Какими особенностями типа связи свойства металлов обусловлены
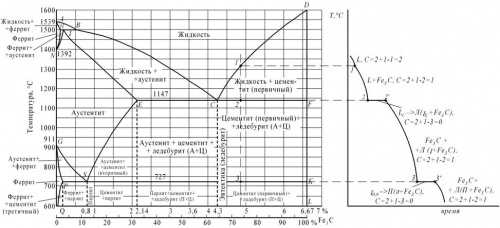
Какими свойствами обладают металлы и какими особенностями типа связи эти свойства обусловлены?
Металлы в твердом и отчасти в жидком состоянии обладают рядом характерных свойств:
– высокими теплопроводность и электрической проводимостью;
– положительным температурным коэффициентом электрического сопротивления; с повышением температуры электрическое сопротивление чистых металлов возрастает; большое число металлов обладают сверхпроводимостью (у этих металлов при температуре, близкой к абсолютному нулю, электрическое сопротивление падает скачкообразно, практически до нуля);
– термоэлектронной эмиссией, т. е. способностью испускать электроны при нагреве;
– хорошей отражательной способностью: металлы непрозрачны и обладают металлическим блеском;
– повышенной способностью к пластической деформации.
Данные свойства обусловлены особенностями строения металлов. Согласно теории металлического состояния, металл представляет собой вещество, состоящее из положительных ядер, вокруг которых по орбиталям вращаются электроны. На последнем уровне число электронов невелико и они слабо связаны с ядром. Эти электроны имеют возможность перемещаться по всему объему металла, т.е. принадлежать целой совокупности атомов.
Таким образом, пластичность, теплопроводность и электропроводность обеспечиваются наличием «электронного газа».
Какая температура разделяет районы холодной и горячей пластической деформации и почему? Рассмотрите на примере меди.
В зависимости от отношения температуры деформации к температуре рекристаллизации различают холодную и горячую деформацию.
Холодной деформацией называют такую, которую проводят при температуре ниже температуры рекристаллизации. Поэтому холодная деформация сопровождается упрочнением (наклепом) металла.
Деформацию называют горячей, если ее проводят при температуре выше температуры рекристаллизации для получения для получения полностью рекристаллизованной структуры.
При этих температурах деформация также вызывает упрочнение («горячий наклеп»), которое полностью или частично снимается рекристаллизацией, протекающей при температурах обработки и при последующем охлаждении.
При горячей обработке давлением (прокатке, прессовании, ковке, штамповке и т. д.) упрочнение в результате наклепа (повышение плотности дислокаций) непосредственно в процессе деформации непрерывно чередуется с процессом разупрочнения (уменьшением плотности дислокаций) при динамической полигонизации и рекристаллизации во время деформации и охлаждения. В этом основное отличие динамической полигонизации и рекристаллизации от статической.
Горячую деформацию в зависимости от состава сплава и скорости деформации обычно проводят при температурах (0,7 – 0,75 Тпл).
Полигонизация – процесс деления зерен на части: фрагменты, полигоны в результате скольжения и переползания дислокаций. Рекристаллизация – процесс зарождения и роста новых недеформированных зерен при нагреве наклепанного металла до определенной температуры.
А.А. Бочвар показал, что между температурным порогом рекристаллизации и температурой плавления металлов имеется простое соотношение: рекристаллизация начинается при температуре, составляющей одинаковую для всех металлов долю от температуры плавления по абсолютной шкале, а именно Тп.р. = (0,3¸0,4)Тпл.
Для меди температурный порог рекристаллизации равен
Тп.р. = (1083+273)0,4–273 = 268 °С.
Выше этой температуры деформация называется горячей, ниже – холодной.
Вычертите диаграмму состояния железо-карбид железа, укажите структурные составляющие во всех областях диаграммы, опишите превращения и постройте кривую охлаждения (с применением правила фаз) для сплава, содержащего 4,3% С. Какова структура этого сплава при комнатной температуре и как такой сплав называется?
Первичная кристаллизация сплавов системы железо-углерод начинается по достижении температур, соответствующих линии ABCD (линии ликвидус), и заканчивается при температурах, образующих линию AHJECF (линию солидус).
При кристаллизации сплавов по линии АВ из жидкого раствора выделяются кристаллы твердого раствора углерода в α-железе (δ-раствор). Процесс кристаллизации сплавов с содержанием углерода до 0,1 % заканчивается по линии АН с образованием α (δ)-твердого раствора. На линии HJB протекает перитектическое превращение, в результате которого образуется твердый раствор углерода в γ-железе, т. е. аустенит. Процесс первичной кристаллизации сталей заканчивается по линии AHJE.
При температурах, соответствующих линии ВС, из жидкого раствора кристаллизуется аустенит. В сплавах, содержащих от 4,3 % до 6,67 % углерода, при температурах, соответствующих линии CD, начинают выделяться кристаллы цементита первичного. Цементит, кристаллизующийся из жидкой фазы, называется первичным. B точке С при температуре 1147°С и концентрации углерода в жидком растворе 4,3% образуется эвтектика, которая называется ледебуритом. Эвтектическое превращение с образованием ледебурита можно записать формулой ЖР4,3→Л[А2,14+Ц6,67]. Процесс первичной кристаллизации чугунов заканчивается по линии ECF образованием ледебурита.
Таким образом, структура чугунов ниже 1147°С будет: доэвтектических – аустенит + ледебурит, эвтектических – ледебурит и заэвтектических – цементит (первичный) + ледебурит.
Превращения, происходящие в твердом состоянии, называются вторичной кристаллизацией. Они связаны с переходом при охлаждении γ-железа в α-железо и распадом аустенита.
Линия GS соответствует температурам начала превращения аустенита в феррит. Ниже линии GS сплавы состоят из феррита и аустенита.
Линия ЕS показывает температуры начала выделения цементита из аустенита вследствие уменьшения растворимости углерода в аустените с понижением температуры. Цементит, выделяющийся из аустенита, называется вторичным цементитом.
В точке S при температуре 727°С и концентрации углерода в аустените 0,8 % образуется эвтектоидная смесь состоящая из феррита и цементита, которая называется перлитом. Перлит получается в результате одновременного выпадения из аустенита частиц феррита и цементита. Процесс превращения аустенита в перлит можно записать формулой А0,8П[Ф0,03+Ц6,67].
Линия PQ показывает на уменьшение растворимости углерода в феррите при охлаждении и выделении цементита, который называется третичным цементитом.
Следовательно, сплавы, содержащие менее 0,008% углерода (точкаQ), являются однофазными и имеют структуру чистого феррита, а сплавы, содержащие углерод от 0,008 до 0,03% – структуру феррит + цементит третичный и называются техническим железом.
Доэвтектоидные стали при температуре ниже 727ºС имеют структуру феррит + перлит и заэвтектоидные – перлит + цементит вторичный в виде сетки по границам зерен.
В доэвтектических чугунах в интервале температур 1147–727ºС при охлаждении из аустенита выделяется цементит вторичный, вследствие уменьшения растворимости углерода (линия ES). По достижении температуры 727ºС (линия PSK) аустенит, обедненный углеродом до 0,8% (точка S), превращаясь в перлит. Таким образом, после окончательного охлаждения структура доэвтектических чугунов состоит из перлита, цементита вторичного и ледебурита превращенного (перлит + цементит).
Структура эвтектических чугунов при температурах ниже 727ºС состоит из ледебурита превращенного. Заэвтектический чугун при температурах ниже 727ºС состоит из ледебурита превращенного и цементита первичного.
Правило фаз устанавливает зависимость между числом степеней свободы, числом компонентов и числом фаз и выражается уравнением:
C = K + 1 – Ф,
где С – число степеней свободы системы;
К – число компонентов, образующих систему;
1 – число внешних факторов (внешним фактором считаем только температуру, так как давление за исключением очень высокого мало влияет на фазовое равновесие сплавов в твердом и жидком состояниях);
Ф – число фаз, находящихся в равновесии.
Сплав железа с углеродом, содержащий 4,3% С, называется эвтетическим чугуном. Его структура при комнатной температуре Ледебурит (П+Fe3C).
а) б)
Рисунок 1: а-диаграмма железо-цементит, б-кривая охлаждения для сплава, содержащего 4,3% углерода
С помощью диаграммы состояния железо-цементит определите температуру нормализации, отжига и закалки для стали У10. Охарактеризуйте эти виды термической обработки и опишите структуру и свойства стали после каждого режима термообработки.
Отжигом называется нагрев стали выше температур фазовых превращений с последующим медленным охлаждением (обычно вместе с печью). При медленном охлаждении стали приближаются к фазовому и структурному равновесию. Структуры, полученные после отжига, указаны на диаграмме железо-цементит. После отжига сталь имеет низкую твердость и прочность. Основные цели отжига: перекристаллизация стали (измельчение зерна), снятие внутренних напряжений, снижение твердости и улучшение обрабатываемости. При комнатной температуре сталь У10 имеет структуру цементита и перлита. До температуры Аc1 сохраняется исходная структура. При температуре Аc1 происходит превращение перлита в аустенит с содержанием углерода 0,8%. При нагреве выше точки Ас1 происходит растворение цементита в аустените (в соответствии с линией SE). Увеличение температуры выше точки Асm вызывает рост зерна аустенита.
При нагреве заэвтектоидной стали выше Аcm (линия ES) и медленном охлаждении после такого нагрева образуется грубая сетка вторичного цементита, ухудшающая механические свойства. Для устранения грубой сетки вторичного цементита заэвтектоидные стали подвергают нормализации. Критические точки для стали У10: Аc1 = 730°С; Аcm = 800°С. Нормализация заэвтектоидной стали заключается в нагреве стали до температуры выше точки Асm на 40-50°С, в непродолжительной выдержке для прогрева садки и завершения фазовых превращений и охлаждении на воздухе. При температуре нагрева заэвтектоидной стали выше Аcm на 40-50°С имеем структуру аустенита (100%). При снижении температуры до Аrm начинают появляться первые зерна цементита. При дальнейшем снижении температуры до Аr1 из аустенита будут образовываться только зерна цементита, а содержание углерода в остающемся аустените будет уменьшаться и при температуре Аr1 достигнет 0,8%. Ускоренное охлаждение на воздухе способствует тому, что цементит не успевает образовать грубую сетку, понижающую свойства стали. При снижении температуры ниже Аr1 из аустенита будет образовываться перлит. Заэвтектоидная сталь после нормализации имеет структуру перлита и цементита.
Для закалки заэвтектоидные стали нагревают на 50-70°С выше точки Ас1. Таким образом, температура нагрева под закалку составляет 780-800°С. При этих температурах в стали наряду с аустенитом имеется цементит. Поэтому после закалки в структуре заэвтектоидных сталей будет мартенсит с цементитом и небольшое количество остаточного аустенита. Охлаждающая среда при закалке – индустриальное масло. Твердость поверхности после закалки 62-64 HRC. Для снятия напряжений и стабилизации структуры после закалки изделия подвергают низкому отпуску. В результате закалки из аустенита образуется неустойчивая, метастабильная структура мартенсит и цементит. Мартенсит представляет собой пересыщенный твердый раствор углерода в α-железе.
Углеродистые стали 45 и У8 после закалки и отпуска имеют структуру мартенсит отпуска и твердость: первая – 50 HRC, вторая – 60 HRC. Используя диаграмму состояния железо – карбид железа и учитывая превращения, происходящие в этих сталях в процессе закалки и отпуска, объясните, почему сталь У8 имеет большую твердость, чем сталь 45.
Закалка – термическая обработка – заключается в нагреве стали до температуры выше критической (А3 для доэвтектоидной и А1 – для заэвтектоидной сталей) или температуры растворения избыточных фаз, в выдержке и последующем охлаждении со скоростью, превышающей критическую.
В результате закалки из аустенита образуется неустойчивая, метастабильная структура мартенсит. Для стали 45 температура АС3 = 770°С, поэтому температуру закалки выбираем 810-840°С.
Для стали У8 критическая точка АС1 = 720°С, поэтому температура закалки равна 770-790°С.
Низкий отпуск снижает закалочные макронапряжения, мартенсит закалки переводится в отпущенный мартенсит, повышается прочность и немного улучшается вязкость без заметного снижения твердости. При отпуске уменьшается степень тетрагональности кристаллической решетки мартенсита вследствие выделения из нее углерода в виде ε-карбида.
Низкий отпуск для обеих сталей проводим при температуре 160-200ºС. Более высокие температуры применять не следует, так как это приводит к снижению твердости, статической и усталостной прочности, износостойкости изделий. Структура стали 45 – отпущенный мартенсит, стали У8 – отпущенный мартенсит + цементит (при доэвтектоидной концентрации углерода в стали У8 цементит выделяться не будет).
Рисунок 1 – Твердость мартенсита в зависимости от содержания углерода
Из рисунка 1 видно, что сталь У8 (0,8-0,9% С) после закалки имеет большую твердость, чем сталь 45 (0,42-0,50% С).
Источник
Металлическая связь — химическая связь, обусловленная наличием относительно свободных электронов. Характерна как для чистых металлов, так и их сплавов и интерметаллических соединений.
Механизм металлической связи
Во всех узлах кристаллической решётки расположены положительные ионы металла. Между ними беспорядочно, подобно молекулам газа движутся валентные электроны, отцепившиеся от атомов при образовании ионов. Эти электроны играют роль цемента, удерживая вместе положительные ионы; в противном случае решётка распалась бы под действием сил отталкивания между ионами. Вместе с тем и электроны удерживаются ионами в пределах кристаллической решётки и не могут её покинуть. Силы связи не локализованы и не направлены.
Поэтому в большинстве случаев проявляются высокие координационные числа (например, 12 или 8). Когда два атома металла сближаются, орбитали их внешних оболочек перекрываются, образуя молекулярные орбитали. Если подходит третий атом, его орбиталь перекрывается с орбиталями первых двух атомов, что дает еще одну молекулярную орбиталь. Когда атомов много, возникает огромное число трехмерных молекулярных орбиталей, простирающихся во всех направлениях. Вследствие многократного перекрывания орбиталей валентные электроны каждого атома испытывают влияние многих атомов.
Характерные кристаллические решётки
Большинство металлов образует одну из следующих высокосимметричных решёток с плотной упаковкой атомов: кубическую объемно центрированную, кубическую гранецентрированную и гексагональную.
В кубической объемно центрированной решётке (ОЦК) атомы расположены в вершинах куба и один атом в центре объёма куба. Кубическую объемно центрированную решётку имеют металлы: Pb, K, Na, Li, β-Ti, β-Zr, Ta, W, V, α-Fe, Cr, Nb, Ba и др.
В кубической гранецентрированной решётке (ГЦК) атомы расположены в вершинах куба и в центре каждой грани. Решётку такого типа имеют металлы: α-Ca, Ce, α-Sr, Pb, Ni, Ag, Au, Pd, Pt,Rh, γ-Fe, Cu, α-Co и др.
В гексагональной решётке атомы расположены в вершинах и центре шестигранных оснований призмы, а три атома — в средней плоскости призмы. Такую упаковку атомов имеют металлы: Mg, α-Ti, Cd, Re, Os, Ru, Zn, β-Co, Be, β-Ca и др.
Другие свойства
Свободно движущиеся электроны обусловливают высокую электро- и теплопроводность. Вещества, обладающие металлической связью, часто сочетают прочность с пластичностью, так как при смещении атомов друг относительно друга не происходит разрыв связей. Также важным свойством является металлическая ароматичность.
Металлы хорошо проводят тепло и электричество, они достаточно прочны, их можно деформировать без разрушения. Некоторые металлы ковкие (их можно ковать), некоторые тягучие (из них можно вытягивать проволоку). Эти уникальные свойства объясняются особым типом химической связи, соединяющей атомы металлов между собой – металлической связью.
Металлы в твердом состоянии существуют в виде кристаллов из положительных ионов, как бы “плавающих” в море свободно движущихся между ними электронов.
Металлическая связь объясняет свойства металлов, в частности, их прочность. Под действием деформирующей силы решетка металла может изменять свою форму, не давая трещин, в отличие от ионных кристаллов.
Высокая теплопроводность металлов объясняется тем, что если нагреть кусок металла с одной стороны, то кинетическая энергия электронов увеличится. Это увеличение энергии распространится в “ электронном море” по всему образцу с большой скоростью.
Становится понятной и электрическая проводимость металлов. Если к концам металлического образца приложить разность потенциалов, то облако делокализованных электронов будет сдвигаться в направлении положительного потенциала: этот поток электронов, движущихся в одном направлении, и представляет собой всем знакомый электрический ток.
Источник
Охарактеризуйте особенности металлического типа связи и основные свойства металлов.
Свойства обусловлены особенностями строения металлов. Согласно теории металлического состояния, металл представляет собой вещество, состоящее из положительных ядер, вокруг которых по орбиталям вращаются электроны. На последнем уровне число электронов невелико и они слабо связаны с ядром. Эти электроны имеют возможность перемещаться по всему объему металла, т.е. принадлежать целой совокупности атомов.
Металлы в твердом и отчасти в жидком состоянии обладают рядом характерных свойств:
– высокими теплопроводностью и электрической проводимостью;
– положительным температурным коэффициентом электрического сопротивления; с повышением температуры электрическое сопротивление чистых металлов возрастает; большое число металлов обладают сверхпроводимостью (у этих металлов при температуре, близкой к абсолютному нулю, электрическое сопротивление падает скачкообразно, практически до нуля);
– термоэлектронной эмиссией, т. е. способностью испускать электроны при нагреве;
– хорошей отражательной способностью: металлы непрозрачны и обладают металлическим блеском;
– повышенной способностью к пластической деформации.
Таким образом, пластичность, теплопроводность и электропроводность обеспечиваются наличием «электронного газа».
Какими стандартными характеристиками механических свойств оценивается прочность металлов и сплавов? Как эти характеристики определяются?
Прочность – свойство материалов в определенных условиях и пределах, не разрушаясь, воспринимать те или иные воздействия.
Диаграмма растяжения образца из низкоуглеродистой стали
Рисунок 1 – Диаграмма растяжения образца из низкоуглеродистой стали
Механические свойства стали (в т. ч. и прочность) обычно определяют по условной диаграмме растяжения. ГОСТ 1497-84 регламентирует следующие прочностные свойства:
– временное сопротивление разрыву (или предел прочности при растяжении) σВ – условное напряжение, соответствующее наибольшей нагрузке PD, предшествующей разрушению образца: σB = PD/F0 кгс/мм2;
– предел текучести σТ (физический) – наименьшее условное напряжение, при котором образец деформируется без заметного увеличения растягивающей нагрузки: σT=PC/F0 кгс/мм2; его определяют для низкоуглеродистой отожженной стали;
– предел текучести σ0,2 (условный) – напряжение, при котором остаточная деформация составляет 0,2% первоначальной расчетной длины; его определяют для большинства марок конструкционной среднеуглеродистой и легированной стали, у которых на диаграмме растяжения отсутствует «площадка текучести». Для определения условного предела текучести от начала координат диаграммы растяжения по оси абсцисс откладывают в соответствующем масштабе отрезок, составляющий 0,2% первоначальной длины; через полученную точку проводят прямую, параллельную начальному линейному участку (ОА) диаграммы (до пересечения с диаграммой). Ордината точки пересечения и соответствует условному пределу текучести σ0,2. Предел текучести σ0,2 можно определить по формуле σ0,2 = P0,2/F0 кгс/мм2;
– предел пропорциональности σп.ц. (условный) – напряжение, при котором отклонение от линейной зависимости между нагрузкой и деформацией достигает такой величины, что тангенс угла наклона диаграммы растяжения к оси нагрузок увеличивается на 50% по отношению к тангенсу угла между начальным линейным участком диаграммы и осью нагрузок. Допуск на увеличение тангенса этого угла может быть равным 10 или 25% (при наличии особых указаний в технических условиях). Величину допуска указывают в обозначении (например, σп.ц. 10; σп.ц. 25);
– предел упругости (условный) σ0,05 – напряжение, при котором остаточное удлинение достигает 0,05% первоначальной длины образца. Величину условного предела упругости определяют по той же методике, что и величину условного предела текучести;
– истинное сопротивление разрыву Sк – напряжение, определяемое отношением нагрузки Рк в момент разрыва к фактической площади поперечного сечения образца в месте разрыва Fк: Sк = Рк/Fк кгс/мм2.
Вычертите диаграмму состояния железо-карбид железа, укажите структурные составляющие во всех областях диаграммы, опишите превращения и постройте кривую охлаждения (с применением правила фаз) для сплава, содержащего 4,8% С. Какова структура этого сплава при комнатной температуре и как такой сплав называется?
Первичная кристаллизация сплавов системы железо-углерод начинается по достижении температур, соответствующих линии ABCD (линии ликвидус), и заканчивается при температурах, образующих линию AHJECF (линию солидус).
При кристаллизации сплавов по линии АВ из жидкого раствора выделяются кристаллы твердого раствора углерода в α-железе (δ-раствор). Процесс кристаллизации сплавов с содержанием углерода до 0,1 % заканчивается по линии АН с образованием α (δ)-твердого раствора. На линии HJB протекает перитектическое превращение, в результате которого образуется твердый раствор углерода в γ-железе, т. е. аустенит. Процесс первичной кристаллизации сталей заканчивается по линии AHJE.
При температурах, соответствующих линии ВС, из жидкого раствора кристаллизуется аустенит. В сплавах, содержащих от 4,3 % до 6,67 % углерода, при температурах, соответствующих линии CD, начинают выделяться кристаллы цементита первичного. Цементит, кристаллизующийся из жидкой фазы, называется первичным. B точке С при температуре 1147°С и концентрации углерода в жидком растворе 4,3 % образуется эвтектика, которая называется ледебуритом. Эвтектическое превращение с образованием ледебурита можно записать формулой ЖР4,3Л[А2,14+Ц6,67]. Процесс первичной кристаллизации чугунов заканчивается по линии ECF образованием ледебурита.
Таким образом, структура чугунов ниже 1147°С будет: доэвтектических — аустенит + ледебурит, эвтектических — ледебурит и заэвтектических — цементит (первичный) + ледебурит.
Превращения, происходящие в твердом состоянии, называются вторичной кристаллизацией. Они связаны с переходом при охлаждении γ-железа в α-железо и распадом аустенита.
Линия GS соответствует температурам начала превращения аустенита в феррит. Ниже линии GS сплавы состоят из феррита и аустенита.
Линия ЕS показывает температуры начала выделения цементита из аустенита вследствие уменьшения растворимости углерода в аустените с понижением температуры. Цементит, выделяющийся из аустенита, называется вторичным цементитом.
В точке S при температуре 727°С и концентрации углерода в аустените 0,8 % образуется эвтектоидная смесь состоящая из феррита и цементита, которая называется перлитом. Перлит получается в результате одновременного выпадения из аустенита частиц феррита и цементита. Процесс превращения аустенита в перлит можно записать формулой А0,8П[Ф0,03+Ц6,67].
Линия PQ показывает на уменьшение растворимости углерода в феррите при охлаждении и выделении цементита, который называется третичным цементитом.
Следовательно, сплавы, содержащие менее 0,008% углерода (точкаQ), являются однофазными и имеют структуру чистого феррита, а сплавы, содержащие углерод от 0,008 до 0,03% – структуру феррит + цементит третичный и называются техническим железом.
Доэвтектоидные стали при температуре ниже 727ºС имеют структуру феррит + перлит и заэвтектоидные – перлит + цементит вторичный в виде сетки по границам зерен.
В доэвтектических чугунах в интервале температур 1147–727ºС при охлаждении из аустенита выделяется цементит вторичный, вследствие уменьшения растворимости углерода(линия ES). По достижении температуры 727ºС (линия PSK) аустенит, обедненный углеродом до 0,8% (точка S), превращаясь в перлит. Таким образом, после окончательного охлаждения структура доэвтектических чугунов состоит из перлита, цементита вторичного и ледебурита превращенного (перлит+цементит).
Структура эвтектических чугунов при температурах ниже 727ºС состоит из ледебурита превращенного. Заэвтектический чугун при температурах ниже 727ºС состоит из ледебурита превращенного и цементита первичного.
Рисунок 2: а — диаграмма железо-цементит, б — кривая охлаждения для сплава, содержащего 4,8% углерода
Правило фаз устанавливает зависимость между числом степеней свободы, числом компонентов и числом фаз и выражается уравнением:
C = K + 1 – Ф,
где С – число степеней свободы системы;
К – число компонентов, образующих систему;
1 – число внешних факторов (внешним фактором считаем только температуру, так как давление за исключением очень высокого мало влияет на фазовое равновесие сплавов в твердом и жидком состояниях);
Ф – число фаз, находящихся в равновесии.
Сплав железа с углеродом, содержащий 4,8 %С, называется заэвтектическим чугуном. Его структура при комнатной температуре Цементит (первичный) + Ледебурит(П+Fe3C).
С помощью диаграммы состояния железо-карбид железа установите температуру полного и неполного отжига и нормализации стали 20. Охарактеризуйте эти режимы термической обработки и опишите структуру и свойства стали.
Полный отжиг.
При полном отжиге доэвтектоидная сталь нагревается выше АС3 на 30-50°С, выдерживается при этой температуре до полного прогрева и медленно охлаждается. В этом случае ферритно-перлитная структура переходит при нагреве в аустенитную, а затем при медленном охлаждении превращается обратно в феррит и перлит. Происходит полная перекристаллизация.
Основные цели полного отжига: устранение пороков структуры, возникших при предыдущей обработке металла (литье, горячей деформации, сварке и термообработке), смягчение стали перед обработкой резанием и снятие внутренних напряжений.
Для стали 20 отжиг проводится при температуре 880-900 °С.
Неполный отжиг.
Заключается в нагреве выше АС1 и медленном охлаждении. При этом происходит частичная перекристаллизация перлитной составляющей.
Неполному отжигу подвергаются доэвтектоидные стали с целью снятия внутренних напряжений и улучшения обрабатываемости резанием в том случае, если предварительная горячая обработка не привела к образованию крупного зерна.
Для стали 20 неполный отжиг проводится при температуре 760-790°С.
Нормализация.
Нормализация заключается в нагреве доэвтектоидной стали до температуры, превышающей точку АС3 на 40-50 °С, в непродолжительной выдержке для прогрева садки и завершения фазовых превращений и охлаждении на воздухе. Нормализация вызывает полную фазовую перекристаллизацию стали и устраняет крупнозернистую структуру, полученную при литье, прокатке, ковке или штамповке. Нормализацию широко применяют для улучшения свойств стальных отливок вместо закалки и отпуска.
Ускоренное охлаждение на воздухе приводит к распаду аустенита при более низких температурах, что повышает дисперсность феррито-цементитной структуры и увеличивает количество перлита или, точнее, сорбита или троостита. Это повышает прочность и твердость нормализованной средне- и высокоуглеродистой стали по сравнению с отожженной.
Нормализация горячекатаной стали повышает ее сопротивление хрупкому разрушению, что характеризуется снижением порога хладноломкости и повышением работы развития трещины.
Назначение нормализации различно в зависимости от состава стали. Для низкоуглеродистых сталей нормализацию применяют вместо отжига. При повышении твердости нормализация обеспечивает большую производительность при обработке резанием и получение более чистой поверхности. Для стали 20 нормализация проводится при температуре 900-920 °С.
Почему для изготовления инструмента применяется сталь с исходной структурой зернистого перлита? В результате какой термической обработки можно получить эту структуру? Приведите конкретный режим для любой инструментальной стали.
Углеродистые инструментальные стали У8 (У8А), У10 (У10А), У11 (У11А), У12 (У12А) и У13 (У13А) вследствие малой устойчивости переохлажденного аустенита имеют небольшую прокаливаемость, и поэтому эти стали применяются для инструментов небольших размеров.
Для заэвтектоидных сталей полный отжиг с нагревом выше Аст (линия ES) вообще не используют, так как при медленном охлаждении после такого нагрева образуется грубая сетка вторичного цементита, ухудшающая механические свойства. К заэвтектоидным углеродистым сталям широко применяют отжиг с нагревом до 740—780 °С и последующим медленным охлаждением. После такого нагрева в аустените остается большое число нерастворившихся включений цементита, которые служат центрами кристаллизации во время распада аустенита при охлаждении.
В результате образуется структура зернистого перлита (сферодита), почему этот отжиг и называют сфероидизирующим. Мелкие частицы цементита при температуре отжига в интервале А1–Аст получаются в результате деления цементитных пластин.
Для режима сфероидизирующего отжига заэвтектоидных сталей характерен узкий температурный «интервал отжигаемости». Нижняя его граница должна находиться выше точки А1, а верхняя граница не должна быть слишком высокой, так как иначе из-за растворения в аустените центров карбидного выделения при охлаждении образуется пластинчатый перлит. Так как точки Аст и А1 сходятся при эвтектоидной концентрации, то у сталей, близких к эвтектоидному составу, «интервал отжигаемости» особенно узок. Например, для сталей У9А и У10А границы этого интервала 740-750 °С, в то время как для сталей У11А, У12А и У13А они находятся в пределах 750-780 °С.
Конечная структура зависит от скорости охлаждения и температуры сфероидизирующего отжига. Чем меньше скорость охлаждения, тем до больших размеров вырастают глобули карбида при распаде аустенита. Регулируя скорость охлаждения, можно получать структуры глобулярного перлита от точечного до крупнозернистого. Более мелкозернистый перлит обладает повышенной твердостью.
С повышением температуры отжига до 800-820 °С твердость снижается из-за развития сфероидизации, а при дальнейшем увеличении температуры отжига твердость растет из-за появления все в большем количестве пластинчатого перлита.
Сфероидизирующему отжигу подвергают углеродистые и легированные инструментальные и шарикоподшипниковые стали.
Сталь со структурой зернистого перлита обладает наименьшей твердостью, легче обрабатывается резанием. Кроме того, зернистый перлит является оптимальной исходной структурой перед закалкой. При исходной структуре зернистого перлита меньше склонность к росту аустенитного зерна, шире допустимый интервал закалочных температур, меньше склонность к растрескиванию при закалке, выше прочность и вязкость закаленной стали (мелкие глобули равномерно распределены в мартенсите закаленной заэвтектоидной стали.
Поэтому металлургические заводы поставляют отожженную инструментальную сталь со структурой зернистого перлита.
Источник