Какая существует связь между твердым раствором и свойствами сплава
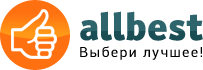
Гл.3 СВОЙСТВА МЕТАЛЛОВ И СПЛАВОВ
CВЯЗЬ МЕЖДУ СТРУКТУРОЙ И СВОЙСТВАМИ СПЛАВОВ
Между составом и структурой сплава, определяемой типом диаграммы состояния, и свойствами сплава существует определенная зависимость.
При образовании твердого раствора предел прочности, текучести и твердость повышаются при сохранении достаточно высокой пластичности. При образовании твердого раствора внедрения прочность во много раз больше, чем при образовании твердого раствора замещения той же концентрации,
Сочетание повышенной прочности и хорошей пластичности позволяет использовать твердые растворы как основу конструкционных сплавов.
Благодаря высокой пластичности сплавы — твердые растворы легко деформируются, но плохо обрабатываются резанием. Такие сплавы имеют низкие литейные свойства.
При образовании твердых растворов значительно увеличивается электросопротивление. Поэтому сплавы — твердые растворы широко применяют для изготовления проволоки электронагревательных элементов и реостатов.
Для получения высоких литейных свойств концентрация компонентов в сплавах должна превышать их предельную растворимость в твердом состоянии и приближаться к эвтектическому составу. Эвтектические сплавы обладают хорошей жидкотекучестью. Но при появлении в структуре сплава эвтектики сильно снижается его пластичность. Поэтому в деформируемых сплавах содержание компонентов не превышает величины предельной растворимости при эвтектической температуре.
Химические соединения, образующиеся в сплавах, обладают свойствами, резко отличающимися от свойств исходных компонентов. Они имеют очень высокую твердость, но хрупки. Химические соединения имеют большое значение в качестве твердых структурных составляющих в сплавах.
Контрольные вопросы
1. Что называется сплавом?
2. Что называется эвтектикой?
3. Какая существует связь между твердым раствором и свойствами сплавов?
В зависимости от назначения изделий металлы и сплавы должны обладать определенными свойствами, которые разделяются на четыре группы: физические, химические, механические и технологические.
К физическим свойствам металлов и сплавов относятся:
—плотность — количество вещества, содержащегося в единице объема, г/см3;
—температура плавления, °С — температура, при
которой металл полностью переходит из твердого
состояния в жидкое;
—теплопроводность (кал/с´мин´град) — это способность тел передавать с той или иной скоростью
тепло при нагревании и охлаждении. Единицей
измерения теплопроводности служит количество
тепла, распространяющегося по единице длины
металла через единицу площади его поперечного
сечения в единицу времени;
—тепловое расширение — металлы расширяются при
нагревании и сжимаются при охлаждении. Изменение линейного размера при нагреве называютлинейным расширением; изменение объема тела — объемным расширением;
—удельная теплоемкость — это количество тепла,
которое необходимо для повышения температуры
1 г вещества на 1°C;
—электропроводность— способность металлов
проводить электрический ток. Под удельным электрическим сопротивлением r понимают сопротивление проводника длиной 1 м и площадью поперечного сечения 1 мм2;
—способность намагничиваться — это способность
металла создавать собственное магнитное поле
либо самостоятельно, либо под действием внешнего магнитного поля.
Химические свойства— это свойства металлов и сплавов, определяющие отношение их к химическим воздействиям различных сред.
Химические воздействия среды проявляются в различных формах: металлы подвергаются атмосферной коррозии; при нагреве в закалочных печах без защитной атмосферы поверхность изделий покрывается окалиной; в кислотах металлы растворяются. Поэтому для практического использования металлов и сплавов необходимо знать их химические свойства.
Например, металлы и сплавы, стойкие против окисления при сильном нагреве (жаростойкие, окалиностойкие) применяются для изготовления различных сильно нагревающихся деталей автомобилей (выпускные коллекторы, глушители).
Источник
Содержание:
- При образовании твердого раствора важен предел прочности
- Получения высоких литейных свойств
- Сплавы, допускающие горячую и холодную обработку
- Схема микроструктур сплавов
- Фазовый состав и свойства сплавов
При образовании твердого раствора важен предел прочности
Существует четкая взаимосвязь между составом и структурой сплава, которая определяется типом диаграммы состояния и характеристиками сплава.
При образовании твердого раствора прочность на растяжение, предел текучести и твердость увеличиваются, сохраняя при этом достаточно высокую ductility. In при образовании твердого раствора входного типа прочность во много раз больше, чем при образовании замещенного твердого раствора той же концентрации.
Сочетание повышенной прочности и отличной пластичности позволяет использовать твердые растворы в качестве основы для конструкционных сплавов.
Благодаря своей высокой пластичности сплав-твердый раствор легко деформируется, но обработка резанием оказывается недостаточной. Такие сплавы обладают низкой Литейной способностью.
- За счет образования твердого раствора электрическое сопротивление значительно возрастает. Поэтому сплав-твердый раствор широко используется в производстве проволочных нагревательных элементов и реостатов.
Получения высоких литейных свойств
Для получения высоких литейных свойств концентрация компонентов в сплаве превышает конечную растворимость в твердом состоянии и должна приближаться к эвтектическому составу. Эвтектический сплав обладает хорошей текучестью.
Однако, когда эвтектика появляется в структуре сплава, его пластичность значительно снижается. Поэтому в кованых сплавах содержание компонентов не превышает значения предельной растворимости при эвтектической температуре.
- Соединения, образующиеся в сплаве, имеют значительно отличающиеся свойства от свойств исходного компонента. У них очень высокая твердость, но они рассыпчатые. Соединение очень важно как твердый структурный компонент сплава.
В состав сплава входят металлы (железо, медь, алюминий, никель и др.) и неметаллические элементы (углерод).Соединения, находящиеся в рассматриваемом интервале температур, если они не диссоциируют на составные части, могут быть компонентом. Количество компонентов, составляющих систему (сплав), может быть различным.
Чистые металлы-это однокомпонентные системы.
Техническая ценность материала зависит от структуры и выражается в его свойствах, например, сплав 2 металлов-2 компонента.
Структура материала характеризуется его структурой. Структура-это набор стабильных связующих элементов materials. It обеспечивает его целостность и сохранение основных характеристик, наряду с внешними и внутренними модификациями. Структура материала определяется многими факторами: строением атомов, ионов, молекул, распределением электронов в нем, типами связей между частицами. В зависимости от назначения изделия, металлы и сплавы нуждаются в определенных свойствах.
Сплавы, допускающие горячую и холодную обработку
Эти свойства подразделяются на 4 группы: физические, химические, механические и технические. Чистый металл после кристаллизации всегда состоит из одного и того же типа мелких кристаллов. Из злаков того же химического состава. Ряд частиц (кристаллитов) одного и того же химического состава называется фазой. Все чистые металлы однофазны. В отличие от чистых металлов, процесс формирования сплава значительно сложнее. Результаты кристаллизации редко становятся ясными.
Это обусловлено взаимной растворимостью компонентов, условиями охлаждения и последующей термообработкой. Если сплав состоит из частиц одинакового химического состава, то он однофазный (однородный).
Если образуются кристаллы различного химического состава, то сплав считается многофазным(гетерогенным) и его фазовый состав определяется типом образующихся кристаллов.
Зерно в разных фазах может сосуществовать по-разному. Структура частиц невидима невооруженным глазом, но она доступна только для микроскопического исследования тонких, полированных и вытравленных деталей.
- Структура сплава, наблюдаемая под микроскопом, называется микроструктурой (на самом деле ее часто называют просто «структурой»).
Схема микроструктур сплавов
Механические, технологические и другие свойства в конечном счете определяются фазовым составом и структурными компонентами. Этим объясняется целесообразность наличия большого количества сплавов, химический состав которых часто»незначительно» отличается.
Существует четкая взаимосвязь между фазовым составом и свойствами сплава. Однофазные сплавы на основе ненасыщенных α-растворов пригодны для холодной и горячей деформации, так как обладают высокой пластичностью при низких и высоких температурах.
- Поскольку при изменении температуры не происходит фазового превращения, исключается возможность термического упрочнения, и поэтому отверждается только холодная деформация. 。Многофазные сплавы с низкой пластичностью или хрупкими фазами имеют пониженную пластичность.
Фазовый состав и свойства сплавов
Обычно они ограничиваются обработкой давлением (например, только в «горячем»или» холодном » состоянии) или вообще не деформируются.
Реферат на тему | На заказ | Образец и пример |
Связь между структурой и свойствами сплавов | Большинство различных металлических материалов, используемых в технологии, являются сплавами. | Чистые металлы не используются в технологии, поскольку они характеризуются низкой прочностью на растяжение. |
Сплавы, содержащие компоненты, растворимость которых изменяется, допускают термическое упрочнение (за счет закалки и последующего старения).
Сплавы с составом, близким к эвтектическому, обладают повышенными литейными свойствами (из-за отсутствия крупных первичных кристаллов используются бывшие эвтектические сплавы).
Рефераты по материаловедению
Источник
Рассмотренные диаграммы состояния характеризуют строение сплавов различного состава. Мы видели, что в зависимости от состава (т. е. от содержания компонентов) сплавы могут иметь разнообразную структуру в соответствии с типом диаграммы состояния. Основоположником учения о связи диаграммы состояния со свойствами сплавов является акад. Н. С. Курнаков.
Зависимость свойств от состава сплавов в общем виде приведена на рис. 1.
а) В сплавах, имеющих структуру механических смесей (рис. 1, а), свойства изменяются в основном прямолинейно. Некоторые свойства механических смесей, в первую очередь НВ и σв, зависят от размеров частиц, т. е. от степени дисперсности. В эвтектических и близко к ним расположенных сплавах фазы измельчены в наибольшей степени, поэтому механические свойства, как это показано на рис. 1, а и б штриховыми линиями, значительно повышаются.
Рис. 1. Зависимость свойств от состава сплавов (вида диаграммы состояния)
б) Если диаграмма показывает, что в сплавах образуется разнообразная структура, то и зависимость свойств тоже неоднозначна (рис. 1, б). А именно, в сплавах-твердых растворах, граничных с чистыми компонентами А и В, свойства изменяются по кривым, а в сплавах-смесях твердых растворов зависимость вновь прямолинейная.
в) В сплавах-твердых растворах свойства изменяются по криволинейной зависимости, т. е. более существенно, чем для сплавов, имеющих структуру смеси кристаллов (1, в).
г) При образовании химических соединений (рис. 1, г) свойства изменяются скачком, очень резко.
Охарактеризуем более подробно изменение свойств в сплавах, в которых образуются ограниченные твердые растворы и механические смеси этих растворов. Изменение некоторых физических и технологических свойств в этом случае показано на рис. 2. Многие физические и механические свойства сплавов четко зависят от структуры, но такие технологические свойства, как литейные (т. е. способность обеспечить хорошее качество отливок) или свариваемость, зависят не столько от структуры, сколько от того, в каких условиях по температуре проходило затвердевание сплавов.
Поэтому о зависимости механических и физических свойств однофазных сплавов (α и β), т. е, сплавов, лежащих левее Si и правее S2 диаграммы, приведенной на рис. 2, можно сделать следующие выводы:
а) твердость НВ, прочность σв и электросопротивление твердых растворов выше, чем у чистых металлов (рис. 2, кривые 1 и 2, отрезки аб и вг);
б) электропроводность и температурный коэффициент электросопротивления у твердых растворов ниже, чем у чистых металлов (рис. 2, кривые 3 и 4, отрезки аб и вг);
в) электрохимический потенциал изменяется по плавной (для полностью однородных твердых растворов) кривой (рис. 2, кривая 5, отрезки аб и гд);
Технологические литейные свойства, определяющие способность сплава при затвердевании дать высококачественные отливки, слитки, детали, зависят от жидкотекучести, несклонности к образованию трещин внутри и на поверхности слитков, образования рассеянной пористости или усадочной сосредоточенной раковины.
Жидкотекучесть — это способность заполнять литейную форму сложной конфигурации. Она зависит от интервала кристаллизации сплава. Чем больше расстояние между ликвидусом и солидусом, т. е. чем больше интервал кристаллизации, тем ниже жидкотекучесть.
Поэтому сплавы-твердые растворы (рис. 2, кривая 6, отрезки аб и вг) имеют пониженную жидкотекучесть.
Кроме того, чем больше интервал кристаллизации, тем сплавы более склонны образовывать трещины на поверхности и внутри отливки.
В результате усадки образуются мелкая пористость, разбросанная по всему объему отливки (что нередко выводит литье в брак), которая тем больше чем больше расстояние между ликвидусом и солидусом (т. е. чем больше интервал кристаллизации); при малом интервале кристаллизации в сплавав образуется сосредоточенная усадочная раковина.
На рис. 2, кривая 7 показан общий объем пустот, которые складываются из мелких пор и усадочной раковины. Как видно из рисунка, чем больше интервал кристаллизации, тем больше мелкой пористости (рассеянные поры). Следовательно, для получения качественных отливок необходимо выбрать сплавы, у которых температуры ликвидуса и солидуса были бы как можно ближе.
Следовательно, в однофазных сплавах, представляющих собой твердые растворы α или β, наибольшую рассеянную пористость будут иметь сплавы, состав которых близок составу в точках Si или S2.
Таким образом, однофазные сплавы-твердые растворы обладают плохими литейными свойствами и не пригодны для фасонного литья. Однако однофазные сплавы, представляющие собой твердые растворы, при достаточно высокой прочности обладают хорошей пластичностью, высоким сопротивлением коррозии. Поэтому сплавы-твердые растворы являются наилучшими для изготовления деталей методами обработки металлов давлением, когда качество деталей будет определяться технологической пластичностью сплава.
В отношении механических смесей фаз (α + β), т. е. для сплавов состава в интервале Sx—S2 диаграммы рис. 2 следует, что электросопротивление (кривая 2, отрезок бе), электропроводность (кривая 3, отрезок бв), температурный коэффициент электропроводности (кривая 4, отрезок бв), электрохимический потенциал (кривая 5, отрезок бв) изменяются по прямым линиям. Прочность (σв) и твердость (НВ) в случае, когда фазы при кристаллизации эвтектики не слишком измельчены (или укрупнены в результате специального отжига), также изменяются прямолинейно (рис. 2, кривая 1, отрезок бв). В случае, когда смесь состоит из высокодисперсных фаз, наблюдается резкое отклонение от прямолинейной зависимости и для сплавов эвтектического состава на кривых свойств виден перелом или даже ясно выраженный пик (рис. 2, кривая 1, сплошная линия бдв).
Литейные свойства изменяются по указанному выше закону: чем больше интервал кристаллизации, тем меньше жидкотекучесть 6, больше мелкой пористости 7, больше склонность к образованию наружных трещин и т. д.
Следовательно, наилучшими литейными сплавами будут эвтектические, а худшими — сплавы, соответствующие предельным твердым растворам (Si и S2). В то же время двухфазная структура обеспечивает низкую технологическую пластичность, поэтому эвтектические сплавы не пригодны для обработки давлением.
Лучшая обрабатываемость резанием выявлена у сплавов, имеющих структуру эвтектики, эти же сплавы дают и наилучшую чистоту поверхности при токарной обработке.
Очень важно отметить значительное влияние химических соединений на свойства сплавов. Присутствие их в сплавах даже в небольших количествах значительно повышает прочность, износостойкость, жаропрочность и другие свойства, необходимые при эксплуатации деталей.
Из изложенного видно, что диаграммы состояния позволяют на научной основе предвидеть поведение сплавов, выбирать сплавы в зависимости от их назначения, применять различные виды термической обработки и другие методы воздействия для получения заданной структуры и свойств.
Рис. 2. Зависимость свойств сплава от состава
при образовании ограниченных твердых растворов:
1 — σв; 2 — электросопротивление; 3 — электропроводность;
4 — температурный коэффициент электросопротивлении;
5 — электрохимический потенциал; 6 — жидкотекучесть;
7 — объемная усадка
Читайте также:
Рекомендуемые страницы:
©2015-2020 poisk-ru.ru
Все права принадлежать их авторам. Данный сайт не претендует на авторства, а предоставляет бесплатное использование.
Дата создания страницы: 2016-08-20
Нарушение авторских прав и Нарушение персональных данных
Источник
Ñõåìû ìèêðîñòðóêòóð ñïëàâîâ. Âîçìîæíûå ôàçû â ñïëàâàõ: òâåðäûå ðàñòâîðû, ÷èñòûå ìåòàëëû, õèìè÷åñêèå ñîåäèíåíèÿ. Ñâÿçü ìåæäó ôàçîâûì ñîñòàâîì è ìåõàíè÷åñêèìè, òåõíîëîãè÷åñêèìè ñâîéñòâàìè ñïëàâîâ. Äèàãðàììû ñîñòîÿíèé è âëèÿíèå ïðèìåñåé íà “÷èñòûå” ìåòàëëû.
Îòïðàâèòü ñâîþ õîðîøóþ ðàáîòó â áàçó çíàíèé ïðîñòî. Èñïîëüçóéòå ôîðìó, ðàñïîëîæåííóþ íèæå
Ñòóäåíòû, àñïèðàíòû, ìîëîäûå ó÷åíûå, èñïîëüçóþùèå áàçó çíàíèé â ñâîåé ó÷åáå è ðàáîòå, áóäóò âàì î÷åíü áëàãîäàðíû.
Ðàçìåùåíî íà https://www.allbest.ru/
Ðàçìåùåíî íà https://www.allbest.ru/
Ìèíèñòåðñòâî îáðàçîâàíèÿ è íàóêè ÐÔ
Ôåäåðàëüíîå ãîñóäàðñòâåííîå àâòîíîìíîå îáðàçîâàòåëüíîå ó÷ðåæäåíèå âûñøåãî ïðîôåññèîíàëüíîãî îáðàçîâàíèÿ
«Ðîññèéñêèé ãîñóäàðñòâåííûé ïðîôåññèîíàëüíî-ïåäàãîãè÷åñêèé óíèâåðñèòåò»
Èíñòèòóò ýëåêòðîýíåðãåòèêè è èíôîðìàòèêè
Êàôåäðà Ìåòàëëóðãèè, ñâàðî÷íîãî ïðîèçâîäñòâà è ìåòîäèêè ïðîôåññèîíàëüíîãî îáó÷åíèÿ
ÐÅÔÅÐÀÒ
ïî äèñöèïëèíå «Ìåòàëëîâåäåíèå è òåðìè÷åñêàÿ îáðàáîòêà ìåòàëëîâ»
íà òåìó: Ñâÿçü ìåæäó ñòðóêòóðîé è ñâîéñòâàìè ñïëàâîâ
Ðàáîòó âûïîëíèë
ñòóäåíò 2 êóðñà ãðóïïû ÌÏ-203
Ïðÿíè÷íèêîâ È.Ì.
Ïðåïîäàâàòåëü: Ñòðîøêîâ Â.Ï.
Åêàòåðèíáóðã
2015
Ñîäåðæàíèå
Ââåäåíèå
1. Âîçìîæíûå ôàçû â ñïëàâàõ
1.1 Òâåðäûé ðàñòâîð
1.2 ×èñòûå ìåòàëëû
1.3 Õèìè÷åñêèå ñîåäèíåíèÿ
2. Ôàçîâûé ñîñòàâ è ñâîéñòâà ñïëàâîâ
3. Äèàãðàììû ñîñòîÿíèÿ
4. Ïðèìåñè â ñïëàâàõ
Çàêëþ÷åíèå
- Ñïèñîê ëèòåðàòóðû
- ÂÂÅÄÅÍÈÅ
Îñíîâíóþ äîëþ ðàçíîîáðàçíûõ ìåòàëëè÷åñêèõ ìàòåðèàëîâ, èñïîëüçóåìûõ â òåõíèêå, ñîñòàâëÿþò ñïëàâû. ×èñòûå ìåòàëëû â òåõíèêå íå ïðèìåíÿþò, ïîòîìó ÷òî îíè õàðàêòåðèçóþòñÿ íèçêèì ïðåäåëîì ïðî÷íîñòè. Ïóòåì ñïëàâëåíèÿ èëè ñïåêàíèÿ íåñêîëüêèõ ìåòàëëîâ èëè ìåòàëëîâ ñ íåìåòàëëè÷åñêèìè ýëåìåíòàìè ïîëó÷àþò ñïëàâû, êîòîðûå îáëàäàþò âûñîêîé ïðî÷íîñòüþ, ïëàñòè÷íîñòüþ, õîðîøî îáðàáàòûâàþòñÿ ðåçàíèåì, ñâàðèâàþòñÿ è ò.ä. Ïðè ýòîì óëó÷øàþòñÿ ýêñïëóàòàöèîííûå è òåõíîëîãè÷åñêèå ñâîéñòâà ìåòàëëè÷åñêîãî ìàòåðèàëà.
Ñïëàâîì íàçûâàåòñÿ ìàêðîñêîïè÷åñêè îäíîðîäíàÿ ñèñòåìà, ñîñòîÿùàÿ èç äâóõ è áîëåå õèìè÷åñêèõ ýëåìåíòîâ. Âåùåñòâà, îáðàçóþùèå ñèñòåìó, íàçûâàþò êîìïîíåíòàìè.
Êîìïîíåíòàìè ñïëàâà ìîãóò áûòü ìåòàëëû (æåëåçî, ìåäü, àëþìèíèé, íèêåëü è ò.ä.) è íåìåòàëëè÷åñêèå ýëåìåíòû (óãëåðîä). Êîìïîíåíòîì ìîãóò áûòü è õèìè÷åñêèå ñîåäèíåíèÿ, åñëè â ðàññìàòðèâàåìûõ èíòåðâàëàõ òåìïåðàòóð îíè íå äèññîöèèðóþò íà ñâîè ñîñòàâíûå ÷àñòè. Êîëè÷åñòâî êîìïîíåíòîâ, ñîñòàâëÿþùèõ ñèñòåìó (ñïëàâ), ìîæåò áûòü ðàçëè÷íûì. ×èñòûé ìåòàëë – ýòî îäíîêîìïîíåíòíàÿ ñèñòåìà; ñïëàâ äâóõ ìåòàëëîâ – äâóõêîìïîíåíòíàÿ, è ò.ä.
Òåõíè÷åñêîå çíà÷åíèå ìàòåðèàëîâ çàâèñèò îò ñòðîåíèÿ è âûðàæàåòñÿ â èõ ñâîéñòâàõ. Ñòðîåíèå ìàòåðèàëîâ õàðàêòåðèçóåò ñòðóêòóðà.
Ñòðóêòóðà — ñîâîêóïíîñòü óñòîé÷èâûõ ñâÿçåé ìàòåðèàëà, îáåñïå÷èâàþùèõ åãî öåëîñòíîñòü è ñîõðàíåíèå îñíîâíûõ ñâîéñòâ, ïðè âíåøíèõ è âíóòðåííèõ èçìåíåíèÿõ.
Ñòðóêòóðà ìàòåðèàëîâ îïðåäåëÿåòñÿ ìíîæåñòâîì ôàêòîðîâ: ñòðîåíèåì àòîìîâ, èîíîâ, ìîëåêóë, ðàñïðåäåëåíèåì â íèõ ýëåêòðîíîâ, òèïîì ñâÿçåé ìåæäó ÷àñòèöàìè è ò. ä.  ìàòåðèàëîâåäåíèè ïðèíÿòî ðàññìàòðèâàòü òðè óðîâíÿ ñòðîåíèÿ ìàòåðèàëîâ: àòîì–ìîëåêóëà–ôàçà.
 çàâèñèìîñòè îò íàçíà÷åíèÿ èçäåëèé ìåòàëëû è ñïëàâû äîëæíû îáëàäàòü îïðåäåëåííûìè ñâîéñòâàìè, êîòîðûå ðàçäåëÿþòñÿ íà ÷åòûðå ãðóïïû: ôèçè÷åñêèå, õèìè÷åñêèå, ìåõàíè÷åñêèå è òåõíîëîãè÷åñêèå. ×èñòûå ìåòàëëû ïîñëå êðèñòàëëèçàöèè âñåãäà ñîñòîÿò èç êðèñòàëëèòîâ îäíîãî òèïà, ò.å. èç çåðåí îäèíàêîâîãî õèìè÷åñêîãî ñîñòàâà. Ñîâîêóïíîñòü çåðåí (êðèñòàëëèòîâ) îäèíàêîâîãî õèìè÷åñêîãî ñîñòàâà íàçûâàåòñÿ ôàçîé. Âñå ÷èñòûå ìåòàëëû ÿâëÿþòñÿ îäíîôàçíûìè.
 îòëè÷èå îò ÷èñòûõ ìåòàëëîâ ïðîöåññ îáðàçîâàíèÿ ñïëàâîâ íàìíîãî ñëîæíåå. Ðåçóëüòàò êðèñòàëëèçàöèè ðåäêî áûâàåò îäíîçíà÷íûì, ïîñêîëüêó îïðåäåëÿåòñÿ íåñêîëüêèìè ôàêòîðàìè: âçàèìíîé ðàñòâîðèìîñòüþ êîìïîíåíò, óñëîâèÿìè îõëàæäåíèÿ, ïîñëåäóþùåé òåðìîîáðàáîòêîé. Åñëè ñïëàâ ñîñòîèò èç çåðåí îäíîãî õèìè÷åñêîãî ñîñòàâà, òî îí ÿâëÿåòñÿ îäíîôàçíûì (ãîìîãåííûì). Åñëè îáðàçóþòñÿ êðèñòàëëû ðàçíîãî õèìè÷åñêîãî ñîñòàâà, òî ñïëàâ ñ÷èòàåòñÿ ìíîãîôàçíûì (ãåòåðîãåííûì), à ðàçíîâèäíîñòè îáðàçóþùèõñÿ êðèñòàëëîâ îïðåäåëÿþò åãî ôàçîâûé ñîñòàâ.
Çåðíà ðàçíûõ ôàç ìîãóò ïî-ðàçíîìó ñîñóùåñòâîâàòü äðóã ñ äðóãîì. Íåâîîðóæåííûì ãëàçîì ç¸ðåííîå ñòðîåíèå íå âèäíî, îíî äîñòóïíî òîëüêî ïðè ìèêðîñêîïè÷åñêîì èññëåäîâàíèè ïîëèðîâàííûõ, ïðåäâàðèòåëüíî ïðîòðàâëåííûõ øëèôîâ. Ñòðîåíèå ñïëàâà, íàáëþäàåìîå ÷åðåç ìèêðîñêîï, íàçûâàåòñÿ ìèêðîñòðóêòóðîé (íà ïðàêòèêå î÷åíü ÷àñòî ãîâîðÿò ïðîñòî «ñòðóêòóðà»).
Ðèñóíîê 1 – ñõåìà ìèêðîñòðóêòóð ñïëàâîâ: à – äîýâòåêòè÷åñêèé, á – ýâòåêòè÷åñêèé, â – çàýâòåêòè÷åñêèé
Ó÷àñòêè ìèêðîñòðóêòóðû, êîòîðûå îäèíàêîâî âûãëÿäÿò ïðè ðàññìîòðåíèè ÷åðåç ìèêðîñêîï, íàçûâàþòñÿ ñòðóêòóðíûìè ñîñòàâëÿþùèìè. Îíè èìåþò îäíîîáðàçíóþ ôîðìó, äèñïåðñíîñòü (ðàçìåðû) è âçàèìíîå ðàñïîëîæåíèå çåðåí. Ñòðóêòóðíûå ñîñòàâëÿþùèå ìîãóò ñîñòîÿòü èç êðèñòàëëîâ îäíîé ôàçû èëè èç çåðåí íåñêîëüêèõ ôàç.
Ñâîéñòâà ñïëàâîâ îïðåäåëÿþòñÿ èõ ìèêðîñòðóêòóðîé, ò.å. âèäîì è ñîñòàâîì ñòðóêòóðíûõ ñîñòàâëÿþùèõ, êîòîðûå, â ñâîþ î÷åðåäü, îïðåäåëÿþòñÿ ôàçîâûì ñîñòàâîì.
Ïîäîáíûå äîêóìåíòû
Ñâîéñòâà ìåòàëëîâ è ñïëàâîâ. Äâîéíûå ñïëàâû. Ìåòàëëû ïðèìåíÿåìûå â ïîëèãðàôèè. Òåõíè÷åñêèå òðåáîâàíèÿ ê òèïîãðàôñêèì ñïëàâàì. Âàæíåéøèå ñâîéñòâà òèïîãðàôñêèõ ñïëàâîâ. Ìåòàëëû äëÿ èçãîòîâëåíèÿ òèïîãðàôñêèõ ñïëàâîâ. Äèàãðàììû ñîñòîÿíèÿ êîìïîíåíòîâ.
ðåôåðàò [32,5 K], äîáàâëåí 03.11.2008
Ñâîéñòâà è àòîìíî-êðèñòàëëè÷åñêîå ñòðîåíèå ìåòàëëîâ. Ýíåðãåòè÷åñêèå óñëîâèÿ ïðîöåññà êðèñòàëëèçàöèè. Ñòðîåíèå ìåòàëëè÷åñêîãî ñëèòêà. Èçó÷åíèå ñâÿçè ìåæäó ñâîéñòâàìè ñïëàâîâ è òèïîì äèàãðàììû ñîñòîÿíèÿ. Êîìïîíåíòû è ôàçû æåëåçîóãëåðîäèñòûõ ñïëàâîâ.
êóðñîâàÿ ðàáîòà [871,7 K], äîáàâëåí 03.07.2015
Çàâèñèìîñòü ìåæäó ñîñòàâîì è ñòðóêòóðîé ñïëàâà, îïðåäåëÿåìîé òèïîì äèàãðàììû ñîñòîÿíèÿ è ñâîéñòâàìè ñïëàâà. Ñîñòîÿíèÿ ñïëàâîâ, êîìïîíåíòû êîòîðûõ èìåþò ïîëèìîðôíûå ïðåâðàùåíèÿ. Ñîñòîÿíèå ñ ïîëèìîðôíûì ïðåâðàùåíèåì äâóõ êîìïîíåíòîâ. Ìèêðîñòðóêòóðà ñïëàâà.
êîíòðîëüíàÿ ðàáîòà [724,7 K], äîáàâëåí 12.08.2009
Ïîíÿòèå î ìåòàëëè÷åñêèõ ñïëàâàõ. Âèäû äâîéíûõ ñïëàâîâ. Ïðîäóêòû, îáðàçóþùèåñÿ ïðè âçàèìîäåéñòâèè êîìïîíåíòîâ ñïëàâà â óñëîâèÿõ òåðìîäèíàìè÷åñêîãî ðàâíîâåñèÿ. Äèàãðàììû ñîñòîÿíèÿ äâîéíûõ ñïëàâîâ, õàðàêòåð èçìåíåíèÿ ñâîéñòâ â çàâèñèìîñòè îò èõ ñîñòàâà.
êîíòðîëüíàÿ ðàáîòà [378,1 K], äîáàâëåí 08.12.2013
Âëèÿíèå âûñîêîòåìïåðàòóðíîé òåðìîìåõàíè÷åñêîé îáðàáîòêè íà òîíêóþ êðèñòàëëè÷åñêóþ ñòðóêòóðó àóñòåíèòíûõ ñòàëåé è ñïëàâîâ. Çàêîíîìåðíîñòè ðîñòà çåðåí ìåòàëëîâ è ñïëàâîâ ïðè âûñîêèõ òåìïåðàòóðàõ. Âëèÿíèå òåìïåðàòóðû íà õàðàêòåðèñòèêè ìåòàëëîâ.
êóðñîâàÿ ðàáîòà [534,9 K], äîáàâëåí 28.12.2003
Îñîáåííîñòè ìåäíûõ ñïëàâîâ, èõ ïîëó÷åíèå ñïëàâëåíèåì ìåäè ñ ëåãèðóþùèìè ýëåìåíòàìè è ïðîìåæóòî÷íûìè ñïëàâàìè – ëèãàòóðàìè. Îáðàáîòêà ìåäíûõ ñïëàâîâ äàâëåíèåì, ñâîéñòâà ëèòåéíûõ ñïëàâîâ è îáëàñòü èõ ïðèìåíåíèÿ. Âëèÿíèå ïðèìåñåé è äîáàâîê íà ñâîéñòâà ìåäè.
êóðñîâàÿ ðàáîòà [994,4 K], äîáàâëåí 29.09.2011
Ìèêðîñòðóêòóðà è óãëåðîäèñòûõ ñòàëåé â îòîææåííîì ñîñòîÿíèè, çàâèñèìîñòü ìåæäó èõ ñòðîåíèåì è ìåõàíè÷åñêèìè ñâîéñòâàìè. Èçó÷åíèå äèàãðàììû ñîñòîÿíèÿ æåëåçî – óãëåðîä. Êðèâàÿ îõëàæäåíèÿ ñïëàâîâ. Ñòðóêòóðà áåëîãî, ñåðîãî, âûñîêîïðî÷íîãî è êîâêîãî ÷óãóíà.
ïðåçåíòàöèÿ [1,5 M], äîáàâëåí 21.12.2010
Ïðèíöèï ïîñòðîåíèÿ äèàãðàììû ñîñòîÿíèé ñïëàâîâ, îáðàçóþùèõ îãðàíè÷åííûå òâåðäûå ðàñòâîðû. Îïèñàíèå ñòðóêòóðíûõ è ôàçîâûõ ïðåâðàùåíèé ïðè ìåäëåííîì îõëàæäåíèè èç æèäêîãî ñîñòîÿíèÿ ñïëàâà ñ çàäàííûì ñîäåðæàíèåì óãëåðîäà. Ïðåâðàùåíèÿ â ñòðóêòóðå ñòàëè.
êîíòðîëüíàÿ ðàáîòà [1,1 M], äîáàâëåí 17.10.2011
Îïðåäåëåíèå ìåõàíè÷åñêèõ ñâîéñòâ êîíñòðóêöèîííûõ ìàòåðèàëîâ ïóòåì èñïûòàíèÿ èõ íà ðàñòÿæåíèå. Ìåòîäû èññëåäîâàíèÿ êà÷åñòâà, ñòðóêòóðû è ñâîéñòâ ìåòàëëîâ è ñïëàâîâ, îïðåäåëåíèå èõ òâåðäîñòè. Òåðìè÷åñêàÿ îáðàáîòêà äåôîðìèðóåìûõ àëþìèíèåâûõ ñïëàâîâ.
ó÷åáíîå ïîñîáèå [7,6 M], äîáàâëåí 29.01.2011
Ïîíÿòèå î æåëåçîóãëåðîäèñòûõ ñïëàâàõ. Ñòðóêòóðíûå ñîñòàâëÿþùèå ôåððè, öåìåíòèòà, àóñòåíèòà, ëåäåáóðè. Ñîäåðæàíèå óãëåðîäà â ïåðëèòå. Äèàãðàììà ñîñòîÿíèÿ æåëåçîóãëåðîäèñòûõ ñïëàâîâ. Ñèñòåìà æåëåçî-öåìåíòèò, ãðàôèò. Ëèíèÿ ñîëèäóñà êðèñòàëëèçàöèÿ ñïëàâîâ.
ïðåçåíòàöèÿ [1,3 M], äîáàâëåí 14.11.2016
- ãëàâíàÿ
- ðóáðèêè
- ïî àëôàâèòó
- âåðíóòüñÿ â íà÷àëî ñòðàíèöû
- âåðíóòüñÿ ê íà÷àëó òåêñòà
- âåðíóòüñÿ ê ïîäîáíûì ðàáîòàì
Источник