Какие свойства металлов и их сплавов относятся к технологическим
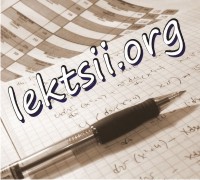
Пластичность
Одним из основных свойств металлов является их пластичность, т.е способность металла, подвергнутого нагрузке, деформироваться под действием внешних сил без разрушения и давать остаточную (сохраняющуюся после снятия нагрузки) деформацию. Пластичность иногда характеризуют величиной удлинения образца при растяжении.
Отношение приращения длины образца при растяжении к его исходной длине, выражаемое в процентах, называется относительным удлинением и обозначается δ, %. Относительное удлинение определяется после разрыва образца и указывает способность металла удлиняться под действием растягивающих усилий.
Ковкость
Способность металла без разрушения поддаваться обработке давлением (ковке, прокатке, прессовке и т.д.) называется его ковкостью. Ковкость металла зависит от его пластичности. Пластичные металлы обычно обладают и хорошей ковкостью.
Усадка
Усадкой металла называется сокращение объема расплавленного металла при его застывании и охлаждении до комнатной температуры.
Соответствующее изменение линейных размеров, выраженное в процентах, называется линейной усадкой.
Жидкотекучесть
Способность расплавленного металла заполнять форму и давать хорошие отливки, точно воспроизводящие форму, называется жидкотекучестью. Кроме хорошего заполнения формы, лучшая жидкотекучесть способствует получению здоровой плотной отливки благодаря более полному выделению из жидкого металла газов и неметаллических включений. Жидкотекучесть металла определяется его вязкостью в расплавленном состоянии.
Износостойкость
Способность металла сопротивляться истиранию, разрушению поверхности или изменению размеров под действием трения называется износостойкостью.
Коррозионная стойкость
Способность металла сопротивляться химическому или электрохимическому разрушению его во внешней влажной среде под действием химических реактивов и при повышенных температурах называется коррозионной стойкостью.
Обрабатываемость
Способность металла обрабатываться при помощи различных режущих инструментов называется обрабатываемостью.
Углеродистые инструментальные стали
Углеродистые инструментальные стали бывают качественные и высококачественные.
Высококачественные углеродистые инструментальные стали, выплавляемые в электропечах, маркируются таким же образом, но с добавлением в конце буквы А, т. е. У7А, У8А и т. д. Буква А обозначает, что сталь является высококачественной (улучшенной), по составу более чистой, с пониженным содержанием серы (до 0,03%), фосфора (также до 0,03%), остаточных примесей и неметаллических включений. Содержание марганца в этих сталях колеблется в пределах от 0,15 до 0,40%; кремния от 0,15 до 0,35%.
Достоинством инструментальных углеродистых сталей является их хорошая обрабатываемость, невысокая твердость (160-180 НВ). Однако они имеют и крупные недостатки: небольшой интервал закалочных температур, необходимость быстрого охлаждения в воде при закалке, что приводит к короблению, деформации инструментов и даже образованию трещин.
Инструментальная углеродистая сталь применяется для изготовления различных инструментов (режущих, мерительных и др.), которые должны обладать высокой износоустойчивостью и красностойкостью.
Понятие термической обработки металлов
Термической обработкой называется совокупность операций нагрева, выдержки и охлаждения твердых металлических сплавов с целью получения заданных свойств за счет изменения внутреннего строения и структуры. Термическая обработка используется либо в качестве промежуточной операции для улучшения обрабатываемости давлением, резанием, либо как окончательная операция технологического процесса, обеспечивающая заданный уровень свойств детали.
Общая длительность нагрева металла при термической обработке складывается из времени собственно нагрева до заданной температуры и времени выдержки при этой температуре. Время нагрева зависит от типа печи, размеров деталей, их укладки в печи; время выдержки зависит от скорости протекания фазовых превращений.
Нагрев может сопровождаться взаимодействием поверхности металла с газовой фазой и приводить к обезуглероживанию поверхностного слоя и образованию окалины. Обезуглероживание приводит к тому, что поверхность деталей становится менее прочной и теряет твердость.
При нагреве и охлаждении стали происходят фазовые превращения, которые характеризуются температурными критическими точками. Принято обозначать критические точки стали буквой А. Критические точки А1 лежат на линии PSK (727 °С) диаграммы железо-углерод и соответствуют превращению перлита в аустенит. Критические точки А2 находятся на линии МО (768 °С), характеризующей магнитное превращение феррита. A3 соответствует линиям GS и SE, на которых соответственно завершается превращение феррита и цементита в аустенит при нагреве.
Для обозначения критических точек при нагреве и охлаждении вводят дополнительные индексы: букву «с» в случае нагрева и «r» в случае охлаждения, например Ас1, Ac3, Ar1, Ar3.
Среди основных видов термической обработки следует отметить:
Отжиг
Отжиг 1 рода (гомогенизация, рекристаллизация, снятие напряжений). Целью является получение равновесной структуры. Такой отжиг не связан с превращениями в твердом состоянии (если они и происходят, то это — побочное явление).
Отжиг 2 рода связан с превращениями в твердом состоянии. К отжигу 2 рода относятся: полный отжиг, неполный отжиг, нормализация, изотермический отжиг, патентирование, сфероидизирующий отжиг.
Закалку проводят с повышенной скоростью охлаждения с целью получения неравновесных структур. Критическая скорость охлаждения, необходимая для закалки, зависит от химического состава сплава. Закалка может сопровождаться полиморфным превращением, при этом из исходной высокотемпературной фазы образуется новая неравновесная фаза (например, превращение аустенита в мартенсит при закалке стали). Существует также закалка без полиморфного превращения, в процессе которой фиксируется высокотемпературная метастабильная фаза (например, при закалке бериллиевой бронзы происходит фиксация альфа фазы, пересыщенной бериллием).
Отпуск необходим для снятия внутренних напряжений, а также для придания материалу требуемого комплекса механических и эксплуатационных свойств. В большинстве случаев материал становится болеепластичным при некотором уменьшении прочности.
Нормализация. Изделие нагревают до аустенитного состояния (на 30…50 градусов выше АС3) и охлаждают на спокойном воздухе
Дисперсионное твердение (старение). После проведения закалки (без полиморфного превращения) проводится нагрев на более низкую температуру с целью выделения частиц упрочняющей фазы. Иногда проводится ступенчатое старение при нескольких температурах с целью выделения нескольких видов упрочняющих частиц.
Криогенная обработка — это упрочняющая термическая обработка металлопродукции при криогенных, сверхнизких температурах (ниже минус 153°С).
Чугун
Чугу́н — сплав железа с углеродом (и другими элементами). Содержание углерода в чугуне не менее 2,14% (точка предельной растворимости углерода в аустените надиаграмме состояний): меньше — сталь. Углерод придаёт сплавам железа твёрдость, снижая пластичность и вязкость. Углерод в чугуне может содержаться в видецементита и графита. В зависимости от формы графита и количества цементита, выделяют белый, серый, ковкий и высокопрочные чугуны. Чугуны содержат постоянныепримеси (Si, Mn, S, P), а в некоторых случаях также легирующие элементы (Cr, Ni, V, Al и др.). Как правило, чугун хрупок.
Белый чугун
В них весь углерод находится в связанном виде (Fe3C). В зависимости от количества углерода делятся на:
– доэвтектические (2,14-4,3% углерода);
– эвтектические (4,3% углерода);
– заэвтектические (4,3-6,67% углерода).
Цементит в изломе – светлый, поэтому такие чугуны назвали светлыми.
Белые чугуны применяются в основном для изготовления ковких чугунов. Их получают путем отжига.
Серый чугун
Серый чугун – это сплав железа, кремния (от 1,2- 3,5 %) и углерода, содержащий также постоянные примеси Mn, P, S. В структуре таких чугунов большая часть или весь углерод находится в виде графитапластинчатой формы. Излом такого чугуна из-за наличия графита имеет серый цвет.
Ковкий чугун
Ковкий чугун получают длительным отжигом белого чугуна, в результате которого образуется графит хлопьевидной формы. Металлическая основа такого чугуна: феррит и реже перлит. Ковкий чугун получил свое название из-за повышенной пластичности и вязкости (хотя обработке давлением не подвергается). Ковкий чугун обладает повышенной прочностью при растяжении и высоким сопротивлением удару. Из ковкого чугуна изготавливают детали сложной формы: картеры заднего моста автомобилей, тормозные колодки, тройники, угольники и т. д.
Маркируется ковкий чугун двумя буквами и двумя числами, например КЧ 370-12. Буквы КЧ означают ковкий чугун, первое число—предел прочности (в МПа) на разрыв, второе число — относительное удлинение (в процентах), характеризующее пластичность чугуна.
Высокопрочный чугун
Высокопрочный чугун имеет в своей структуре шаровидный графит, который образуется в процессе кристаллизации. Шаровидный графит ослабляет металлическую основу не так сильно, как пластинчатый, и не является концентратором напряжений.
Половинчатый чугун
В половинчатом чугуне часть углерода (более 2,04%) содержится в виде эвтектического цементита — в структуре наряду с эвтектическим или первичным графитом присутствует ледебурит. Структурные составляющие такого чугуна — перлит, ледебурит и пластинчатый графит.
Источник
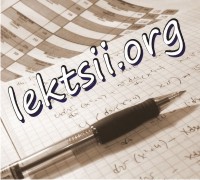
При разработке и создании различных изделий особое внимание уделяется технологическим свойствам материалов из которых изготавливаются эти изделия. Технологические свойства определяют пригодность материала для изготовления из него детали тем или иным способом. К числу этих свойств относятся:
– Обрабатываемость резанием — способность металла изменять свою форму под действием режущего инструмента (резца, фрезы, сверла и т. д.) при различных Операциях механической обработки (обтачивании, фрезеровании, сверлении).
– Ковкость— (деформируемость) — возможность менять форму изделия в горячем состоянии или при нормальной температуре под воздействием давления.
– Свариваемость—способность металлов образовывать прочные соединения при нагреве свариваемых частей до расплавленного или до пластичного состояния. Хорошей свариваемостью обладают стали с низким содержанием углерода. Плохо свариваются чугун, медные и алюминиевые сплавы.
– Жидкотекучесть – (литейность) — способность металла в расплавленном состоянии заполнять литейную форму, без оставления пустот. Металл должен обладать способностью давать отливки с резко очерченными контурами, т. е. иметь хорошую литейность. При недостаточной литейности форма заполняется не полностью и в тонких сечениях отливки образуются недоливы. Повышение температуры заливки улучшает жидкотекучесть сплавов.
Величину жидкотекучести определяют по технологической пробе, т. е. по длине спирального канала, заполненного металлом в контрольной форме. Чем больше жидкотекучесть сплава, тем большей длины участок спирали он заполнит до затвердевания.
– Усадка —сокращение объема расплавленного металла при его застывании и охлаждении до комнатной температуры по сравнению с размерами модели, по которой она была отформована. Соответствующее изменение линейных размеров, выраженное в процентах, называется линейной усадкой.
Величина усадки отливок зависит от химического состава сплава, конфигурации детали и других факторов. При большой усадке металла во время его кристаллизации и охлаждения возникают значительные внутренние напряжения и образуются усадочные раковины. Для удобства усадку отливок выражают в процентах по отношению к размерам модели и называется линейной усадкой..
– Ликвация — свойство сплавов образовывать при охлаждении и кристаллизации отливки с неоднородным химическим составом. Это объясняется тем, что сплав в форме охлаждается неравномерно. Чем больше разница в температуре внешних и внутренних частей отливки при ее охлаждении, тем больше компонентов, плавящихся при более низкой температуре, скапливается в середине сечения.
Различают два вида ликвации:
· Внутрикристаллическая ликвация характерна для фасонных отливок, изготовляемых из сплавов, образующих твердые растворы. В большинстве случаев скорость затвердевания отливки превышает скорость диффузии, которая необходима для выравнивания химического состава. Последнее является основной причиной развития внутрикристаллической ликвации в отливках.
· Зональная ликвация наблюдается в толстостенных отливках, слитках, которые медленно охлаждаются в формах. Зональная ликвация может происходить по двум основным причинам: в связи с расслоением жидкого сплава из-за различной плотности, которое происходит при недостаточном перемешивании сплава при плавке и заливке, или при выпадении из жидкого сплава легких и тяжелых кристаллизующихся фаз.
– Прокаливаемость — способность улучшения различных свойств металла путем закалки на различную глубину.
Все эти технологические свойства металлов и сплавов в комплексе и определяют дальнейшую сферу их применения.
Сталь наряду с бетонами — главнейший конструкционный материал. Широкому использованию сталь обязана высоким физико-механическим и технологическим свойствам. Одним из самых широко используемых технологических свойств стали является ее хорошая свариваемость. При нагреве сталь постепенно размягчается, а при температуре 1300—1400° С становится тестообразной. Если два куска стали, нагретых до тестообразного состояния, сложить вместе и сжать под прессом или молотом, то они соединятся в одно целое или, как говорят, сварятся
Другим свойством стали является ее хорошая прокаливаемость. Сталь, нагретая до температуры 750—900° (температура нагрева зависит от состава стали) и быстро охлажденная в воде или масле, становится более твердой и хрупкой. Процесс, сопровождающийся изменением структуры (т. е. строения) стали, называется закалкой.
Чем больше в стали содержание углерода, тем лучше она закаливается. Сталь с содержанием углерода до 0,15% не закаливается и, наоборот, лучше закаливается сталь с содержанием углерода более 0,5%. Отдельные элементы, входящие в состав стали, влияют на свойства ее следующим образом.
Углерод (С). С увеличением в стали содержания углерода увеличиваются ее твердость, прочность и закаливаемость, но понижаются ковкость и теплопроводность. Чем больше в стали углерода, тем медленнее ее надо нагревать. Сталь с содержанием углерода до 1,4% хорошо куется и прокатывается.
Кремний (Si) повышает прочность и упругость стали, но понижает вязкость и свариваемость. В стали машиностроительных сортов кремния обычно содержится от 0,2 до 0,4%’. Заметного влияния на ковкость кремний не оказывает.
Марганец (Мn). В обычных сортах углеродистых сталей марганца содержится от 0,2 до 1 %, а в специальных сортах до 14%. Марганец повышает сопротивляемость удару, прочность, уменьшает истирание, понижает вредное влияние серы. С увеличением содержания марганца понижается теплопроводность и свариваемость. Марганец способствует перегреву стали и появлению трещин. Чем больше в стали марганца, тем медленнее ее нужно греть; чтобы избежать перегрева и пережога марганцовой стали, необходимо тщательно следить за температурой нагрева и выдержкой при высоких температурах. Правильно нагретые заготовки или слитки из марганцовой стали куются хорошо.
Никель (Ni) увеличивает пластичность, вязкость и прочность стали. Никель не влияет на ковкость стали, но при нагреве никелевых сталей образуется окалина, которая прочно удерживается на поверхности заготовки. Окалина может заковываться в деталь и тем самым понижать ее механические качества.
Хром (Сr) повышает твердость, прочность и упругость стали, но понижает вязкость и теплопроводность. При ковке литого слитка структура хромистой стали плохо поддается разрушению. Для получения в поковке мелкозернистой структуры нужна большая проковка при высокой температуре. Хромистая сталь при температуре 1150—850° С куется удовлетворительно, а при низких температурах (ниже 850° С) твердость поверхности ее резко возрастает, отчего могут появляться трещины.
Молибден (Мо) добавляется в сталь вместе с никелем sr хромом. В сталях различных марок молибдена содержится до 0,45% и редко до 1%. В сплаве с хромом и никелем молибден повышает прочность и вязкость стали, но понижает теплопроводность. Чем больше в стали молибдена, тем медленнее ее надо греть, так как наличие молибдена сильно повышает чувствительность стали к перегреву. Молибденовые стали требуют интенсивной проковки на более мощных, прессах или молотах, чем прессы и молоты, на которых куются углеродистые стали. Охлаждать поковки из молибденовой стали нужно медленно, строго по-технологическому процессу, так как молибденовая сталь принимает воздушную закалку и предрасположена к образованию трещин.
Ванадий (V). В сталях, применяемых в машиностроении,, ванадия обычно содержится до 0,3% и редко до 1%. Ванадий повышает прочность и упругость стали, способствует образованию мелкозернистой структуры слитков. Содержание ванадия в стали улучшает ее ковкость и препятствует перегреву.
Вольфрам (W) повышает твердость и прочность стали, незначительно понижает вязкость и уменьшает теплопроводность. Ковка вольфрамовой стали при низких температурах вызывает трещины. Вольфрамовые стали нужно греть медленнее, чем углеродистые, а ковать при более высоких температурах.
Сера (S) — вредная примесь в стали, но в то же время является таким элементом, который переходит в сталь при ее плавке. Серы в стали должно быть как можно меньше. В сталях, применяемых, для изготовления особо ответственных деталей, содержание серы не должно превышать 0,02—0,03%, а в обычных сталях 0,045—0,055%. Повышенный процент серы в стали приводит к красноломкости. Если такую сталь нагреть до красного каления, то она становится хрупкой, во время ковки дает трещины и разрушения. При обычной температуре сера, содержащаяся в стали, понижает ее прочность.
Фосфор (Р). В отличие от серы фосфор сообщает стали холодноломкость, т. е. вызывает хрупкость при комнатной температуре. Фосфора в сталях, из которых изготовляются ответственные детали, не должно быть больше 0,03—0,04%. Чем больше сталь содержит углерода, тем больше может быть фосфора. Холодноломкость стали часто обнаруживается при правке и гибке изделий во время морозов в неотапливаемом помещении.
Дата добавления: 2016-12-31; просмотров: 2795 | Нарушение авторских прав | Изречения для студентов
Читайте также:
Рекомендуемый контект:
Поиск на сайте:
© 2015-2021 lektsii.org – Контакты – Последнее добавление
Источник