехода от вязкого к хрупкому разрушению (или хладостойкость) принимается температура, при которой А или KCU, KCV равны или превышают их заданные значения.
В последние годы для оценки сопротивления хрупкому разрушению сталей для строительных конструкций все большее применение, особенно в исследовательских работах, находят испытания образцов с предварительно нанесенной усталостной трещиной с определением характеристик вязкости разрушения: критического коэффициента интенсивности напряжений К1с, раскрытия в вершине трещины σc, критического значения J-интеграла Jc или J1c, критического коэффициента плотности деформаций Sc. Подобные испытания имеют ряд важных преимуществ по сравнению с вышеописанными испытаниями на статический и ударный изгиб надрезанных образцов. Во-первых, они позволяют количественно оценить одно из основных эксплуатационных свойств элементов строительных конструкций — сопротивление хрупкому разрушению при наличии в них острых надрезов типа трещины, часто присутствующих в сварных конструкциях, т. е. их трешиностойкость, а также длину опасной трещины. Во-вторых, характеристики линейной механики разрушения являются более структурно-чувствительными, что весьма важно для оптимизации параметров упрочняющих обработок проката из этих сталей.
В пластичных сталях при росте номинального напряжения напряжение у вершины трещины всегда превышает предел текучести (во всяком случае раньше, чем коэффициент интенсивности напряжения достигает критического значения). При этом в вершине трещины в зоне размером rт возникают пластические деформации.
Для строительных сталей предпочтительнее использовать энергетические характеристики трещиностойкости. Сущность метода J-интеграла Для оценки разрушения материала в упругопластической области состоит в привлечении представлений об интенсивности высвобождения энергии Деформации при распространении трещины. Значение J-интеграла зависит от изменения потенциальной энергии, связанной с увеличением размера трещины. При упругом (линейном и нелинейном) поведении материала из-за обратимости деформации характеризует энергию, необходимую для распространения трещины.
Источник