Какие продукты разделения воздуха
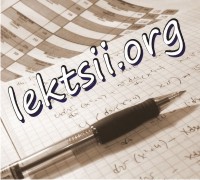
Разделение воздуха является основным промышленным методом получения технических газов, таких как кислород, азот, аргон, а также редких газов, таких как криптон, ксенон, неон, гелий.
Разделение воздуха является основным промышленным методом получения технических газов, таких как кислород, азот, аргон, а также редких газов, таких как криптон, ксенон, неон, гелий.
Воздухоразделение используется в установках криогенного, адсорбционного, мембранного типа.
Криогенное воздухоразделение функционирует при низкотемпературном режиме ректификации.
Адсорбционное воздухоразделение происходит посредством связывания твердым веществом, называемым адсорбентом, отдельных компонентов газовой смеси.
Это явление обусловлено силами взаимодействия молекул газа и адсорбента.
Короткоцикловая адсорбция наиболее предпочтительна в случаях, когда потребность в производственных объемах азота велика и степень чистоты имеет средние показатели.
Технология адсорбции основана на поглощении молекулярными ситами определенных веществ, за счет этого обеспечивается разделение воздушной смеси.
Регулирование процесса поглощения газов и регенерации адсорбента происходит путем изменения давления и/или температуры.
Адсорбционная технология позволяет эффективно получать из атмосферного воздуха такие газы как азот и кислород.
Мембранное воздухоразделение основано на проникновении воздушных компонентов через газоразделительные мембраны из-за разных скоростей проникновения.
Движущей силой разделения газов является разница парциальных давлений на различных сторонах мембраны.
Мембранные установки производят азот чистотой до 99,5% и достаточно экономичны при средних объемах потребления.
Современная газоразделительная мембрана представляет собой уже не плоскую пластину или плёнку, а полое волокно.
Половолоконная мембрана состоит из пористого полимерного волокна с нанесённым на его внешнюю поверхность газоразделительным слоем.
Пористое волокно имеет сложную асимметричную структуру, плотность полимера возрастает по мере приближения к внешней поверхности волокна.
Толщина газоразделительного слоя волокна не превышает 0,1 мкм, что обеспечивает высокую удельную проницаемость газов через полимерную мембрану.
Существующий уровень развития технологии позволяет производить полимеры, которые обладают высокой селективностью при разделении различных газов, что, соответственно, обеспечивает высокую чистоту газообразных продуктов.
Современный мембранный модуль, используемый для технологии мембранного разделения газов, состоит из сменного мембранного картриджа и корпуса.
Из-за разницы парциальных давлений на внешней и внутренней поверхностях половолоконной мембраны происходит разделение газовой смеси на компоненты. Газы, быстро проникающие через полимерную мембрану (например, H2, CO2, O2, пары воды, высшие углеводороды), поступают внутрь волокон и выходят из мембранного картриджа через один из выходных патрубков. Газы, медленно проникающие через мембрану (например, CO, N2, CH4), выходят из мембранного модуля через второй выходной патрубок.
Конструктивно половолоконная мембрана компонуется в виде цилиндрического картриджа, который представляет собой катушку с намотанным на неё особым образом полимерным волокном.
Газовый поток под давлением подаётся в пучок мембранных волокон.
Из-за различных парциальных давлений на внешней и внутренней поверхностях мембраны происходит разделение газового потока.
В газоразделительных блоках полностью отсутствуют движущиеся части, что обеспечивает надёжность установок. ембраны очень устойчивы к вибрациям и ударам, химически инертны к воздействию масел и нечувствительны к влаге, функционируют в широком диапазоне температур от −40 °C до +60 °C.
При соблюдении условий эксплуатации ресурс мембранного блока составляет от 130 000 до 180 000 часов (15-20 лет непрерывной работы).
Недостатки мембранных установок являются ограниченная производительность и относительно низкая чистота получаемых продуктов по сравнению с газами, полученными с помощью метода адсорбции или криогенным способом.
Чем нужно руководствоваться при выборе установки.
1. Какие продукты разделения воздуха, и в каком виде вам необходимо получать.
– На криогенных установках возможно одновременное получение азота, кислорода, (на крупных установках так же и аргона) как в газообразном, так и жидком виде.
– На адсорбционных и мембранных установках возможно получение только одного продукта, азота или кислорода, и только в газообразном виде.
2. Чистота получаемых продуктов разделения воздуха, необходимая для обеспечения технологических процессов вашего производства.
Технический и медицинский газообразный кислород по ГОСТ 5583-78 и ГОСТ 6331-78 (чистота не ниже 99,2%) , как и жидкий возможно получить только криогенным способом.
Адсорбционные установки дают чистоту не выше 95%, мембранные – до 50%.
(Для газовой сварки и резки металлов применяется кислород чистотой не ниже 98,5 %, получаемый только на криогенных установках.)
Азот повышенной чистоты (99,999) возможно получить как на криогенных, так и на адсорбционных установках.
3. Производительность установки.
4. Энергопотребление. Основной характеристикой при определении затрат на производство технических газов, является удельный расход электроэнергии на м3 (или кг) производимого продукта.
5. Давление продуктов разделения воздуха на выходе установки.
6. Условия эксплуатации. Количество обслуживающего персонала, ремонтопригодность оборудования, стоимость и возможность получения запасных частей.
Источник
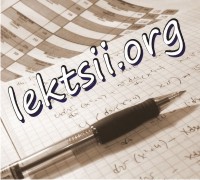
Общие сведения
Состав воздуха, продукты его разделения и их использование
Состав атмосферного воздуха не постоянен. Содержание компонентов зависит от географической широты, высоты над поверхностью, солнечной активности и других факторов. Существенно неодинакова загрязненность воздушного бассейна, где содержание примесей может меняться в течение суток, например, под влиянием метеорологических условий.
Усредненный состав сухого атмосферного воздуха у поверхности земли приведен в табл. 1.1.
Таблица 1.1. Усредненный состав атмосферного воздуха
Газ | Молекулярная масса | Объемное содержание в воздухе, % | Массовое содержание, % | Нормальная температура кипения, К |
Азот N2 | 28,016 | 78,09 | 75,52 | 77,36 |
Кислород O2 | 32,00 | 20,95 | 23,15 | 90,19 |
Аргон Ar | 39,944 | 0,93 | 1,28 | 87,29 |
Диоксид углерода CO2 | 44.01 | 0,03 | 0,05 | 194,6 |
Неон Ne | 20,183 | 1,8×10-3 | 1,25×10-3 | 27,0 |
Гелий He | 4,003 | 5,24×10-4 | 0,72×10-4 | 4,22 |
Криптон Kr | 83,8 | 1×14-4 | 3,3×10-4 | 119,0 |
Водород H2 | 2,016 | 5×10-5 | 0,035×10-4 | 20,4 |
Закись азота N2O | 44,016 | 5×10-5 | 8×10-5 | 184,60 |
Ксенон Xe | 131,3 | 8×10-5 | 3,6×10-5 | 165,0 |
Озон O3 | 48,00 | 1×10-6 | 1,5×10-6 | 161,25 |
Радон Rn | 6×10-18 | 4,5×10-17 | 211,35 |
Кроме того, в зависимости от производственной деятельности в регионе, в воздухе содержится незначительное количество метана, ацетилена и других высокомолекулярных углеводородов.
Содержание в воздухе водяных паров зависит от температуры и относительной влажности j. Значение относительной влажности обычно усредняется для определенного региона. Для средней полосы России j=0,7-0,8.
В табл. 1.2. приведено насыщающее влагосодержание воздуха в зависимости от его температуры при нормальном атмосферном давлении.
При сжатии воздуха содержание влаги в нем при полном насыщении уменьшается.
Таблица 1.2. Насыщающее влагосодержание воздуха в зависимости от температуры при атмосферном давлении
Температура воздуха, °С | Влагосодержание, г/кг | Температура воздуха, °С | Влагосодержание, г/кг | Температура воздуха, °С | Влагосодержание, г/кг | Температура воздуха, °С | Влагосодержание, г/кг |
25,40 | 3,73 | -30 | 0,229 | -60 | 0,00695 | ||
19,07 | -5 | 1,7 | -35 | 0,133 | -65 | 0,00286 | |
14,17 | -10 | 1,59 | -40 | 0,077 | -70 | 0,00163 | |
10,35 | -15 | 1,01 | -45 | 0,043 | -75 | 0,00073 | |
7,48 | -20 | 0,63 | -50 | 0,024 | -80 | 0,00032 | |
5,313 | -25 | 0,39 | -55 | 0,013 | -90 | 0,000082 |
Основными продуктами разделения предварительно осушенного воздуха в современных воздухоразделительных установках (ВРУ) являются следующие так называемые промышленные газы:
кислород технический – 99,2-99,7 % (1-й сорт – 99,7; 2-й сорт – 99,5; 3-й сорт – 99,2 %) и технологический – 92-98 % (в среднем – 95 %, остальное азот);
азот особой чистоты – не менее 99,996 %, высшего сорта – 99,994; 1-го сорта – 99,5; 2-го сорта – 99 и 3-го сорта – 97 %;
аргон высшего сорта – 99,993 и 1-го сорта – 99,987 %; сырой аргон – 86-90 %, содержащий до 4 % О2 и до 10 % N2; технический – 86-87 % с примесью 12-14 % азота;
первичный криптоноксеноновый концентрат с объемной долей криптона и ксенона до 0,2 %;
неоногелиевая смесь с объемной долей неона и гелия от 40 % и выше.
В дальнейшем сырой аргон и криптоноксеноновый концентрат подвергаются очистке и дополнительной ректификации.
Применение основных продуктов разделения воздуха – кислорода и азота, является одним из важных направлений технического прогресса в ряде отраслей промышленного производства. Это черная и цветная металлургия, химическая, нефтехимическая и пищевая промышленность, энергетика, медицина, машиностроение и пр. Использование этих продуктов позволяет интенсифицировать технологические процессы в этих отраслях. Это способствует увеличению выработки продукции, улучшению ее качества, снижению себестоимости.
По данным США использование кислорода в различных отраслях промышленности распределяется приблизительно следующим образом (в % от общего производства кислорода):
черная и цветная металлургия 60;
химическая промышленность 25;
ракетная техника и энергетика 10;
нефтепереработка 3;
прочие отрасли 2 %.
В течение последних 25 лет ежегодный прирост производства кислорода составляет 12-15 %.
Примерные удельные расходы кислорода на единицу продукции составляют:
в доменном производстве – 100-150 м3 на 1 т чугуна;
при конверторной выплавке стали – 55-60 м3/т кислорода 1-го и 2-го сорта;
в электроплавильном производстве – 15-20 м3/т, кислорода того же качества;
в производстве азотной кислоты – 155 м3/т, кислорода 1-3 сортов.
При аэрации и осветлении сточных вод воздухом, обогащенным кислородом, в зависимости от степени их загрязнения расходуется от 2 до 24 м3/м3.
С каждым годом все большее применение находит азот. В химической промышленности на производство аммиака, этилена, пропилена, азотных удобрений расходуется до 1000 м3 азота на каждую тонну продукта.
Особое развитие нашла так называемая “азотная технология”. Она стремительно расширяет области своего внедрения:
в машиностроении, например, это азотирование поверхностей деталей, что обеспечивает повышение прочности и износостойкости. Закалка инструмента в жидком азоте повышает его стойкость до 90 раз. Значительно надежнее и прочнее становятся неразъемные соединения, полученные с помощью жидкого азота, например, запрессовка бандажей, втулок и пр.;
в пищевой промышленности – азот наилучший охладитель и консервант продуктов питания;
в легкой промышленности – обработка кож, различного сырья. Замораживание жидким азотом тканей позволяет роботизировать и автоматизировать процессы раскроя и пошива одежды;
в медицине – безболезненные и быстрые операции на коже, глазах. Консервация органов пересадки, крови и др.
Жидкий азот является важнейшим хладоносителем для предварительного охлаждения газов в криогенных установках. С его помощью получают жидкий водород, гелий и др. редкие газы. На него возлагают большие надежды энергетики – разработчики высокотемпературной сверхпроводимости.
Аргон применяют как защитную среду для расплавленных металлов от окисления при плавке, разливе и электросварке нержавеющих сталей, титана, магния, алюминия. При плазменно-дуговой резке легированных сталей, сплавов алюминия, меди. При получении чистых металлов – титана, циркония, ниобия, молибдена и др.
Широко используется аргон в электроламповой промышленности для заполнения ламп накаливания и газоразрядных ламп. Лампы накаливания с аргоном имеют повышенные срок службы и светоотдачу. Аргон препятствует диффузии вольфрама, помутнению колб, уменьшают тепловые потери, так как позволяют повысить температуру нити накаливания.
В полупроводниковой промышленности аргон используется как защитная среда при производстве монокристаллов титана, бария, кремния и др. полупроводниковых материалов.
Сжижаются не только воздух и его компоненты. На практике широко применяются многие газы в сжиженном и твердом виде, например, CO2, CH4, H2, F2, и др. Некоторые из них применяются как хладагенты, другие как горючее и окислители. В ряде случаев сжижение ведется с целью перевоза и хранения.
Процессы сжижения газов довольно энергоемки. Например: для получения 1 т сухого льда (СО2) затрачивается 125-150 кВт×ч электроэнергии;
1 т жидкого кислорода (О2) – 1200-1500 кВт×ч;
1т жидкого водорода (Н2) – 60000-80000 кВт×ч.
Эксергетический КПД процессов сжижения, реализуемых в технических установках не превышает 20-25 %, а часто 10-15 %.
Дата добавления: 2016-03-28; просмотров: 1988 | Нарушение авторских прав | Изречения для студентов
Читайте также:
Рекомендуемый контект:
Поиск на сайте:
© 2015-2020 lektsii.org – Контакты – Последнее добавление
Источник
Текущая версия страницы пока не проверялась опытными участниками и может значительно отличаться от версии, проверенной 25 февраля 2019; проверки требуют 2 правки.
Воздухоразделительные установки (ВРУ) — установки для разделения воздуха на компоненты, а именно на: кислород, азот, аргон, неон, ксенон, криптон. Газовый состав воздуха на земле одинаков, за исключением углекислого газа, углеводородов и аммиака, концентрация которых на несколько (3 и более) порядков меньше, чем содержание кислорода и азота.
Воздухоразделительные установки подразделяются по давлению цикла разделения: P = 15 ÷ 20 МПа — высокое давление, P = 4 ÷ 7 МПа — среднее давление, P = 0,5 ÷ 1,2 МПа — низкое давление.
История[править | править код]
Исторически существовали несколько способов разделения воздуха.
- Фракционная конденсация паров воздуха
- Фракционное испарение жидкого воздуха
- Ректификационный
- Адсорбционный
- Мембранный
Первоначалом для существующих ВРУ, были ожижители воздуха. Первые ожижители представляли собой четырёхкаскадную систему охлаждения, с несколькими контурами охлаждения на базе аммиака, борного спирта и некоторых фракций природного газа (пропан, бутан, этан).
Первым, кто получил кислород из воздуха путём ректификации был Карл Линде в 1895 году. Он создал криогенный цикл, по которому работала установка разделения, в последующем её назвали установка Линде, а цикл разделения воздуха — цикл Линде. В данном цикле применялся изотермический дроссель эффект, который создавался за счет изотермического сжатия в компрессоре и последующего расширения через дроссельный вентиль. Установка работала по циклу высокого давления P = 10 ÷ 15 МПа, с производительностью Vк = 100 (м³ O2)/час и концентрацией xк = 99,5 ÷ 99,7 % O2. Линде впервые создал аммиачную холодильную машину, которую в последующем включил в цикл разделения воздуха (в 1902 год).
Установку низкого давления изобрел советский ученый П. Л. Капица в 1939 году. Установка была предназначена для получения газообразного кислорода и работала по циклу низкого давления P = 0,6 ÷ 0,7 МПа
снижение давления было достигнуто путём применения в цикле турбодетандера, а также увеличением на порядок по сравнением с циклом Линде (от 3000 м³ воздуха в час и выше) потребляемого воздуха.
Принцип работы и устройство[править | править код]
Устройство[править | править код]
ВРУ состоит из 2-х секций. Ожижительной и разделительной. Ожижительная секция предназначена для получения жидкого воздуха, вернее, жидкой флегмы, в которой массовая доля кислорода чуть выше, чем в воздухе, за счет более высокой температуры кипения, как следствие при испарении в парах над флегмой больше низкокипящих компонентов, таких как азот.
Ожижительная секция состоит из блока комплексной очистки и осушки (БКОО), компрессора, ряда теплообменников, расширителя, в роли которого выступает дроссель или детандер, и оканчивается резервуаром для скопления сжиженной флегмы. Чаще всего, резервуаром для флегмы является дно ректификационной колонны.
Как правило, в системе стоит от 2-х и более теплообменников. Первый теплообменник работает при положительных температурах, и предназначен для охлаждения сжатого компрессором воздуха, окружающим воздухом. Последующие теплообменники охлаждают сжатый воздух путём теплообмена с исходящими продуктами: кислородом, азотом или флегмой.
Разделительная секция чаще всего состоит из ректификационной колонны, конденсатора-испарителя и ряда азото-кислородных теплообменников. Количество ректификационных колонн зависит от того какой газ или жидкость получается в установке. Так при получении только газообразного азота в установке находится 1 колонна. При получении кислорода в установке будет находится: верхняя и нижняя колонны и конденсатор испаритель между ними . При получении аргона в установке будет находиться 4 колонны: нижняя, верхняя, сырого аргона, чистого аргона. Остальные газы (ксенон, криптон, неон) находящиеся в воздухе получают в крупных ВРУ в виде смесей, из которых далее, в специальном оборудовании, выделяют эти газы в чистом виде. Неон и гелий при работе ВРУ накапливаются в конденсаторе-испарителе в виде некондесируемой фракции и начинают мешать процессам конденсации азота, для их удаления предусмотрен вентиль стравливания.
Принцип работы[править | править код]
Воздух, прошедший ряд фильтров механической фильтрации, попадает в компрессор, где сжимается до давления цикла, далее воздух поступает в БКОО, где с помощью абсорбентов из него удаляются влага, двуокись углерода и углеводороды, после чего воздух попадает в теплообменники. После них он попадает в нижнюю ректификационную колонну, где ректифицирует на кубовую жидкость (~ 35 % O2, 2 % Ar, остальное — азот) и газообразный азот с чистотой ~99,99 %.
Если установка получает помимо азота ещё и кислород, то кубовая жидкость подается в середину верхней ректификационной колонны, а жидкий азот в верх верхней ректификационной колонны. Из верха верхней ректификационной колонны отбирается газообразный азот, внизу собирается жидкий кислород. Жидкий кислород попадает в конденсатор-испаритель, который производит теплообмен с газообразным азотом нижней ректификационной колонны. Со временем в конденсаторе-испарителе накапливается неон и гелий, что предусматривает установку вентиля для стравливания этих газов.
Классификация ВРУ[править | править код]
Существуют три метода разделения воздуха: адсорбционный, мембранный и криогенный. Отсюда и типы установок: адсорбционные, мембранные и криогенные.
Криогенные ВРУ[править | править код]
подразделяются[1]:
- по давлению цикла разделения: P = 15 ÷ 20 МПа — высокое давление, P = 4 ÷ 7 МПа — среднее давление, P = 0,5 ÷ 1,2 МПа — низкое давление. Основано на классификации компрессоров по давлению нагнетания. Тем же образом классифицируют адсорбционные и мембранные установки разделения воздуха.
- по производительности:
- малой Vк = 30 ÷ 300 (м³ N2 или O2)/час при нормальных условиях (T0 = 273 K, P0 = 760 мм рт.ст. = 101325 Па = 1 атм);
- средней Vк = 300 ÷ 3000 (м³ N2 или O2)/час при нормальных условиях;
- высокой Vк > 3000 (м³ N2 или O2)/час при нормальных условиях;
- по состоянию получаемого продукта:
- Для получения газообразных продуктов;
- Для получения жидких продуктов;
- Для одновременного получения продуктов в жидкой и газообразной фазах;
Существуют малые ВРУ в которых в качестве ожижительной части используется газовая криогенная машина, работающей по обратному циклу Стирлинга. Рабочим газом в такой машине в большинстве случаев является гелий.
Расшифровка названия:[1]
После тире в названии ВРУ указывается её производительность по первому продукту в тыс.м³/ч или тыс.кг/ч если речь идет о жидких продуктах.
- А — получение газообразного азота
- Кд — получение газообразного кислорода
- Аж — получение жидкого азота
- Кж — получение жидкого кислорода
- Ар — получение газообразного аргона
- Кт — получение технологического (чистота 95 %) кислорода
Пример: установка АжКж-0,6 получает жидкий азот в количестве 0,6 тыс.кг/ч, а также жидкий кислород.
Установка КА-5 производит газообразный кислород в количестве 5 000 м³/ч, а также газообразный азот.
См. также[править | править код]
- Криогеника
Литература[править | править код]
- Справочник Кислород том 1 и том 2, в 2 томах, под ред Глизманенко Д. Л., М: «Металлургия», 1967 г.
- Установки, машины и аппараты криогенной техники часть 1 и 2, в 2 частях, Усюкин И. П., М.: Пищевая промышленность, 1976 г.
Примечания[править | править код]
- ↑ 1 2 Установки, машины и аппараты криогенной техники, Усюкин И. П., М.: Пищевая промышленность, 1976
Ссылки[править | править код]
- История Института кислородного машиностроения
Источник