Какие химические соединения придают гидравлическим вяжущим гидравлические свойства
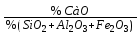
Гидравлические вяжущие вещества – более сложные по составу, чем воздушные, вещества. После смешивания с водой способны схватываться, твердеть, сохранять и повышать свою прочность не только на воздухе, но и в воде. не содержат сложные минералы, образующиеся при обжиге карбонатных пород или искусственных смесей : силикаты, алюминаты, ферриты кальция.
К гидравлическим веществам относятся:
· гидравлическая известь;
· портландцемент и его разновидности;
· специальные цементы.
В отдельную группу выделяют вяжущие вещества автоклавного твердения, быстро набирающие прочность только в автоклаве в среде насыщенного водяного пара при температуре 175-200°С и давлении 0,8-1, 5 МПа. К ним относятся романцемент, глиноземистый и расширяющиеся цементы, гипсоцементно-пуццолановые, известково-кремнеземистые и известково-шлаковые вяжущие, нефелиновый цемент, хотя по существу эти вяжущие являются гидравлическими.
Число разновидностей гидравлических вяжущих постоянно растет благодаря использованию новых видов сырья и применения современных способов производства.
Сырьем для производства минеральных вяжущих являются различные горные породы, главным образом осадочного происхождения, и некоторые массовые побочные продукты металлургической, энергетической, химической и других отраслей промышленности. В больших объемах используются:
Ø карбонатные (известняк, мел, доломит, мергель, магнезит);
Ø сульфатные (гипс, ангидрит);
Ø кремнеземистые (диатомит, трепел, опока);
Ø глинистые и высокоглиноземистые (бокситы) горные породы;
Ø промышленные отходы (доменные и другие металлургические шлаки, шлаки и зола от пылевидного сжигания твердого топлива, нефелинового шлама). При этом отпадает необходимость организации карьеров по добыче природного сырья, сокращаются расходы топлива и электроэнергии на обжиг и помол, что в целом способствует охране природы и среды обитания человека.
Технологический процесс производства вяжущих состоит из следующих циклов – измельчение сырья до частиц примерно одного размера, тщательное смешение смеси для получения однородной композиции, обжиг сырья при высоких температурах(в результате физико-химических процессов в период обжига образуются новые соединения, способные взаимодействовать с водой и при этом твердеть, превращаясь в искусственный камень). Причём каждое вяжущее требует определенной температуры и продолжительности термической обработки. Высококачественные вяжущие(портландцемент и глиноземный цемент) получают обжигом при высоких температурах до частичного плавления(спекания) сырьевой смеси. Чаще всего продукты обжига еще не являются готовым вяжущим.
Для проявления вяжущих свойств их подвергают тонкому измельчению (помолу) в чистом виде или чаще совместно с добавками, вводимыми с целью регулирования технологических свойств теста вяжущего и эксплуатационных свойств искусственного камня, а также облегчения помола и удешевления. Чем выше тонкость помола, тем быстрее и полнее пройдут процессы химического взаимодействия вяжущего с водой.
Минеральные вяжущие обычно приводят в рабочее состояние путем смешивания с водой (затворения). Иногда (например, в случае с магнезиальными вяжущими) затворение производят водными растворами солей. Переход теста в искусственный камень происходит в результате затвердевания – сложных процессов, сопровождающих химическое взаимодействие вяжущего с водой с выделением теплоты (экзотермический процесс).
Применение – в сухих и влажных условиях, где требуется высокая прочность и там, где нельзя применять воздушные вяжущие вещества. Их используют в кладочных и штукатурных растворах для наружных стен, фундаментов и получения бетона, железобетона, асбестоцементных и других изделий.
Источник
Гидравлические вяжущие вещества являются более сложными по составу, чем воздушные. Гидравлические вяжущие вещества в отличие от воздушных затвердевают и сохраняют свою прочность не только на воздухе, но и в воде. К гидравлическим вяжущим веществам относятся: известь гидравлическая и различные цементы (роман-цемент, портландцемент, шлакопортлащщемент и др.). Гидравлические вяжущие вещества применяются как в сухих, так и во влажных условиях: там, где требуется высокая прочность, и там, где нельзя применять воздушные вяжущие вещества. Их используют в кладочных и штукатурных растворах для наружных стен, фундаментов, а также для получения бетона, железобетона, асбестоцементных и других изделий.
Гидравлическая известь – продукт обжига кальциево-магни-евых карбонатных пород при температуре 1000 °С, содержащих 8-20% глинистых примесей. Выпускается в виде кусков или порошка. Основным показателем качества является гидравлический модуль. Гидравлический модуль есть отношение количества оксидов кальция (СаО) к общей сумме других оксидов:
где т – гидравлический модуль.
Если гидравлический модуль находится в пределах 1,7—4,5. материал обладает высокими гидравлическими свойствами и ближе к цементам; если он колеблется в пределах 4,5-9 единиц, он обладает низкими гидравлическими свойствами и по свойствам ближе к воздушной извести.
Роман-цемент – порошок от светло-желтого до бурого цвета, получаемый в результате тонкого помола обожженных не до спекания (при температуре 1000-1100 °С) известняков, содержащих свыше 20% глинистых примесей. По прочности делится на марки: 2, 5, 50 и 100. Начало схватывания – не ранее 15 мин, конец – не позднее 24 ч, остаток на сите № 008 не более 25%. Применяется для растворов при кладке и оштукатуривании стен и фундаментов, изготовления бетонов невысоких марок.
Портландцемент – основной вид гидравлических вяжущих веществ. Представляет собой тонкий порошок серого цвета с зеленоватым оттенком. Получается помолом обожженной до спекания при температуре 1450 °С смеси известняка (углекислый кальций) – 75% и глины – 25%. Портландцемент с необходимыми свойствами можно получить в том случае, когда содержание основных оксидов будет в следующих количествах: СаО – 60-67%, 8Ю2 -12-24%, А12О3 -4-7% и Ре2О3 – 2-6%. Вредными примесями являются М§О и 8О3, содержание которых соответственно допускается не более 5 и 3,5%. Увеличение их содержания вызывает неравномерное изменение объема при затвердевании и повышает сульфатную коррозию.
Производство портландцемента является сложным процессом. После подготовки сырьевых материалов они подвергаются обжигу. При обжиге под влиянием высокой температуры происходят сложные физико-химические процессы взаимодействия оксида кальция с другими оксидами, с образованием следующих минералов: трехкальциевого силиката (ЗСаО8Ю2) – 37-60%; двукаль-циевого силиката (2СаО8Ю2) – 15-37%; трехкальциевого алюмината (ЗСаОА12О3) – 7-15% и четырехкальциевого алюмоферрита (4СаОА12О3Ре2О3) – 10-18%, которые обусловливают гидравлические свойства портландцемента.
По прочности при сжатии в 28-суточном возрасте цемент подразделяется на марки: 400,500,550 и 600. Начало схватывания цемента должно наступить не ранее 45 мин, а конец – не позднее 10 ч от начала затворения. Остаток на сите № 008 не должен быть более 15%.
Шлакопортландцемент представляет собой портландцемент (20-85%) с добавками шлаков (15-80%). По свойствам похож на портландцемент, но является более дешевым. Выпускается трех марок: 300, 400 и 500.
ЛИСТОВЫЕ СТЕКЛОМАТЕРИАЛЫ
Сырьем для производства оконного стекла являются: кварцевый песок, известняк, сода, сульфат натрия, доломит, полевой шпат и др. Примерная рецептура его может быть представлена
Глава 10
Строительные товары
следующим образом, в %: 8Ю2– 71,8; А12О3 – 1,97;№2О- 14,85; Ре2О3 – 0,08; ЗО3 – 0,05; СаО – 6,65; М^О -4,10. Оконное стекло изготавливают на машинах вертикального и горизонтального вытягивания по лодочному и безлодочному способу. Выпускается это стекло в виде листов размером 250 * 250 до 1620 х 2200 мм при толщине 2, 3, 4, 5 и 6 мм. Применяется для остекления окон. дверей.
Полированное стекло вырабатывается способом горизонтального проката с последующей шлифовкой и полировкой поверхностей. Максимальные размеры полированного стекла -4450 х 2950 мм при толщине 7,5 мм и 2950 * 2950 мм при толщине 6,5 мм. При получении стекла методом плавающей ленты отпадает необходимость в его механической обработке (шлифовке и полировке). Полированное стекло применяется для устройства витрин, изготовления зеркал, автомобильных стекол и т. д. Полированное стекло выпускается трех сортов в зависимости от того, для каких целей оно предназначено:
– УА – для производства зеркал;
– УУА – для остекления средств транспорта;
– УУУ – для остекления оконных проемов жилых и обществен
ных зданий и витрин магазинов.
Узорчатое стекло – листовое стекло, на поверхности которого нанесен узор для-полного или частичного рассеивания света и создания декоративного эффекта.
Узорчатое стекло производят методом непрерывного проката ленты между двумя валками, на одном из которых гравировкой нанесен рисунок. В зависимости от рельефа рисунка видимость через стекло может быть частично или полностью исключена и сохранена светопропускаемость. Эти свойства узорчатого стекла позволяют широко использовать его для остекления оконных блоков и дверных полотен в производственных и жилых помещениях, для отделки вестибюлей, лестничных клеток общественных и административных зданий, магазинов, крытых веранд и др. Узорчатое стекло выпускается в листах толщиной 4-6 мм, размеры листов оговариваются заказчиком, но максимальные размеры – 1600 х 3600 мм.
Армированное стекло – листовое стекло, имеющее внутри стекла металлическую сетку. Армированное стекло производится методом непрерывного горизонтального проката ленты стекла, в процессе которого в него запрессовывается металлическая сетка, не позволяющая стеклу рассыпаться при ударах и при воздействии высоких температур. При пожарах стекло способно препятствовать распространению огня и дыма в помещениях. Армированное стекло может иметь гладкую, кованую или узорчатую поверхность. Размеры армированного стекла по длине – от 1200 до 2000 мм, по ширине – от 400 до 1500 мм при толщине – 6,5 мм. Оно применяется для остекления фонарей верхнего света, оконных переплетов, дверных филенок, устройства перегородок, светопрозрачных плафонов, ограждения лестничных маршей, балконов, лоджий и др.
Теплопоглощающее стекло используется для остекления оконных переплетов и фонарей верхнего света с целью уменьшения проникновения солнечной радиации в помещения. Стекло имеет легкую голубую и голубовато-зеленоватую окраску, почти не искажающую цвет просматриваемого через него предмета. Размеры идентичны размерам оконного стекла.
Теплозащитное стекло предназначено для защиты от тепловой радиации солнечного спектра. В отличие от тепло поглощающего стекла, окрашенного в массе, теплозащитное представляет собой обычное оконное стекло, на поверхность которого нанесена прозрачная пленка. Пленка имеет цвет от серо-дымчатого до сине-фиолетового. Интенсивность окраски можно регулировать также толщиной слоя, который изменяется в пределах 0,3-1,0 мк. Свето-пропускание светозащитного стекла задается в широких пределах (от 30 до 70%) независимо от толщины стекла.
Теплоотражателъпое стекло снимает теплопотери через оконные проемы и другие виды светопрозрачных ограждений в промышленных, общественных и жилых зданиях, теплицах, оранжереях, а также защищает от тепловой радиации, получаемой техническими источниками света.
Нанесение на стекло светоотражательной пленки практически не изменяет прозрачности стекла по отношению к солнечной радиации, но значительно снижает его способность поглощать
Глава 10
Строительные товары
длинноволновую радиацию и соответственно его излучательную способность благодаря повышению отражения. Последнее может достигать 60-80% для инфракрасного излучения. Степень черноты такого стекла снижается более чем в два раза. Такое стекло является теплоизоляционным.
Цветное стекло может вырабатываться различными способами и иметь разное назначение. Цветное накладное стекло, вырабатываемое методом вертикального вытягивания, может быть прозрачным и непрозрачным. Кроме этого, для получения цветного и тонированного строительного стекла используют пленки различного химического состава.
В нашей стране создана целая гамма цветных декоративных стекол, окрашенных от золотистого до красно-оранжевого цветов. Имеющие высокие декоративные свойства стекла оранжевого цвета задерживают ультрафиолетовую радиацию и могут быть использованы для остекления архивов, библиотек, других помещений, которые необходимо защитить от разрушающего воздействия ультрафиолетовых лучей. Прозрачное (зеленое, желтое, красное, синее) стекло применяется в качестве сигнального стекла.
Безосколочное трехслойное стекло “Триплекс” представляет собой трехслойное стекло, состоящее из двух листов, прочно соединенных находящейся между ними прозрачной эластичной полимерной прокладкой – поливинилбутиральной или бутафоль-ной (сополимеры поливинилбутираля) пленкой. Благодаря сочетанию хрупкого стекла с эластичной прокладкой, ‘Триплекс” при разрушении от ударов не дает отлетающих осколков. Все осколки растрескавшегося стекла прочно удерживаются на внутренней эластичной прокладке, поэтому применение стекла “Триплекс” исключает возможность получения травм от осколков. Максимальные размеры листов безосколочного трехслойного стекла составляют по длине 1200 мм, по ширине 600 мм при толщине от 4,5 до 6,5 мм. Стекло “Триплекс” применяется для остекления автомобилей.
Закаленное листовое стекло подвергается специальной термической обработке – закалке путем нагревания в электрических печах (при температуре 650-670 °С) с последующим быстрым охлаждением холодным воздухом в обдувной решетке. 526
В результате закалки наружные слои стекла сильно сжимаются, а внутренние – растягиваются, благодаря чему в стекле создается равномерное распределение напряжения, которое обеспечивает стеклу высокую механическую прочность и термическую устойчивость. Закаленное листовое стекло распадается на мелкие осколки округлой формы, без острых режущих граней; осколки могут удерживаться вместе. Закаленное стекло долговечно и практически не изменяет своих свойств в условиях эксплуатации.
Размеры листов закаленных стекол не превышают по длине 1200 мм, по ширине 600 мм при толщине 4,5-6,5 мм. Резка, обработка кромок листов стекла, сверление отверстий должно предшествовать закалке, т. к. закаленное стекло при проведении этих операций распадается на мелкие осколки.
Закаленное стекло широко используется в различных областях промышленности и в строительстве; для остекления автомобилей, самолетов, троллейбусов, электровозов, кабин экскаваторов; для остекления зданий больниц, школ и других общественных и производственных зданий.
Дата добавления: 2015-11-05; просмотров: 2189 | Нарушение авторских прав | Изречения для студентов
Читайте также:
Рекомендуемый контект:
Поиск на сайте:
© 2015-2020 lektsii.org – Контакты – Последнее добавление
Источник
Гидравлические
свойства вяжущих обусловлены наличием
в их составе силикатов, алюминатов,
ферритов кальция и зависят от
гидравлического модуля m и температуры
обжига сырья:
m =
,
m более 9 для воздушной
извести,
m = 1,7-9 для гидравлической
извести,
m = 1,1-1,7 – для
романцемента,
m = 1,9-2,4 – для
портландцемента.
Усиление гидравлических
свойств в ряду «воздушная известь
гидравлическая известь
романцемент» связано с уменьшением
гидравлического модуля с 9 до 2 при
одинаковой температуре обжига 10000С.
Увеличение температуры обжига сырья с
1000 0С
до 1450 0С,
при которой наблюдается частичное
плавление, приводит к получению
качественно нового вяжущего –
портландцемента.
6.3.1. Портландцемент
Портландцементом
называют гидравлическое вяжущее
вещество, в составе которого преобладают
высокоосновные силикаты Са (70-80%). Его
получают совместным помолом клинкера
с добавкой природного гипса (3-5%). Клинкер
представляет собой зернистый камнеподобный
материал, получаемый обжигом до спекания
(при 1450 0С)
тщательно подобранной сырьевой смеси.
Добавка гипса вводится для регулирования
сроков схватывания портландцемента.
Открытие портландцемента
(1824-1825 гг.) связывают с именами Е.Г.Челиева
и Д.Аспдина (Великобритания).
Сырьем
для производства портландцемента
служат:
– известняки с высоким
содержанием СаСО3
(мел, плотный известняк и др.);
– глинистые породы
состава Al2O3.nSiO2.mH2O
(глины, глинистые сланцы);
– корректирующие
добавки (пиритные огарки, трепел, опока,
бокситы и др.).
Соотношение между
карбонатными и глинистыми составляющими
сырьевой смеси 3:1 (75% известняка и 25%
глины).
Возможна замена
глинистого и частично карбонатного
компонента побочными продуктами
промышленности – доменными или
электротермофосфорными гранулированными
шлаками, а также нефелиновым шламом,
получающимся при производстве глинозема.
Производство
портландцемента
– сложный технологический и энергоемкий
процесс, состоящий из ряда операций,
которые можно разделить на две основные
стадии. Первая – производство клинкера,
вторая – измельчение клинкера совместно
с гипсом, а в ряде случаев и с активными
минеральными добавками.
Производство
клинкера
складывается из следующих технологических
операций:
– добыча и доставка
сырьевых материалов, их подготовка;
– приготовление
сырьевой смеси заданного состава путем
помола и смешивания сырьевых компонентов
в определенном количественном соотношении;
– обжиг сырьевой
смеси до спекания;
– интенсивное
охлаждение клинкера;
– складирование
клинкера.
Производство
портландцемента включает:
– подготовку
минеральных добавок (дробление, сушку);
– дробление гипсового
камня;
– помол клинкера с
активными минеральными добавками и
гипсом;
– складирование,
упаковку и отправку цемента потребителю.
Производство клинкера
может осуществляться сухим, мокрым и
комбинированным способом.
Сухой способ
заключается в приготовлении сырьевой
муки в виде тонкоизмельченного сухого
порошка (из сухих или предварительно
высушенных материалов) с остаточной
влажностью 1-2%.
При
мокром способе
сырьевые материалы измельчаются и
смешиваются в присутствии воды, поэтому
смесь получается в виде водной суспензии
– шлама с влажностью 35-45%. Это наиболее
энергоемкий способ.
Комбинированный
способ
заключается в том, что приготовленный
шлам до поступления в печь обезвоживается
на фильтрах до влажности 16-18%. Однако
энергоемкость производства в целом
остается высокой.
Обжиг сырьевой
смеси осуществляется в основном во
вращающихся печах, работающих по принципу
противотока. Печь имеет небольшой наклон
и вращается со скоростью 1-2 об/мин. При
мокром способе производства длина печи
достигает 185 м. Сырье подается в печь
со стороны ее верхнего (холодного) конца
и при вращении печи медленно двигается
к нижнему (горячему) концу, со стороны
которого вдувается топливо (природный
газ, мазут, воздушно-угольная смесь),
сгорающее в виде 20-30-метрового факела.
Двигаясь навстречу горячим газам,
образующимся при сгорании топлива,
сырье проходит различные температурные
зоны. В каждой зоне проходят различные
физико-химические превращения, в
результате которых и получается цементный
клинкер. Полученный в печи раскаленный
клинкер поступает в холодильник, где
резко охлаждается холодным воздухом.
Клинкер выдерживают на складе 1-2 недели.
Химический состав
клинкера выражают содержанием оксидов
(% по массе):
СаО – 63-66 %, SiO2
– 21-24 %, Al2O3
– 4-8 %, Fe2O3
– 2-4 %.
В процессе обжига,
доводимого до спекания смеси, главные
оксиды образуют силикаты, алюминаты и
алюмоферрит кальция в виде минералов
кристаллической структуры, а некоторая
их часть входит в стекловидную фазу.
Минеральный состав
клинкера:
– алит
3СаО. SiO2 (С3S)
– 45-60% – самый важный минерал, определяет
быстроту твердения, прочность и другие
свойства;
– белит
2СаО. SiO2 (С2S)
– 20-30% – медленно твердеет, но достигает
высокой прочности при длительных сроках
твердения;
– трехкальциевый
алюминат
3СаО. Al2O3
(С3А)
– 4-12% – быстро гидратируется и твердеет,
но конечная прочность его небольшая;
является причиной сульфатной коррозии
цементного камня;
– четырехкальциевый
алюмоферрит
4СаО. Al2O3
.Fe2O3
(С4АF)
– 10-20% по скорости твердения занимает
промежуточное положение между С3S
и С2S.
– клинкерное
стекло 5-15%
– затвердевшая в виде стекла часть
расплава, содержит СаО, Al2O3
, Fe2O3
, MgO, К2О,
Na2O.
–свободные
оксиды кальция и магния
могут присутствовать в виде зерен (СаО
своб) и в виде
минерала периклаза (MgО
своб); их
содержание не должно превосходить 1% и
5% соответственно; в случае их повышенного
содержания может проявляться неравномерное
изменение объема цемента при твердении
и появление трещин;
– щелочные
оксиды Na2O
и К2О
– их содержание не должно превышать
0,6%, так как при большем содержании они
могут явиться причиной коррозии
цементного бетона.
Твердение
портландцемента
происходит благодаря сложным
физико-химическим процессам взаимодействия
клинкерных минералов и гипса с водой.
2(3СаО. SiO2)
+ 6H2O
= 3СаО. 2SiO2.
3H2O
+ 3Са(ОН)2
гидросиликат
Са гидроксид Са
2(2СаО. SiO2)
+ 4H2O
= 3СаО. 2SiO2.
3H2O
+ Са(ОН)2
3СаО. Al2O3+
6H2O
= 3СаО. Al2O3.
6H2O
гидроалюминат
Са
В присутствии 3-5%
гипса образуется практически нерастворимое
соединение – гидросульфоалюминат кальция
(эттрингит), который предотвращает
быструю гидратацию С3А
за счет образования защитного слоя на
его поверхности и замедляет схватывание.
Кроме того, роль
добавки гипса состоит в улучшение
свойств цементного камня (прочности,
морозостойкости) за счет уплотнения
структуры, связанного с увеличением
объема эттрингита в еще не затвердевшей
системе.
3СаО. Al2O3
+ 3(СаSO4.2H2O)
+ 26 H2O
= 3СаО. Al2O3
. 3СаSO4.32H2O
гидросульфоалюминат
кальция (эттрингит)
4СаО. Al2O3
.
Fe2O3
+ mH2O
= 3СаО.
Al2O3
.
6H2O
+ СаО.
Fe2O3
. nH2O
гидроалюминат
Са
гидроферрит
Са
Структура цементного
камня может
быть представлена как микроскопическая
неоднородная дисперсная система –
“микробетон” (по В.Н. Юнгу).
Цементный камень
включает:
–
продукты
гидратации цемента
гель
гидросиликатов (до 75% объема) и другие
новообразования;кристаллы
Са(ОН)2
и эттрингита;
– непрореагировавшие
зерна клинкера –
клинкерный фонд;
– поры:
поры
геля (менее 0,1 мкм),капиллярные
поры (от 0,1 до 10 мкм) между агрегатами
частиц геля,воздушные
поры (от 50 мкм до 2 мм).
Свойства
портландцемента
Тонкость
помола цемента
определяет быстроту твердения и прочность
цементного камня. Она должна быть такой,
чтобы через сито № 008 проходило не менее
85% массы пробы (Sуд
= 2500-3000 см2/г.).
Истинная
плотность
= 3,05-3,15 г/см3.
Насыпная плотность
в среднем составляет 1300 кг/м3.
Водопотребность
портландцемента
характеризуется количеством воды (% от
массы цемента), необходимым для получения
цементного теста нормальной густоты и
составляет 22-28%.
Сроки схватывания
цементов определяют с помощью прибора
Вика (табл. 6.2). Для информации в таблице
приведены сроки схватывания и основного
алюминатного цемента – глиноземистого.
Таблица 6.2
Источник