Какие свойства имеет резина по сравнению с каучуком
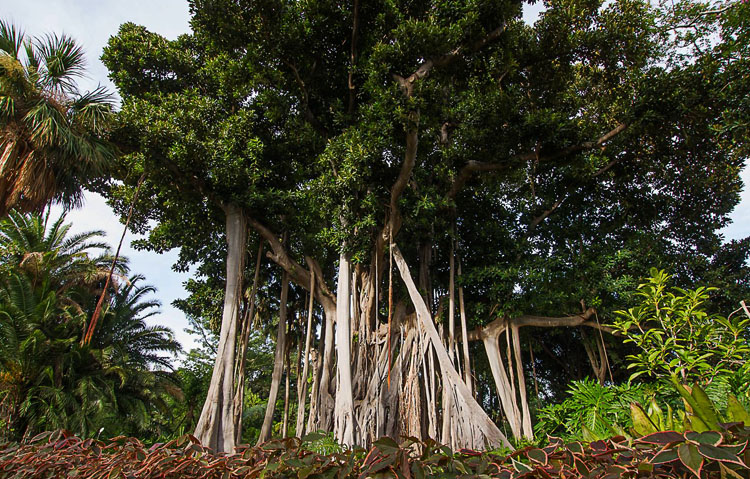
27 декабря 2018
Автор
КакПросто!
Резиновые изделия и те, что выполнены из каучука, нередко очень похожи: они имеют практически одинаковую плотность, текстуру, физические свойства. Однако сами материалы принципиально разнятся.
Содержание статьи
- Каучук
- Резина
Каучук начал применяться с 1823 года в качестве пропитки для плащей, которые изобрел К. Макинтош.
Сырье это бывает двух видов: натуральный и искусственный. Натуральный каучук получают из латекса каучуковых растений, которые растут в Латинской Америке, и к ним относятся следующие виды деревьев:
– гевея;
– фикусы каучуковые;
– разновидности ландольфии.
Искусственный каучук называют синтетическим. В его основе лежит синтез изопрена и бутиллития при помощи химического катализатора. При производстве синтетического каучука также используются производные нефти в качестве растворителя. Впервые он был получен в 1920 году, а в 1931 началось его серийное производство в промышленных масштабах. В настоящее время существуют следующие виды синтетических каучуков:
– бутадиен стирольный;
– полибутадиеновый;
– полизопреновый;
– бутилкаучук;
– этилен–пропиленовый;
– хлоропреновый;
– бутадиен – нитрильный.
Резина получается путем вулканизации каучука и добавлением различных химических элементов, которые призваны повысить прочность материала. Первая резина появилась в 1839 году путем вулканизации под воздействием на каучук серы, при котором на молекулярном уровне происходит укрепление сеточных структур.
При синтезе резины с применением синтетического каучука получается материал, который обладает повышенными качествами стойкости по отношению к агрессивным средам, таким как:
– жидкости с повышенным содержанием октана (бензин, керосин);
– продукты переработки нефти (различного рода масла).
Также у резины намного лучше характеристики по отношению к механическому воздействию на нее со стороны внешних факторов. Она имеет значительно более плотную структуру по отношению к каучуку, за счет чего она получила широкое распространение во всех отраслях народного хозяйства.
Резина в силу ее искусственного происхождения устойчива к различным атмосферным воздействиям. Кроме всего прочего она обладает диэлектрическими свойствами. Но главным отличием натурального и искусственного каучука от резины является повышенная пластичность каучуковой массы. Ее специально добавляют в резину при производстве, чтобы добавить гибкости, тягучести. Каучук в чистом виде почти не используется в виду его небольшой прочности, но зато при добавлении его в резину получается очень прочный, износостойкий материал.
Источник
В рецептуре покрытий применяются каучуки различной природы. Выбор того или иного каучука зависит от требований, предъявляемых к тканям с покрытиями.
Сравнительные свойства основных каучуков приведены в таблице2.11. В связи с тем что информация о свойствах изложена в многочисленных публикациях, книгах, на сайтах производителей и потребителей каучуков и вполне доступна, основное внимание при обсуждении свойств каучуков будет уделено некоторым их особенностям, определяющим их применение в рецептуре покрытий, а также недостаткам, которые необходимо учитывать.
Натуральный каучук.
[-СН2СН(СН3)=СН-СН2-]n
Натуральный каучук, состоящий на 90 % из цис-полиизопрена, был первым каучуком, применяемым для нанесения покрытий на ткани и изготовления конфекционных клеев. Основные достоинства натурального каучука, обеспечившие широкое его применение по сегодняшний день – хорошие прочностные свойства наполненных и ненаполненных резин на его основе, стойкость к истиранию, многократному изгибу, высокая эластичность, хорошая морозостойкость. Высоким прочностным показателям каучук обязан кристаллизации, она же создает некоторые проблемы при его переработке. Перед пуском в производство каучук подвергают декристаллизации при 50-80 оС в течение 24-70 ч, пластицируют в резиносмесителях, червячных машинах или на вальцах. После такой обработки процесс смешения натурального каучука с наполнителями, мягчителями и другими ингредиентами не представляет трудности. Вулканизация проводится серой в присутствии ускорителей вулканизации при температурах 143-151оС (при избыточном давлении пара 3-4 кгс/см 2). Прорезиненные ткани – мягкие, легко склеиваются клеем на основе натурального каучука. Натуральный каучук (светлый креп) разрешен к использованию в рецептурах пищевых и медицинских резин, поэтому применяется при изготовлении, например, прорезиненных тканей для резервуаров питьевой воды, тканей или изделий из них, контактирующих с кожей человека.
Благодаря высокой когезионной прочности натурального каучука клеи на его основе очень технологичны. Швы имеют высокую начальную прочность в невулканизованном состоянии, а если учесть высокую прочность швов после вулканизации (самовулканизации), то придется признать, что ни один из неполярных каучуков не может составить ему конкуренции.
Недостатки натурального каучука связаны с его непредельностью и неполярностью: малая устойчивость к старению, плохая атмосферостойкость, низкая маслобензостойкость. Сопротивление старению и атмосферостойкость можно улучшить правильным рецептуростроением.
Изопреновый каучук.
[-СН2С(СН3)=СН-СН2-]n
Синтетический цис-полиизопрен (СКИ-3) – аналог натурального каучука, но во многом ему уступает. Содержание 1,4-цис-звеньев у СКИ-3 составляет 93-98 % против 98-100 % у НК, доля 1,4-звеньев, присоединенных нерегулярно (“голова-голова”, “хвост-хвост”) составляет 2-4 и 0 % соответственно. НК содержит природные добавки, защищающие его в определенной мере от старения и отсутствующие в СКИ-3. СКИ-3 существенно уступает НК по степени кристаллизации и, следовательно, по когезионной прочности резиновых смесей. Тем не менее СКИ-3 нашел свое применение в тканях с покрытиями, но чаще в комбинации с другими каучуками, особенно, СКД.
Бутадиеновые каучуки.
(-CH2-CH=CH-CH2-)n
В России изготавливаются бутадиеновые каучуки двух основных типов – с преимущественным содержанием 1,2- и 1,4-звеньев. Внутри каждого из этих типов существуют различные марки каучуков.
Каучуки СКБ с 1,2-звеньями изготавливаются полимеризацией бутадиена в присутствии натриевого катализатора, поэтому называются натрий-бутадиеновыми. Благодаря отсутствию двойных связей в основной цепи они имеют хорошую стойкость к тепловому старению. Кроме того, они очень технологичны, хорошо смешиваются с ингредиентами, допускают получение высоконаполненных смесей без существенного ухудшения эластичности. Ткани с покрытиями на основе СКБ обладают мягкостью, высокой морозостойкостью, хорошей стойкостью к многократному изгибу. Основные недостатки каучука (низкая прочность, плохая стойкость к истиранию) связаны с низкой кристаллизацией, плохая маслобензостойкость – с химическим строением. С использованием СКБ-55, 60 выпускался большой ассортимент прорезиненных тканей и не для всех удалось найти альтернативную замену. Поэтому и сейчас Казанским заводом СК выпускаются каучуки марок СКБ-30, СКБ-40 и СКБ-50.
В 70-х годах была поставлена задача замены “морально устаревшего” каучука СКБ. Был синтезирован и запущен в серийное производство на Ефремовском заводе РТИ каучук СКД-СР различных марок с содержанием 1,2-звеньев от 40 до 70 %, в том числе маслонаполненный. Для прорезиненных тканей начал с успехом применяться каучук СКД-СР-М-10. В настоящее время его выпуск практически прекращен из-за малого спроса. При большом спросе на другие типы каучуков, в том числе поставляемых на экспорт, малотоннажное производство СКД-СР оказалось попросту экономически невыгодным.
Цис-1,4-полибутадиеновые каучуки (СКД) в рецептуре покрытий используется в комбинации с другими каучуками – полиизопреновым, бутадиенстирольным и др. Связано это, в первую очередь, с его неудовлетворительными технологическими свойствами – плохой перерабатываемостью, низкой когезионной прочностью и клейкостью. В смесях же с другими каучуками эти проблемы благополучно решаются и реализуются уникальные свойства СКД – высокая морозостойкость и износоустойчивость.
Бутадиенстирольные каучуки.
[-CH2-CH=CH-CH2-CH2-CH(C6H5)-]n
-CH2-CH=CH-CH2- C(CH3)(C6H5)-CH2-]n
Бутадиенстирольные каучуки получают сополимеризацией бутадиена со стиролом (СКС) или α-метилстиролом (СКМС). Каучуки выпускают с различным содержанием стирола. В производстве прорезиненных тканей используется преимущественно СКС-30АРКМ-15 и СКМС-30АРКМ-15 с содержанием стирола 30 % масс. и масла 15 % масс. Остальные буквенные обозначения расшифровываются так: А- “холодный (получение при 5 оС), Р- каучук содержит регулятор степени полимеризации, обеспечивающий заданную вязкость по Муни, К – в качестве эмульгатора использовались соли кислот диспропорционированной (гидрированной) канифоли. Маслонаполненные каучуки достаточно технологичны, доступны, недороги, поэтому широко применяются в производстве прорезиненных тканей. Стойкость к тепловому старению выше, чем у натурального каучука. Из-за некристаллизуемости каучуки обладают низкой когезионной прочностью, низкой прочностью вулканизатов (особенно ненаполненных). Как и другие неполярные каучуки они имеют плохую стойкость к маслам и углеводородным растворителям.
Этиленпропиленовые каучуки.
(-CH2-CH2)n-[CH2-CH(CH3)-]m (СКЭП)
Этиленпропиленовые каучуки получают сополимеризацией этилена и пропилена (СКЭП) или этилена, пропилена и диена (СКЭПТ). В качестве третьего мономера обычно используется дициклопентадиен, реже – 2-этилиден-5-нонборнен и гексадиен-1,4-метилтетраинден. Чаще в рецептурах покрытий тканей используются тройные сополимеры, для которых возможна серная вулканизация, с содержанием пропилена 30 (СКЭПТ-30) или 40 % (СКЭПТ-40).
Из-за очень малого содержания двойных связей этиленпропилендиеновые каучуки обладают исключительно высокой стойкостью к тепловому и атмосферному старению, воздействию окислителей, озона, растворов кислот, щелочей и других агрессивных сред. Они имеют низкую удельную плотность и высокую морозостойкость. Как и другим неполярным каучукам, СКЭПТ свойственна низкая стойкость к углеводородным растворителям. При оценке свойств каучука в качестве основного компонента покрытия тканей следует особо отметить низкую адгезию и низкую скорость вулканизации. Этим свойствам, как и основным своим преимуществам, каучук обязан малому содержанию двойных связей. Для повышения адгезии используются смолы и различные модификаторы адгезии. Отрицательное влияние низкой скорости вулканизации проявляется при использовании полиэфирных тканей в качестве подложки. Для увеличения скорости вулканизации СКЭПТ в резиновую смесь вводят ускорители, содержащие аминные группы или образующие их в процессе вулканизации. Именно они в результате конкурентной реакции аминолиза эфирных связей вызывают разрыв макромолекул полиэтилентерефталата и существенное падение прочности тканей. На практике нами отмечалось снижение прочности прорезиненных тканей после вулканизации до 50 %, в литературе же сообщается о ее снижении на 80 % [ 58 ]. Степень такого вредного воздействия напрямую зависит от аминного числа ускорителя (доля азота аминного типа) и его содержания. Следует отметить, что падение прочности может происходить не только при вулканизации, но и в процессе теплового старения материала. В таблице 2.12 приводятся расчетные амино-азотные индексы некоторых ускорителей, показывающие количество азота, который реально может быть переведен в амины в ходе вулканизации, в расчете на грамм ускорителя:
Общий индекс вулканизующей системы равен сумме индексов компонентов, помноженных на из массовую долю. Исследования показали, что при температуре 160 оС в течение 2 часов прочность полиэфирного корда уменьшается на 60 % при использовании ускорителей с общим индексом 10-15, на 80 % – при индексах от 25 и выше.
Подробное изучение поведения полиэфирного корда в контакте с резинами на основе этиленпропилендиенового каучука привело авторов к выводу, что на потерю прочности влияют три основных фактора – наличие влаги, природы вулканизующей системы и условий вулканизации и теплового старения. Разрушение полиэфирного корда вызвано гидролизом, катализируемым аминами. С повышением температуры разрушение ускоряется. Наиболее эффективный метод устранения падения прочности – отказ от ускорителей вулканизации аминного типа. Это всегда необходимо учитывать при разработке полиэфирных тканей с резиновыми покрытиями на основе СКЭПТ.
При применении полиамидных, вискозных и т.д. тканей таких проблем не замечено.
“Ткани с эластомерным покрытием для мягких оболочечных конструкций”
Авторский коллектив; Л.Е. Ветрова, к.х.н В.Ф. Ионова, П.В. Таскаева, к.т.н. А.Т. Титаренко, к.т.н. В.П. Шпаков
Под общей редакцией к.т.н. В.П. Шпакова
Источник
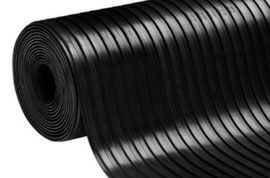
Эластичные материалы знакомы человеку с давних времен. Они тогда применялись преимущественно в бытовых целях. Сегодня без резины и каучука трудно представить развитие промышленности, транспорта и строительства и связи, повседневную жизнь людей.
Что появилось раньше
Еще до того, как Америку открыли европейцы, индейцы, жившие там, пользовались каучуком. Его получали из сока тропической гевеи. Высушенный сок коптили, получая непромокаемый и упругий материал. Он шел на изготовление емкостей для воды, игрушек, предметов культа. Из него делали примитивную обувь и одежду.
В середине XVIII века каучук путешественники привезли в Европу. Однако долго не могли найти способ его применения. За исключением стирающих карандаш ластиков. Считалось, что из-за его высыхания и затвердевания он не имеет перспектив практического применения. В следующем веке появились непромокаемые ткани, сумки и галоши, которые твердели в холодную погоду и становились мягкими в тепле.
Через сотню лет после появления каучука в Старом Свете был придуман способ, позволивший сделать эластичность этого материала устойчивой. Он получил название вулканизации. Его суть в смешивании сырого каучука с серой и дальнейшим разогревом этой смеси. Получившийся продукт стали называть резиной. Она начала широко использоваться в качестве уплотнителя и электроизолятора. В начале ХХ века в связи с ростом потребности в резине была решена проблема производства синтетических каучуков в промышленно развитых странах.
Куда идет латекс
Натуральный каучук добывают из каучуконосных деревьев, которые растут в тропических лесах или на специальных плантациях. Такое дерево начинает давать сок через семь лет. Для этого на нем ножом делается спиралевидное углубление, по которому в емкость попадает вытекающий сок белого цвета, называемый латексом. Спустя несколько часов набирается примерно полторы сотни граммов. После загустевания и высыхания образуются комочки натурального каучука. Такую процедуру можно проводить раз в два дня.
Каучуковое дерево
Всего в мире натуральный каучук достигает 40% в общем производстве и потреблении всех видов каучуков. Это примерно 9 млн. тонн.
Необработанный каучук растворяется в бензине, образуя каучуковый клей, и других органических растворителях. После вулканизации он только набухает, а не растворяется.
Кроме бензина он растворяется в бензоле, хлороформе, сероуглероде и других углеводородах. Он практически не растворяется и не набухает в спирте, воде и ацетоне.
Свыше половины натурального каучука идет на производство автошин. В странах Юго-Восточной Азии (Вьетнам, Индонезия, Малайзия и Таиланд) организовано крупномасштабное его производство.
Как делают резину
Оба эластичных материала неразрывно связаны. Резину получают из натурального или синтетического каучука в результате вулканизации. Добавляется наполнитель, которым чаще всего является сажа. Нагретый до 130-160 градусов каучук начинает взаимодействовать с серой. Во время этого технологического процесса молекулы каучука сшиваются в единую сетку с помощью атомов серы. Это резко повышает его эластичность и твердость, прочностные качества. Регулируется набухаемость и растворимость органическими растворителями.
Резина
Помимо серы для вулканизации применяются оксиды металлов, соединения аминного типа, убыстряющие процесс катализаторы, и другие химические компоненты. Они обеспечивают нужную пластичность, свойства против старения и другие эксплуатационные качества. В результате каучук превращается в резину. В зависимости от содержания серы образуется материал разной степени упругости. Самой мягкой получается резина с минимальным содержанием серы, а самой твердой та, в которой она составляет треть и более.
Производство резины
При изготовлении резины ей задаются определенные качества для производства изделий из нее:
- Кислотостойкость.
- устойчивость в агрессивных средах.
- Маслобензостойкость.
- устойчивость против высоких и низких температур.
- Озоностойкость.
- Электропроводимость и пр.
Резина широко применяется для изготовления шин для транспортных средств, различных шлангов и уплотнителей, лент транспортеров, бытовых, гигиенических и медицинских товаров.
В чем сходство и разница
Резина и каучук схожи, прежде всего, своей эластичностью и тем, что они могут перерабатываться. Их отличия существеннее.
Сырой каучук:
- Не пригоден для промышленного производства. В мире применяют не более 1% добываемого натурального каучука. В основном в виде резинового клея.
- У него низкая прочность, и высокая липучесть, которая сильно проявляется при высокой температуре. На морозе он твердеет и ломается. Полезные качества он приобретает только после вулканизации.
- При комнатной температуре начинается его старение, следствием которого становится потеря прочности и эластичности.
- Когда температура поднимается до 200 градусов, он разлагается с образованием низкомолекулярных углеводородов.
- Растворяется органическими растворителями типа бензина.
- Служит сырьем для производства резины.
Резина, полученная в результате вулканизации каучуков, служит для массового производства многих тысяч наименований различных изделий.
Из нее изготавливают:
- Шины для транспортных средств и авиационной техники.
- Разнообразные уплотнители, применяемые в промышленности и строительстве, различных видах техники.
- Электроизоляционные материалы.
- Приводные ремни, рукава для подачи жидкостей.
- Напольные покрытия и изолирующие пластины.
- Резиновую обувь и водоустойчивую одежду.
- Средства защиты от химического, радиационного и бактериологического воздействия (костюмы, перчатки, сапоги и пр.).
- Изделия медицинской техники и гигиены.
- Фурнитуру для одежды и пр.
Источник