Дозаторы пищевых добавок в воду
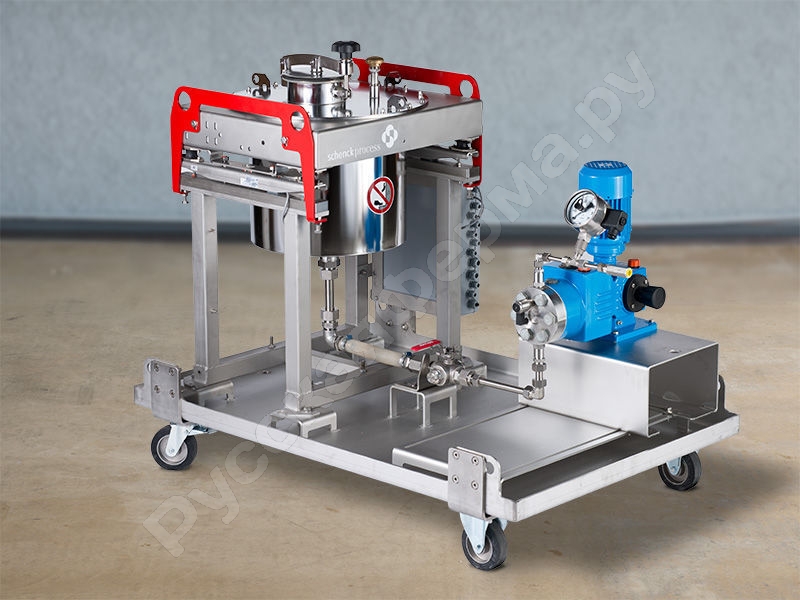
Дозатором называется аппарат по выдаче порций определенной величины. Дозирование проводится по весовым или объемным параметрам. В качестве рабочей среды может быть сыпучее вещество, жидкость или газ. Разные группы устройств функционируют с различной степенью точности.
Дозатор может работать с одним материалом или несколькими (соответственно, одно- или многокомпонентные), выдавать конечный результат одному или нескольким потребителям (одно- или многоканальные). У современных моделей есть компьютерный блок управления. Такая техника действует по заданной программе, выводит информацию на считывающее устройство и хранит ее.
Диспенсером (англ. Dispenser – дозатор) называется агрегат, выдающий фиксированное количество вещества (питьевая вода) или предметов (сигареты, наличные деньги). Микродозаторы (рецептурные) отличаются повышенной точностью при внесении малых порций, используются, в основном, в фармацевтике и пищепроме. Дозаторы соотношения автоматически поддерживают пропорциональный состав, увеличивая либо уменьшая количество одних компонентов, в зависимости от изменения других. Программные работают в заданной логической или временной последовательности. Мультиголовочный весовой дозатор (рис. 1) функционирует по принципу подбора подходящего сочетания из нескольких бункеров, для обеспечения необходимого веса.
Применение пищевых дозаторов
Дозаторы широко используются во всех отраслях промышленности: пищевой, фармацевтической, химической, металлургической, нефтегазовой, строительной и других. Они нужны там, где требуется отмеривание точных порций компонентов. А также – в процессе упаковки готовых жидких, сыпучих либо мелкоштучных изделий. Питатели подают материал к машинам непрерывного действия.
Основные виды дозаторов
Все дозаторы делятся на весовые и объемные. В первом случае порция выделяется после того, как дозирующий механизм (ДМ) получит количество материала, вес которого соответствует заданному. Во втором – то же самое, но по объему. У каждого вида есть свои достоинства и недостатки.
Объемные
Принцип работы объемного дозатора заключается в том, что продукт подается в мерную емкость и заполняет ее. Одна из популярных конструкций предусматривает ДМ в виде барабана с мерными стаканами. Последние состоят из двух частей. Перемещая подвижную, можно изменять объем. В дополнение к ДМ есть механизм регулировки и электропривод. Со стороны входа стаканы заполняются из бункера сыпучим материалом. На выходе отмеренная порция выгружается в упаковочный автомат. Преимущества объемных аппаратов:
Простота конструкции, надежная работа.
Высокая производительность.
Низкая цена.
Главным недостатком объемных дозаторов является их малая, по сравнению с весовыми, точность работы. Среди других минусов следующие:
Способ дозирования (по объему) не слишком популярный. Большинство продуктов (кроме жидких) продаются и, соответственно, фасуются по весу. В результате, при необходимости обработки другого вещества, его объем будет тот же, но вес – другой. Надо перенастраивать аппарат.
Проблема перенастройки в том, что диапазон регулирования небольшой, обычно в пределах плюс-минус 30%. Поэтому, например, механизм, рассчитанный на фасовку сахара в 500-граммовые пакеты, для развешивания в килограммовые мешочки уже не подойдет. Надо менять агрегат.
На трудносыпучих продуктах, таких как липнущий к стенкам стакана изюм или мало подвижные кукурузные палочки, объемное устройство, скорее всего, работать не будет.
Объем порции зависит от температуры и давления.
Весовые
Основной узел – электронные весы, оборудованные дополнительными устройствами для отмеривания порции.
В общем случае весовые дозаторы дискретного действия состоят из следующих узлов:
Устройство для подачи рабочего материала (питатель). Например, вибролоток.
ДМ, который отмеривает заданные порции. Это может быть калиброванная емкость (ковш), подвешенная на тензометрическом датчике, для контроля массы поступившего рабочего вещества. Датчик оборудован тензометром – прибором, который измеряет деформацию (в данном случае – наполнение); устройство преобразует полученную величину в электрический сигнал. На входе и выходе предусмотрены клапаны.
Регулятор – электронный блок управления (УЭБ).
Принцип работы следующий. На УЭБ выставляется вес дозы по двум параметрам: грубо и точно. УЭБ запускает вибролоток, который подает материал из бункера в ковш. После достижения первого порога, тензодатчик отправляет сигнал на УЭБ, амплитуда колебаний уменьшается. Продукт аккуратно досыпается до второго порога, после чего УЭБ выключает лоток, открывает ковш и высыпает материал в упаковочный автомат. Затем цикл повторяется.
Весовой дозатор ленточный работает аналогично, только вместо вибролотка применяется транспортер. После достижения предела «грубо», УЭБ уменьшает скорость его движения.
Весовой дозатор сыпучих материалов имеет более сложную конструкцию, чем объемный. Этим, во многом, объясняются его преимущества и недостатки.
Весовые дозаторы намного точнее, чем объемные. Допуски можно регулировать. Наличие порогов грубой и точной дозировки значительно повышает качество процесса. Есть и другие плюсы:
Благодаря использованию более распространенных весовых мер, ассортимент обрабатываемых продуктов значительно расширяется. Аппарату «безразлично», что делить на порции, он с одинаковым успехом будет взвешивать 200г. сахара или 200г. миндальных орешков. Смена продукта не играет роли.
Большой диапазон регулирования. На УЭБ выставляется любое количество порции – это можно делать, например, в пределах от 50г. до 1000г.
Нет проблем с трудносыпучими продуктами. Ковш одинаково хорошо заполняется изюмом, кукурузными палочками или рисом. Не имеет значения, насколько плотно фрагменты расположены в емкости – важен только вес.
Из основных недостатков, которые имеет весовой дозатор для сыпучих продуктов, можно отметить два:
Небольшая производительность. По сравнению с объемным (38 – 40 доз / мин), аппарат с одним ковшом (каналом) за минуту делает порядка 10 порций. Таким образом, чтобы «догнать» объемный, у весового должно быть, как минимум, 4 канала.
Одноканальный весовой дозатор где-то на 15% дороже аналогичного по вместимости ДМ объемного. Если надо уравнять производительность, то есть, взять четырехканальный, то цена получится выше в 4,5 раза.
Основные схемы устройств для жидкостей
Дозаторы для жидкостей, в отличие от сыпучих веществ, делаются, чаще всего, объемного типа. Это, в данном случае, более привычный для покупателя способ фасовки. К весовым относятся мембранные (рис. 2а) и бункерные (рис. 2б) системы. Обе работают циклично.
На дне емкости 1 мембранного аппарата на вертикальном стержне 3 расположена эластичная мембрана 2. Она воспринимает давление столба жидкости и передает его на весовой механизм 5. Для впуска и выпуска рабочей среды предусмотрены электромагнитные клапаны, которые управляются контактной колодкой 4. Величина порции зависит от суммарного веса гирь на механизме 5.
Бункерный агрегат относится к многокомпонентным. В приемном коллекторе 7 есть весовой рычаг 3, подвешенный на опорах 2. Одним концом он фиксируется на неподвижных блоках. Другим – давит на рычаг измерителя силы 4. Последний компенсирует массу ингредиентов, которые поступают в бункер 7 через клапаны.
Принципиальная схема объемных устройств для дозирования жидкостей указана на рис 3. Среди них барабанный работает непрерывно, остальные – циклично.
Постоянный уровень жидкости в емкости 7 дроссельного дозатора (рис. 3а) поддерживается при помощи поплавка 2, связанного рычагами с запорным клапаном. По трубе 3 с дросселирующим механизмом 4 жидкость выпускается наружу. Аппарат работает с высокой точностью, если температура будет стабильной.
В барабанном механизме (рис. 3б) на внешней поверхности быстро вращающегося барабана 1 образуется тонкий слой жидкости 2, который с помощью скребка 3 направляется в потребляющее устройство. В емкости поддерживается постоянный уровень рабочей среды. Барабан погружается на глубину 0,3 радиуса. Скорость вращения составляет от 2 до 3 м/с. Недостатки: большие размеры конструкции, сложность регулирования из-за нелинейной зависимости расхода от частоты вращения.
Объемные дозаторы на рисунках 3 в – и работают на основе слива жидкости из калиброванной емкости. Истечение может быть принудительное (шестеренные, поршневые) или свободное (прочие). Расход зависит от величины бака, плотности рабочей среды, частоты циклов «слив – заполнение».
Не смотря на то, что все эти аппараты порционные, при большой частоте циклов на выходе образуется практически непрерывный поток. Незначительные колебания расхода нивелируются в сливном канале. В результате любая из указанных систем может работать в качестве питателя с машиной непрерывного действия.
В поплавковом устройстве (рис. 3в) жидкость поступает в мерную емкость 2 через кран 7 и электромагнитный клапан 6. По мере наполнения бака, поплавок 1 всплывает, поднимая стержень 3 с контактом 4. Когда заливается заданное количество рабочей среды, контакты 4 и 5 замыкаются, электромагнитный клапан 6 перекрывает впускную трубу. Для слива кран 7 поворачивается на 90 град.
Черпаковый механизм (рис. 3г) работает по принципу периодического погружения калиброванных емкостей в бак с жидкостью, находящейся на постоянном уровне. Черпак 1 утапливается, заполняется и поднимается вверх. Рабочая среда сливается через трубку, размещенную в крепежном кронштейне. Для регулировки объема, в черпаке предусмотрены вытеснительные стаканы. Недостатки: при обработке вязких жидкостей переменной плотности, невозможно обеспечить точное дозирование.
В дозаторе фиксированного уровня (рис. 3д) мерная емкость 1 заполняется жидкостью из бачка 4 через впускной клапан 3 до тех пор, пока уровень в трубке 5 не сравняется с уровнем в бачке 4. Последний поддерживается на постоянной отметке. Набранная доза сливается через клапан 2. Для регулировки порции, трубку 5 поднимают или опускают.
В электродном дозаторе (рис. 3е) есть несколько электродов 4, из которых в сеть включен только один – тот, высота которого соответствует установленной норме. Жидкость поступает в емкость 1 через электромагнитный клапан 3. Когда уровень поднимается, раствор смачивает включенный электрод, сеть замыкается и клапан 3 закрывается. Слив – через клапан 2.
В стаканчиковой системе (рис. 3ж) два главных узла: неподвижный корпус 2 с отверстиями 3, 4 и 5, и вращающийся стакан 1. Отверстия предназначены, соответственно, для слива порции, удаления воздуха и подачи жидкости. Действия происходят в то время, когда паз стакана совпадает с очередным отверстием. Достоинства: простая конструкция, легкое обслуживание, быстрая регулировка. Недостаток – жидкость протекает через зазоры, из-за чего точность работы невысокая.
Две следующих системы – это распространенные конструкции насосов-дозаторов. Главными их параметрами являются напорно-расходные характеристики. Чем меньше сопротивление на выходе нагнетательного рукава, тем выше подача.
Шестеренный дозатор (рис. 3з) состоит из корпуса 3, в котором вращаются две взаимно зацепленные шестерни – ведущая 1 (ротор) и ведомая 2 (замыкатель). Когда их зубья напротив впускного патрубка выходят из зацепления, образуется разрежение. Жидкость всасывается внутрь. Затем шестерни перемещают ее к выпускному патрубку. Там они входят в зацепление, давление повышается, рабочая среда выталкивается в нагнетательную трубу.
Когда в поршневом автоматическом дозаторе (рис. 3и) поршень 1 движется вправо, создается разрежение. Клапан 3 закрывается, клапан 2 открывается, жидкость заполняет рабочую камеру. Затем поршень идет влево. Клапан 2 закрывается, клапан 3 открывается, жидкость под давлением выталкивается в выпускной патрубок. Преимущества: стабильный расход, не смотря на переменное сопротивление в нагнетательной магистрали. Точность дозирования высокая. Недостаток – пульсирующая подача. Для большей равномерности, применяются многопоршневые насосы, установленные на коленвал, что обеспечивает работу с фазовым сдвигом.
Массовые и шнековые дозаторы
Нередко отдельным видом, наравне с весовыми и объемными, считаются массовые дозаторы. При этом информативно утверждается, что масса в данном случае измеряется в кубических метрах. А производительность аппарата – в куб.м./час.
Масса – это вес тела, деленный на ускорение свободного падения (m = P / g). Ее можно выразить в силовых килограммах (1 кгс = 10 Н). Основным узлом такого устройства является массовый кориолисовый расходомер (рис. 4), из-за чего вся конструкция и получила свое название. Принцип его действия заключается в том, что поток рабочего вещества, движущийся внутри U-образной трубки, создает кориолисову силу. Она сопротивляется механическим колебаниям данной трубки. Из-за этого происходит изменение фаз, пропорциональное весу прошедшего материала. Чтобы узнать количество (массу) вещества, достаточно замерить фазовый сдвиг. Приборы отличаются высокой точностью, не зависящей от вибрации труб, температуры и давления. А также надежностью и долговечностью, потому что не имеют движущихся частей. Могут работать с высоковязкими средами. Но отдельным видом они не являются, а относятся к весовым устройствам.
То же самое можно сказать и о шнековых дозаторах (рис. 5), которые также иногда считают отдельным видом. Они относятся к объемным, а наличие шнека – всего лишь особенность конструкции. Такие аппараты работают с сыпучими материалами. Главное преимущество – простота устройства и обслуживания. Среди основных недостатков – небольшая точность, которая еще и сильно зависит от погрешностей, допущенных при изготовлении шнека. Если плотность продукта неравномерная, точность дозирования – крайне низкая.
Классификация дозаторов пищевых жидкостей по другим признакам
Кроме деления на весовые и объемные, существует еще около двух десятков признаков, по которым можно классифицировать дозаторы. Ниже приведено несколько основных.
По степени автоматизации – ручные, полуавтоматические и автоматические. Первые используются в строительстве, металлургической и других отраслях промышленности. Доза отвешивается вручную. Они малоэффективны, поэтому работают в лабораториях или на участках с простой технологией и низкой производительностью, где операции выполняются периодически и на каждую отводится достаточное количество времени. Например, для подачи фракций в бетономешалку.
Автоматические дозаторы – сложные устройства. Они работают с заданной точностью по схеме непрерывного цикла. Кроме дозировки, обеспечивают укупорку тары и ее ополаскивание. Оператор осуществляет только общее управление процессом. Это высокопроизводительные аппараты, подходящие для крупных компаний с большими объемами работ. Основной недостаток – высокая стоимость. Кроме того, у многих моделей ассортимент продукции, фасуемой в автоматическом режиме, относительно небольшой.
Полуавтоматические аппараты более простые и дешевые, чем автоматы, хотя их производительность несколько меньше. Они легко монтируются и быстро перенастраиваются с одного продукта на другой. Конструкция может быть разной. На большинстве современных моделей, применяемых в пищевой промышленности, оператор только устанавливает пустую тару и убирает наполненную. Изредка – еще и запускает процесс фасовки.
По назначению – дискретные (порционные) и непрерывного действия (питатели). Первые дозируют материалы равными долями, через одинаковые промежутки времени. Функционируют в цикличном режиме. Принцип работы описан выше.
Агрегат непрерывного действия (рис. 6) представляет собой транспортер с расположенным над одним его краем бункером с материалом. Лента смонтирована на весоизмерителе с тензодатчиками. Также имеется датчик скорости движения ленты. Сыпучее вещество подается через шиберную заслонку, формируется так, чтобы насыпанная полоса получилась определенной ширины и высоты. Сигналы от датчика скорости и весоизмерителя отправляются в процессор. Там они обрабатываются и посылаются на инвертор (частотный преобразователь). Последний управляет мотор-редуктором так, чтобы производительность агрегата была стабильной и равнялась заданной.
По типу привода: электрические, гидравлические, пневматические, комбинированные.
По виду дозирующего узла: дозаторы поршневые, мембранные, плунжерные, шланговые, сильфонные, винтовые, шестеренчатые, шнековые, с мерной емкостью, ковшовые.
Исполнение привода может быть, как стандартным, так и пылевлагонепроницаемым, искро- или взрывобезопасным.
Техническое обслуживание дозаторов на пищевых производствах
Правильное и своевременное ТО увеличивает рабочий ресурс аппарата, сокращает количество поломок. Оно делится на ежедневное (ЕТО) и периодическое (ПТО), включает в себя операции по осмотру устройства, проверке его работоспособности и техсостояния, а также ухода за прибором.
ЕТО выполняется после окончания рабочей смены. Устройство надо промыть. Затем осмотреть аппарат, для обнаружения явных дефектов, проверить заземление, электропроводку, отсутствие механических повреждений. Выявленные неполадки – устранить.
Периодичность ПТО – обычно раз в месяц. Делается ЕТО, после чего – другие мероприятия, согласно перечню, приведенному в инструкции к прибору. При необходимости, на месте выполняется текущий ремонт (ТР). Для этого проводится дефектовка вышедших из строя или изношенных деталей, после чего они заменяются. Если своими силами сделать ТР невозможно, обращаются в сервисную службу.
Источник