Какие свойства приобретает сталь после закалки
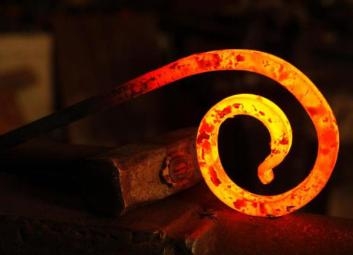
Закалкой называют вид термической обработки металлов, который заключается в нагреве выше критической температуры с последующим резким охлаждением (обычно) в жидких средах. Критической называют температуру, при которой происходит изменение типа кристаллической решетки, то есть осуществляется полиморфное превращение. Она определяется она по диаграмме «железо-углерод». фото
Свойства стали после закалки
После закалки увеличивается твердость и прочность стали, но при этом повышаются внутренние напряжения и возрастает хрупкость, провоцирующие разрушение материала при резких механических воздействиях. На поверхности изделия появляется толстый слой окалины, который необходимо учитывать при определении припусков на обработку.
Внимание! Некоторые изделия закаляются частично, например, это может быть только режущая кромка инструмента или холодного оружия. В этом случае на поверхности изделия можно наблюдать четкую границу, разделяющую закаленную и незакаленную части. Закаленную часть на клинках называют «хамон», что в переводе на современный язык металлургии означает «мартенсит».
Определение! Мартенсит – основная составляющая структуры стали после закалки. Вид этой микроструктуры – игольчатый или реечный.
Для уменьшения внутренних напряжений и роста пластичности осуществляют следующий этап термообработки – отпуск. При отпуске происходит некоторое снижение твердости и прочности.
Технология закалки
Режим закалки определяется температурой, временем выдержки, скоростью охлаждения, используемой охлаждающей средой.
Способы закалки стали:
- в одном охладителе – применяется при работе с деталями несложной конфигурации из углеродистых и легированных сталей;
- прерывистый в двух средах – востребован для обработки высокоуглеродистых марок, которые сначала остужают в быстро охлаждающей среде (воде), а затем в медленно охлаждающей (масле);
- струйчатый – обычно востребован при частичной закалке изделия, осуществляется в установках ТВЧ и индукторах обрызгиванием детали мощной струей воды;
- ступенчатый – процесс, при котором деталь остывает в закалочной среде, приобретая во всех точках сечения температуру закалочной ванны, окончательное охлаждение осуществляют медленно;
- изотермический – похож на предыдущий вид закалки стали, отличается от него временем пребывания в закалочной среде.
Типы охлаждающих сред
От правильного выбора охлаждающей среды во многом зависит конечный результат процесса.
- Для поверхностной закалки и работы с изделиями простой конфигурации, предназначенными для дальнейшей обработки, применяется в основном вода. Она не должна содержать соли и примеси моющих средств, оптимальная температура +30°C.
- Для изделий сложной формы применяют 50% раствор каустической соды, который нагревают до +60°C. При использовании такого состава для охлаждения сталь приобретает светлый оттенок. Пары каустической соды вредны для здоровья человека.
- Для тонкостенных деталей, изготовленных из углеродистых и легированных сталей, применяются минеральные масла, обеспечивающие постоянную температуру охлаждения, не зависящую от температуры окружающей среды. Главное условие, которое необходимо соблюдать при охлаждении сталей после закалки, – отсутствие воды в минеральных маслах. Недостатки процесса: выделение вредных для человека паров, возможность возгорания масла, образование налета, постепенная потеря эффективности охлаждающего состава.
Внимание! Использовать этот способ охлаждения для деталей сложной конфигурации не рекомендуется из-за риска появления трещин.
Внимание! Для работы с изделиями из углеродистых сталей со сложным химическим составом используют комбинированное охлаждение. Оно состоит из двух этапов. Первый – охлаждение детали в воде, второй, после +200°C, – в масляной ванне. Перемещение из одной охлаждающей среды в другую должно производиться очень быстро.
Какие стали можно закаливать?
Процедурам закалки и отпуска не подвергается прокат и изделия из него, изготовленные из малоуглеродистых сталей типа 10, 20, 25. Этот вид термообработки эффективен для углеродистых сталей (45, 50) и инструментальных, у которых в результате твердость увеличивается в три-четыре раза.
Таблица режимов закалки и областей применения для некоторых видов инструментальных сталей
Марка стали | Для какого инструмента используется | Температура закалки, °C | Температура отпуска, °C | Охлаждающая среда для закалки | Охлаждающая среда для отпуска |
У7 | Молотки, кувалды, плотницкий инструмент | 800 | 170 | Вода | Вода, масло |
У7А | Зубила, отвертки, клейма, топоры | 800 | 170 | Вода | Вода, масло |
У8, У8А | Пуансоны, матрицы, стамески, пробойники, ножовочные ручные полотна | 800 | 170 | Вода | Вода, масло |
У10, У10А | Деревообрабатывающий инструмент, керны, резцы строгальные и токарные | 790 | 180 | Вода | Вода, масло |
У11 | Метчики | 780 | 180 | Вода | Вода, масло |
У12 | Надфили | 780 | 180 | Вода | Вода, масло |
Р9 | Метчики, ножовочные полотна станочные, сверла по металлу, фрезы | 1250 | 580 | Масло | Воздух в печи |
Р18 | Ножовочные полотна станочные, сверла по металлу, фрезы | 1300 | 580 | Масло | Воздух в печи |
ШХ6 | Напильники | 810 | 200 | Масло | Воздух |
ШХ15 | Ножовочные полотна станочные | 845 | 400 | Масло | Воздух |
9ХС | Плашки, сверла спиральные по дереву | 860 | 170 | Масло | Воздух |
Как закалить сталь в домашних условиях?
Закалку и отпуск желательно осуществлять в производственных условиях с использованием специального оборудования и приборов. Однако домашние умельцы часто практикуют это в собственных мастерских. Для нагрева изделия используют электроплиты, духовки, раскаленный песок, паяльные лампы, костер. Самостоятельная термообработка оправдана в случае необходимости упрочнения режущей кромки инструмента.
Как сделать закаленную сталь:
- перед термообработкой изделие необходимо очистить от масла и ржавчины;
- равномерно разогреть;
- охладить и произвести отпуск в соответствии с режимами, рекомендованными для конкретной марки стали.
При необходимости проведения термообработки в домашних условиях в отсутствии приборов температуру металла ориентировочно определяют по цветам побежалости. Условие – помещение не должно быть освещено солнцем.
Определение! Цветами побежалости называют оксидные пленки, образующиеся без участия молекул воды на сплавах на основе железа во время нагрева. Каждому интервалу температур соответствует определенный цвет:
- темно-коричневый – 530-580°C;
- коричнево-красный – 580-650°C;
- вишневый – 650-730°C;
- вишнево-красный – 730-770°C;
- вишнево-алый – 770-800°C;
- светло-вишнево-алый – 800-830°C;
- ярко-красный – 830-870°C;
- красный – 870-900°C;
- оранжевый – 900-1050°C;
- темно-желтый – 1050-1150°C;
- светло-желтый – 1150-1250°C;
- желто-белый – 1250-1300°C;
ослепительно белый – более 1300°C.
Источник
Сталь после закалки: структура и свойства
Сталь в обычном виде – довольно мягкий и податливый к обработке металл. Особая прочность некоторым маркам (это так называемые стали обыкновенного качества, производимые согласно требованиям ГОСТ 380) и не требуется: тех показателей, что были получены после выплавки, вполне хватает, например, канализационным люкам или оградительным решёткам. Но есть категории сталей – конструкционные и инструментальные, которым изначальных прочностных показателей мало. Их надлежит подвергать термической обработке. Основным её видом считается закалка.
Микроструктура стали 45 после отжига и закалки
Закалка: сущность операции
Как известно, любая сталь представляет собой твёрдый раствор углерода в основной структуре α-железа. При этом марка определяет процентное содержание углерода (например, марка «сталь 65» означает, что в её составе содержится 0,65% С, сталь У13 содержит около 1,3% С, и так далее). Однако этот элемент – довольно химически активный, поэтому в процессе выплавки (при 1600…2000 °С) он активно связывается железом, образуя в результате цементит Fe3C. Всё остальное представляет собой феррит – достаточно мягкую структурную составляющую. Большое количество феррита в малоуглеродистых сталях обуславливает их повышенную пластичность, причём даже в холодном состоянии. Это не касается сталей:
- легированных (они производятся согласно требованиям ГОСТ 4543);
- подшипниковых по ГОСТ 801;
- рессорно-пружинных по ГОСТ 2052 и ГОСТ 14959;
- всех типов инструментальных, как легированных, так и нелегированных.
Чтобы понять эффективность закалки, необходимо обратиться к структуре стали после выплавки и последующей горячей прокатки на необходимый профиль – полосу, пруток или специальный профиль (уголок, швеллер и т.п.).
Любая сталь имеет кристаллическую структуру, которую составляет бесконечное множество кристаллов. Если лить сталь с последующим охлаждением расплава, то эти кристаллы превращаются в многогранные образования, называемые зёрнами. Поскольку при этом происходит активное насыщение кислородом, между смежными кристаллами возникают пустоты, которые в процессе охлаждения слитка постепенно заполняются серой, фосфором и прочими легкоплавкими неметаллическими включениями. Это не только снижает пластичность (фосфор и сера – весьма хрупкие химические элементы), но и способствует появлению весьма грубых скоплений зёрен, что делает металл неравномерным по своей плотности. Обрабатывать такие изделия невозможно – слиток начнёт раскалываться. Поэтому сразу после выплавки выполняется прокатка, в ходе которой исходные дефекты залечиваются, и структура становится более однородной. Соответственно, увеличивается плотность, а также исчезают поверхностные трещины.
Температура заготовки в зависимости от цвета при нагреве
Пластическая деформация положительно влияет только на макроструктуру. За изменение микроструктуры отвечает закалка – совокупность технологических методов термической обработки, суть которых состоит в увеличении прочностных показателей стали. Смысл закалки заключается в том, чтобы зафиксировать ряд высокотемпературных составляющих микроструктуры (придающих стали стойкость) для обычных условий эксплуатации изделий. Соответственно, сталь, не изменяя своего химического состава, резко повысит уровень своих некоторых механических характеристик:
- предела временного сопротивления σв, МПа;
- предела текучести σт, МПа;
- предела усталости σи, МПа;
- твёрдости по Бринеллю HB или Роквеллу НRC.
При этом некоторые показатели – в частности, ударная вязкость, относительное удлинение, – после закалки становятся ниже. Если это критично с точки зрения последующей эксплуатационной стойкости детали (а в большинстве случаев так и происходит), то правильно после её закалки выполнить ряд дополнительных операций: отпуск, старение и др.
Температурные изменения в структуре
Закалка проводится весьма часто для продукции, изготовленной из качественных конструкционных сталей, содержащих более 0,4% С, и практически всегда – для конструкционных легированных сталей, поскольку именно для них обычно и предъявляются повышенные прочностные требования.
Выбор режима закалки зависит от предназначения детали. Наиболее распространены следующие технологии:
- Термообработка малоуглеродистых конструкционных сталей (менее 0,2% С), для которых необходимо сочетание поверхностной твёрдости с достаточно вязкой сердцевиной. В этом случае сначала выполняют цементацию — насыщение поверхности дополнительным количеством углерода, а уже потом сталь закаливают;
- Термообработка среднеуглеродистых сталей с 0,3…0,6% С. Они применяются для производства ответственных машиностроительных изделий сложной формы, которые работают в условиях знакопеременных нагрузок. Нормализация всегда выполняется после закалки;
- Химико-термическая обработка, которая выполняется относительно высоколегированных сталей, где глубинные слои могут оставаться вязкими. Основные варианты исполнения такой обработки – цианирование, нитридирование, сульфурирование – производятся также после закалки.
3 формы кристаллов железа в сверхвысокоуглеродистой стали
Все конструкционные стали относятся к виду доэвтектоидных: процентное содержание углерода в них не превышает 0,8%. В структуре стали после закалки в зависисмотси от условий нагрева имеются следующие составляющие:
- В диапазоне температур до 723 °С – феррит и перлит (перлит представляет собой механическую смесь феррита и цементита, куда подмешиваются и карбиды легирующих элементов).
- Выше этой температуры и до 850…900 °С– смесь феррита с аустенитом, причём область устойчивого существования структуры зависит от процента углерода, и постепенно снижается от диапазона 950…723 °С до 0.
- Ниже этой температурной линии структура является уже чисто аустенитной.
Для отображения динамики структурных изменений в конструкционных сталях при их нагреве широко применяется известная диаграмма «железо-углерод», по которой устанавливают режимы закалки и последующего отпуска. Часто тут же приводятся и фотографии структурных составляющих.
Режимы закалки
Поскольку при закалке растут не только прочностные характеристики, но и хрупкость, технология правильного ведения процесса состоит в том, чтобы, с одной стороны, зафиксировать так можно большее количество остающегося аустенита, а другой стороны, снизить негативные проявления таких изменений. Особенно это важно для деталей сложной формы, где уже имеются концентраторы напряжений.
Задача решается ускоренным охлаждением деталей, нагретых выше температуры аустенитного превращения на 30…50 °С, с последующим отпуском. В качестве охлаждающей среды используется вода или масло, а итогом такого охлаждения является появление в микроструктуре мартенсита – пересыщенного твёрдого раствора углерода в железе. Мартенсит — значительно более твердая структура, с иным типом кристаллической решётки и игольчатой структурой кристаллов. Он считается так называемой метастабильной фазой, которая в обычных условиях существовать не может.
Закалка подразделяется на следующие виды:
- Изотермическую, при которой выполняется непрерывное охлаждение в масле, либо в расплавах солей хлоридов бария и натрия. В результате аустенитное превращение протекает полностью, а в закалённом продукте исключаются трещинообразование и коробление. Изотермическая закалка и отпуск обязательны для конструкций сложной формы и значительных габаритных размеров.
- Ступенчатую, при которой после закалки в ванне до окончания мартенситного превращения и выравнивания температурных перепадов по всему сечению, продукцию извлекают из закалочной ёмкости, и в дальнейшем охлаждают уже на спокойном воздухе.
- Сквозную, применяемую для деталей небольших размеров. В результате получается наивысшая равномерность механических свойств.
Три вида отпуска после закалки
Особенности закалки инструментальных сталей заключаются в том, что они работают при гораздо повышенных эксплуатационных нагрузках: например, для тяжелонагруженного инструмента они достигают 3000…3500 МПа. Поэтому крайне важно обеспечить удовлетворительное сочетание всех прочностных параметров. Принципиальным отличием всех режимов закалки инструментальных сталей является обязательность отпуска непосредственно после закалки.
Наилучший результат дают следующие режимы закалки:
- Изотермическая.
- Закалка с самопроизвольным отпуском, при которой нагретую деталь кратковременно извлекают из охлаждающей среды (масла), очищают от образовавшейся плёнки окислов, после чего вновь опускают в масляную ванну.
- Чистая, при которой нагрев ведут в печах с контролируемой атмосферой, свободной от окислов.
- Светлая, когда продукция нагревается в щелочных расплавах.
Нагрев под закалку проводят преимущественно в электропечах или в газовых печах, атмосфера которых содержит инертный газ. Так обеспечивается качество и полнота мартенситного превращения, исключаются неравномерность свойств и поверхностные дефекты.
Источник
Все о технологии закалки стали: что это такое, для чего нужно, какие способы существуют. Температуры, которым подвергается металл. Как изменяются свойства стали. Методы нагрева и среды охлаждения. Оборудование для термообработки. Дефекты при закалке.
Закалка стали проводится для повышения ее твердости, прочности и износостойкости. Это один из видов термической обработки, при котором металл сначала нагревается до температур, изменяющих его структурное состояние, а затем охлаждается таким образом, чтобы он приобрел требуемый физико-химический состав и необходимую кристаллическую структуру. Существует множество способов закалки стали, приводящих к различным результатам, но все они состоят из двух основных циклов: нагрева до критической точки и охлаждения с определенной скоростью до заданной температуры. Еще одна технологическая операция, используемая в процессе закалки металлов, — это отпуск, при котором структурные изменения происходят после нагрева до невысокой температуры с медленным охлаждением. Возможность изменения характеристик стали посредством закаливания во многом связана с ее изначальной кристаллической структурой и химическим составом, в котором самыми важными компонентами являются углерод и легирующие добавки. Именно они определяют, какой будет форма, размер и конфигурация элементов структуры стали после ее термической обработки.
Какие металлы подлежат калению
Закалка металла — это термическая обработка, которой чаще всего подвергаются углеродистые и легированные стали с целью повышения их твердости и улучшения прочностных характеристик. Несколько реже встречается термообработка цветных металлов, в частности отпуск, отжиг и закалка меди, латуни и бронзы, а также сплавов алюминия и титана. Необходимо отметить, что закаливание этих соединений в отличие от углеродистых сталей не всегда приводит к их упрочнению, некоторые сплавы меди после этого, наоборот, становятся более пластичными и мягкими. Гораздо чаще изделия из цветных металлов подвергаются отпуску для снятия напряжения после отливки, штамповки, прокатки или волочения.
Свойства стали после закалки
Углеродистая сталь в процессе нагрева проходит через ряд фазовых изменений своей структуры, при которых меняется ее состав, а также форма и элементов кристаллической решетки. При критической температуре 723 °C в еще твердом металле начинается распад цементита (карбида железа) и формирование равномерного раствора углерода в железе, который называется аустенит. Это состояние углеродистой стали является исходным для закалки.
При медленном охлаждении аустенит распадается, и металл возвращается в исходное состояние. Если же сталь охлаждать быстро, то аустенит не успевает изменяться, и при определенной скорости охлаждения и пороговых температурах формируются кристаллические решетки и химические составы, придающие ей различные эксплуатационные свойства. Этот процесс называется закалкой, и каждому его виду соответствует определенная структура уже закаленной стали, обладающей определенными техническими характеристиками. Основные фазовые состояния, имеющие значения при закалке, — это перлит, сорбит, троостит и мартенсит (см. рис. ниже).
Самая высокая твердость у стали, закаленной до состояния мартенсита. Таким способом производят закаливание режущего инструмента, а также осуществляют упрочнение поверхностей деталей, подвергающихся в процессе работы трению (втулки, обоймы, валы, шестерни и пр.). После выполнения закалки на троостит сталь становится одновременно твердой и упругой. Этой вид термообработки применяют к ударному инструменту, а также рессорам и пружинным амортизаторам. Для получения таких свойств стали, как стойкость к износу, упругость и вязкость, используют закалку до состояния сорбита. Такая термообработка используется для рельсов и других конструктивных элементов, работающих под постоянной динамической нагрузкой. Перечисленные фазовые состояния свойственны всем углеродистым сталям, но каждая их марка характеризуется своими температурными диапазонами и скоростями охлаждения.
Классификация каления стали
Виды закалки сталей классифицируют по типу источника нагрева и способу охлаждения металла. Основным оборудованием для нагрева деталей перед закаливанием по-прежнему являются муфельные печи, в которых можно равномерно разогревать металлические изделия любых размеров. Высокую скорость нагрева при поточной обработке изделий обеспечивает закалка с применением токов высокой частоты (индукционная закалка сталей) (см. фото ниже). Для закаливания верхних слоев стальных изделий применяют довольно недорогую и эффективную газопламенную закалку, главный недостаток которой — невозможность точно задать глубину прогрева. Этих недостатков лишена лазерная закалка, но ее возможности ограничены небольшой мощностью источника излучения. Способы охлаждения закаливаемой детали обычно классифицируют по виду охлаждающей среды, а также совокупностям и циклам рабочих операций. Некоторые из них включают процедуры отпуска, а для других, таких как разные виды изотермической закалки, он не нужен.
Закаливание в одной среде
При таком способе закалки нагретое до заданной температуры изделие из стали помещают в жидкость, где она остается до полного остывания. В качестве закалочной среды для углеродистых сталей используют воду, а для легированных — минеральное масло. Недостаток этого метода заключается в том, что после такого закаливания в металле сохраняются значительные напряжения, поэтому в ряде случаев может потребоваться дополнительная термообработка (отпуск).
Ступенчатая закалка
Ступенчатое закаливание проходит в два этапа. На первом изделие помещается в среду с температурой, превышающей на несколько десятков градусов точку начала возникновения мартенсита. После того, как температура выравнивается по всему объему металла, деталь медленно охлаждается, в результате чего в нем равномерно формируется мартенситная структура.
Изотермическая закалка
При изотермическом закаливании изделие также выдерживается в закалочной ванне при температуре, превышающей точку мартенсита, но несколько дольше. В результате этого аустенит трансформируется в бейнит — одну из разновидностей троостита. Такая сталь сочетает в себе повышенную прочность с пластичностью и вязкостью. Кроме того, после изотермической закалки в изделии снижаются остаточные напряжения.
Закалка с самоотпуском
Этот вид термообработки используется для закаливания ударного инструмента, который должен обладать твердым поверхностным слоем и вязкой серединой. Его особенность заключается в том, что изделие извлекается из закалочной емкости при неполном охлаждении. В этом случае его внутренняя часть еще содержит достаточное количество тепла, чтобы прогреть весь объем металла до температуры отпуска. Так как повторный нагрев изделия осуществляется без внешнего воздействия за счет внутренней тепловой энергии, такой вид термической обработки называют закалкой с самоотпуском.
Светлая закалка
Светлая закалка применяется для стальных изделий, поверхности которых при термообработке не должны подвергаться окислению. При такой термообработке сталь нагревается в вакуумных печах (см. фото ниже) или в инертных газовых средах (азот, аргон и пр.), а охлаждается в неокисляющих жидкостях или расплавах. Этим способом закаливают изделия, которые не должны подвергаться дальнейшей шлифовке, а также детали, критичные к содержанию углерода в поверхностном слое.
Оборудование для термообработки сталей
Основное оборудование, на котором проводится термическая обработка изделий из сталей и цветных металлов, состоит из двух основных групп: установок для нагрева заготовок и закалочных ванн. Нагревательные устройства включают в себя следующие виды оборудования:
- муфельные термопечи;
- устройства индукционного нагрева;
- установки для нагрева в расплавах;
- газоплазменные установки;
- аппараты лазерной закалки.
Первые три вида могут выполнять прогрев всего объема изделия до требуемой температуры, а последние — только поверхностного слоя металла. Кроме того, выпускаются и широко используются печи для закалки металлов, в которых нагрев осуществляется в вакууме или в среде инертного газа.
Закалочные ванны представлены стальными емкостями-охладителями для различных жидкостей, а также специальными тиглями из графита и печами для расплавов солей или металлов. В качестве закалочных жидкостей чаще всего используют минеральное масло, воду и водополимерные смеси. Для расплавов металлов обычно применяют свинец или олово, а для расплавов солей — соединения натрия, калия и бария. Закалочные ванны для жидких сред имеют системы нагрева и охлаждения рабочей жидкости до требуемой температуры, а также мешалки для равномерного распределения жидкости и разрушения паровой рубашки.
Температура для закалки
Нормативная температура нагрева стали при ее закалке напрямую зависит от массовой доли углерода и легирующих добавок. В целом наблюдается следующая зависимость: чем меньше содержание углерода, тем выше температура закалки. При недогреве изделия не успевает сформироваться требуемая структура, а при значительном перегреве происходит обезуглероживание, окисление поверхностного слоя, изменение формы и размера структурных элементов, а также рост внутреннего напряжения. В таблице ниже приведены температуры закалки, отжига и отпуска некоторых марок углеродистых и легированных сталей.
Марка стали | Температура, С | ||
---|---|---|---|
закалки | отжига | отпуска | |
15Г | 800 | 780 | 200 |
65Г | 815 | 790 | 400 |
15Х, 20Х | 800 | 870 | 400 |
30Х, 35Х | 850 | 880 | 450 |
40Х, 45Х | 840 | 860 | 400 |
50Х | 830 | 830 | 400 |
50Г2 | 805 | 830 | 200 |
40ХГ | 870 | 880 | 550 |
ОХ13 | 1050 | 860 | 750 |
3Х13 | 1050 | 880 | 450 |
35ХГС | 870 | 860 | 500 |
30ХГСА | 900 | 860 | 210 |
У7, У7А | 800 | 780 | 170 |
Р9, Р12 | 1250 | 860 | 580 |
Р9Ф5, Р9К5 | 1250 | 860 | 590 |
Р18Ф2 | 1300 | 900 | 590 |
ШХ15 | 845 | 780 | 400 |
9ХС | 860 | 730 | 170 |
Р18К5Ф2 | 1280 | 860 | 580 |
1Х14Н18Б2БРГ | 1150 | 860 | 750 |
4Х14Н1482М | 1200 | 860 | 750 |
Определение температуры нагрева в промышленном производстве осуществляется посредством контактных и бесконтактных пирометров. В последние десятилетия широкое распространение получили инфракрасные приборы, позволяющие дистанционно замерять температуру в любой точки поверхности нагретой детали. Кроме того, приблизительную температуру разогрева стали можно определить по цветовым таблицам.
Технология каления металла
Технология закалки сталей требует соблюдения ряда требований к процессам нагрева и охлаждения закаливаемых деталей. В первую очередь это относится к скорости разогрева и охлаждения металла. Экономические показатели термического процесса требуют максимально быстрого повышения температуры до номинальной, т. к. при этом расходуется меньше энергии. Однако скоростной нагрев приводит к большому перепаду температур между поверхностным слоем и сердцевиной изделия, что может привести к его деформации и возникновению трещин. Поэтому прогрев на всю глубину детали до полного ее разогрева должен проходить плавно, а его время определяется технологом-термистом с помощью эмпирических формул и табличных значений.
От скорости и температурных параметров охлаждения стали, разогретой выше критической точки, напрямую зависит процесс формирования структуры и состава закаленного металла. К примеру, при быстром охлаждении в воде с комнатной температурой можно получить углеродистую сталь с мартенситной структурой, а при охлаждении в масле или горячей воде получается троостит. Каждой марке стали соответствуют свои характеристики и температурные режимы закалки, которые, помимо прочего, зависят от размера и формы детали. Поэтому на производстве термическая обработка деталей проводится в соответствии с маршрутной технологией и операционными картами, разрабатываемыми для каждого изделия.
Способы охлаждения
Охлаждая сталь до разных температур и с разными скоростями, можно получить различные структуры ее кристаллической решетки с элементами разного размера и формы. Совокупность этих характеристик с химическим составом определяет такие ее эксплуатационные качества, как твердость, хрупкость, вязкость, прочность, упругость и пр. Поэтому существует множество технологий охлаждения и их разновидностей, среди которых можно выделить следующие технологические группы:
- Охлаждение в одном компоненте. Изделие погружается в жидкость и остается в ней до полного остывания.
- Прерывистая закалка в двух охладителях. Изделие сначала помещают в быстроохлаждающую жидкость, а после достижения заданной температуры переносят в среду с медленным охлаждением.
- Струйное охлаждение. Разогретая деталь интенсивно орошается потоком охладителя (см. фото ниже).
- Обдув. Поверхность изделия обдувается потоком воздуха или инертного газа.
При практическом применении закалки все эти виды охлаждений могут иметь различные вариации или комбинироваться друг с другом.
Среды охлаждения
В качестве охлаждающих жидкостей при закалке углеродистых сталей обычно используют воду: как чистую, так и в виде водных растворов (солевых и щелочных). Легированные стали требуют меньшей скорости охлаждения, поэтому для них применяют минеральные масла и воздух. При ступенчатой и изотермической закалке охлаждающей средой служат расплавы солей, щелочей и металлов. При некоторых видах закалки для получения требуемой структуры стали среды охлаждения чередуются.
№ | Структура | Среда охлаждения | Твердость (HBW) |
---|---|---|---|
1 | Мартенсит | Холодная вода | 500÷750 |
2 | Троостит | Масло | 350÷500 |
3 | Сорбит | Воздух | 250÷350 |
4 | Перлит | С остыванием печи | 150÷250 |
Влияние скорости охлаждения на конечный результат
При закалке стали охлаждение должно идти со скоростью, предотвращающей распад аустенита на феррит и карбид железа, которое начинает происходить при температуре ниже 650 °C. Дальнейшее снижение температуры следует проводить медленнее, т. к. такая скорость обеспечивает уменьшение внутренних напряжений стали. Быстрое и полное охлаждение в холодной воде позволяет получить мартенсит, который обладает максимальной твердостью, но довольно хрупок. При быстром понижении температуры на 200÷300 °C распад аустенита прекращается, а дальнейшее более медленное охлаждение формирует в стали фазовые состояния с меньшей твердостью, но обладающие повышенной прочностью и износостойкостью. Скорость охлаждения регулируется видом используемой закалочной среды и ее температурой (см. таблицу ниже).
№ | Среда охлаждения | Скорость охлаждения (град/сек) |
---|---|---|
1 | Воздух | 5 |
2 | Минеральное масло | 150 |
3 | Вода при комн. t° | 700 |
4 | Вода при 80 °C | 1400 |
5 | 10%-й р-р хлористого натрия | 2100 |
6 | 10%-й р-р едкого натра | 1600 |
Отличия закаливаемости от прокаливаемости
Каждая марка стали обладает определенной закаливаемостью, которая характеризуется ее способностью приобретать при закалке требуемую твердость. Основные факторы, влияющие на закаливаемость стали, — это процентные доли углерода и легирующих добавок. Нижний предел содержания углерода, после которого сталь не воспринимает закалку, равен 0.2 %. Прокаливаемость характеризуется глубиной проникновения в объем металла закаленной структуры (полностью мартенситной или состоящей из троостита и мартенсита). Легирующие добавки в виде молибдена, хрома, никеля и пр. увеличивают как закаливаемость, так и прокаливаемость, а добавление кобальта их понижает.
Дефекты при закаливании стали
Причиной возникновения дефектов при закалке стали является ряд физических и химических факторов, возникающих при отклонении от заданных параметров термического процесса или из-за неоднородности закаливаемой заготовки. Неравномерный нагрев или охлаждение изделия может привести к его деформации и возникновению внутренних трещин. Эта же причина может вызвать неодинаковость фазовых превращений в различных частях изделия, в результате чего металл будет иметь неоднородную по составу и твердости структуру. Пережог стали происходит вследствие проникновения кислорода в поверхностный слой металла, что приводит к возникновению окислов, разъединяющих его структурные элементы и изменяющих физические свойства поверхностного слоя. Причиной обезуглероживания при закалке стали является выгорание углерода при попадании в печь избыточного количества кислорода. Эти виды дефектов неисправимы, а единственный способ борьбы с ними — это проверка герметичности печи или закалка в вакууме и инертных газах.
Окалины и критическое снижение концентрации углерода при калении
Даже небольшая концентрация кислорода в закалочной печи приводит к появлению поверхностной окалины, которая является следствием окисления металла при его термообработке. Эта же причина может вызвать уменьшение количества углерода в поверхностном слое заготовки. Полностью избавиться от таких явлений можно только путем применения вакуумных печей, обеспечивающих так называемую светлую закалку, а также при нагреве изделия в среде азота или аргона. Для минимизации окисления и обезуглероживания закалочная печь должна быть максимально ге